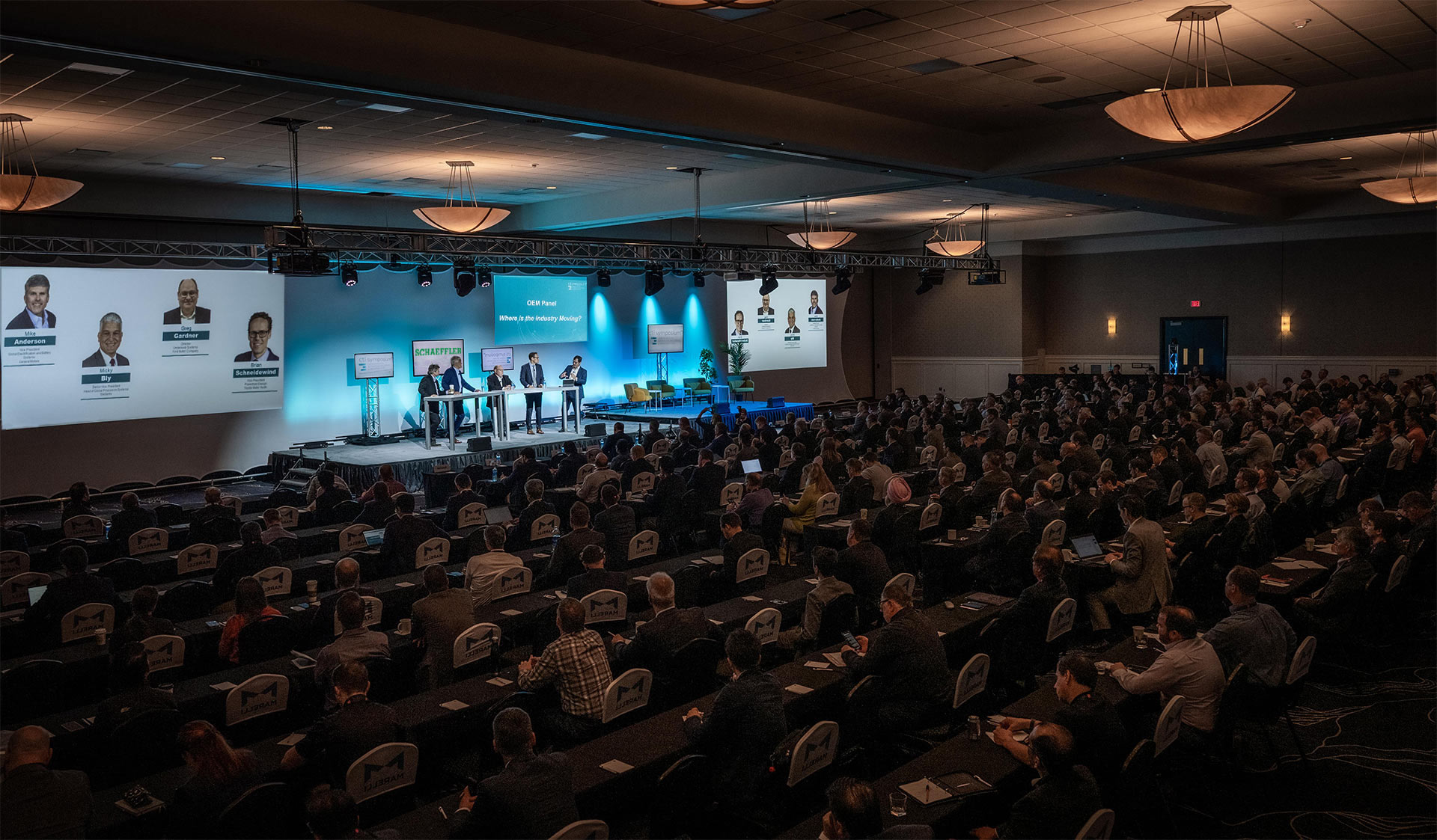
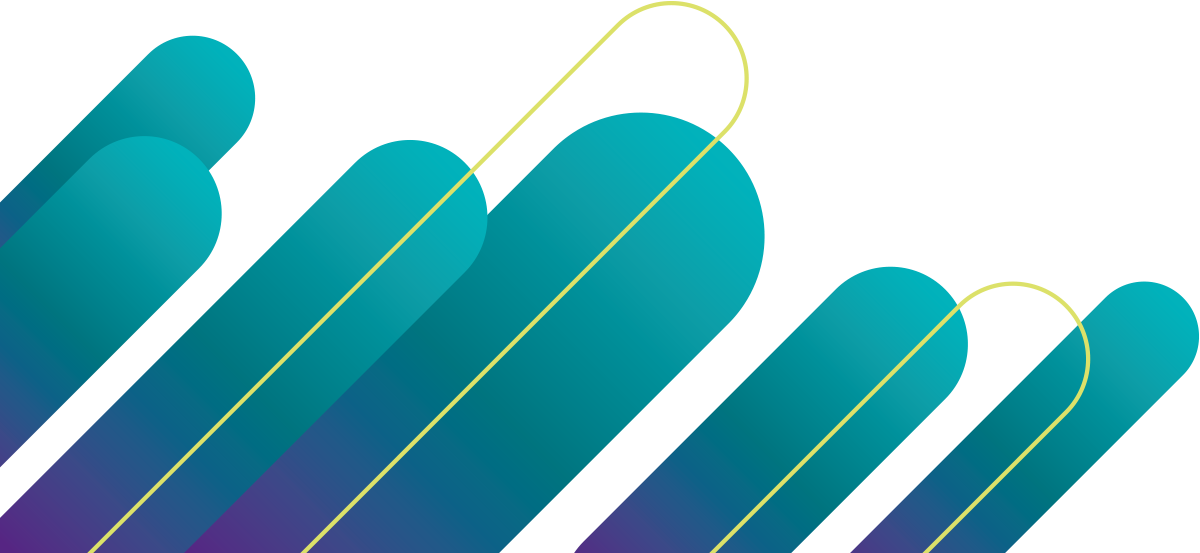
DRIVING TOMORROW − POWERTRAIN & MOBILITY REDEFINED
International Congress, Expo and Ride & Drive
19 & 20 May 2026, Novi, MI, USA
CTI SYMPOSIUM USA IS THE KEY MEETING POINT FOR GLOBAL FORWARD THINKERS IN AUTOMOTIVE POWERTRAIN DEVELOPMENT – FROM PASSENGER CARS TO HEAVY-DUTY VEHICLES.
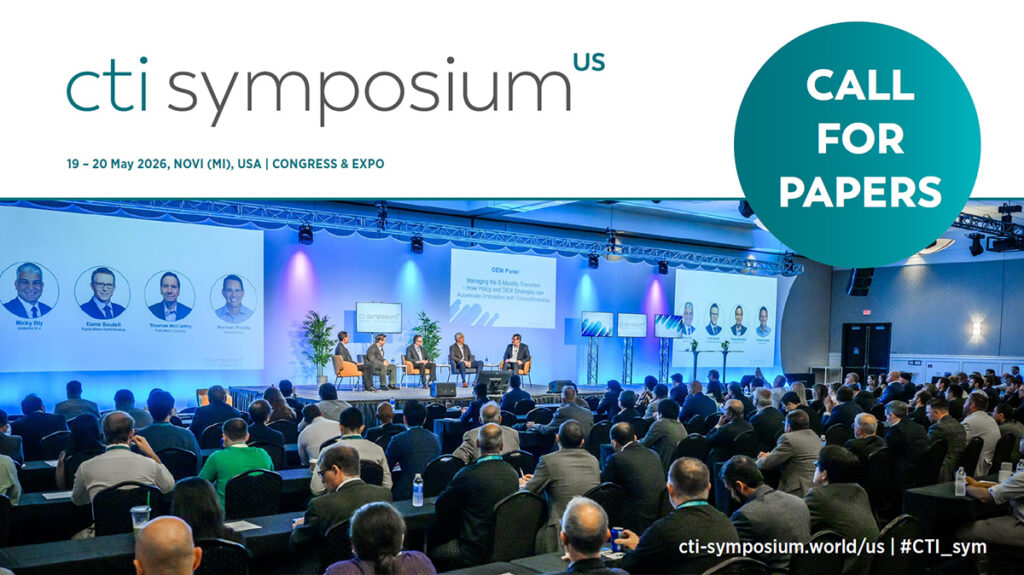
For the CTI SYMPOSIUM USA 2026, we invite OEMs, suppliers, engineering services, start-ups, and research institutions who are working on the redefinition of automotive powertrains and mobility to submit your topic proposal. We will continue to explore advancements in Internal Combustion Engine (ICE), Battery Electric Vehicle (BEV), and Hybrid Vehicle technologies, with a focus on drivetrain systems, e-motors, power electronics, and battery systems.
New in 2026: Smart Chassis Meets Smart Powertrains
Moreover, for the first time, CTI USA will spotlight innovations in chassis-powertrain integration, from motion control strategies, steer-by-wire and brake-by-wire to active suspension systems and integrated development methods. Why now? Because chassis and electric powertrains share common challenges: precise motor control, real-time responsiveness, and the highest levels of functional safety.
INTERNATIONAL DELEGATES, EXHIBITORS & SPEAKERS
EXECUTIVE VIEWS
DEEP DIVE TECHNICAL SESSIONS
25+ HOURS OF CONTENT & NETWORKING
CTI RIDE & DRIVE
Impressions 2025
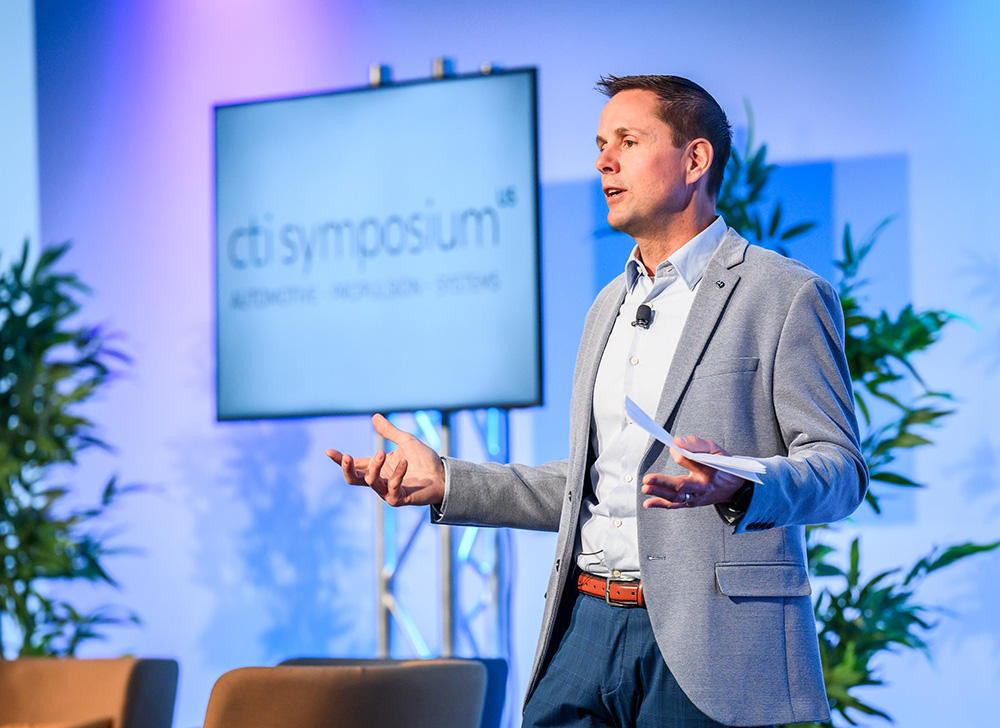
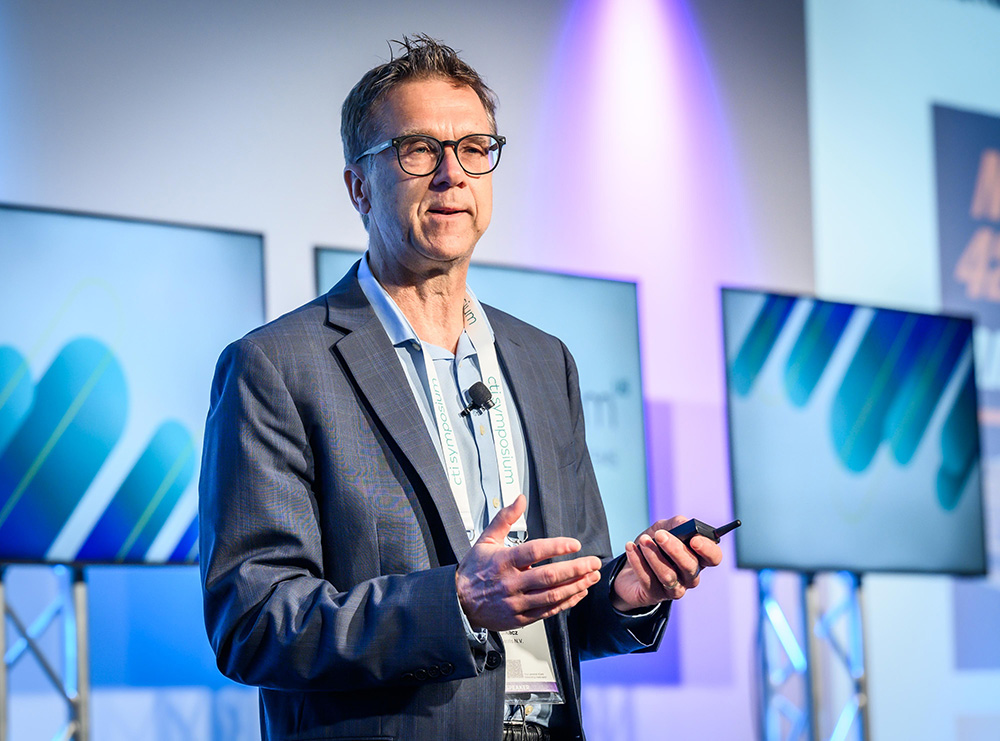
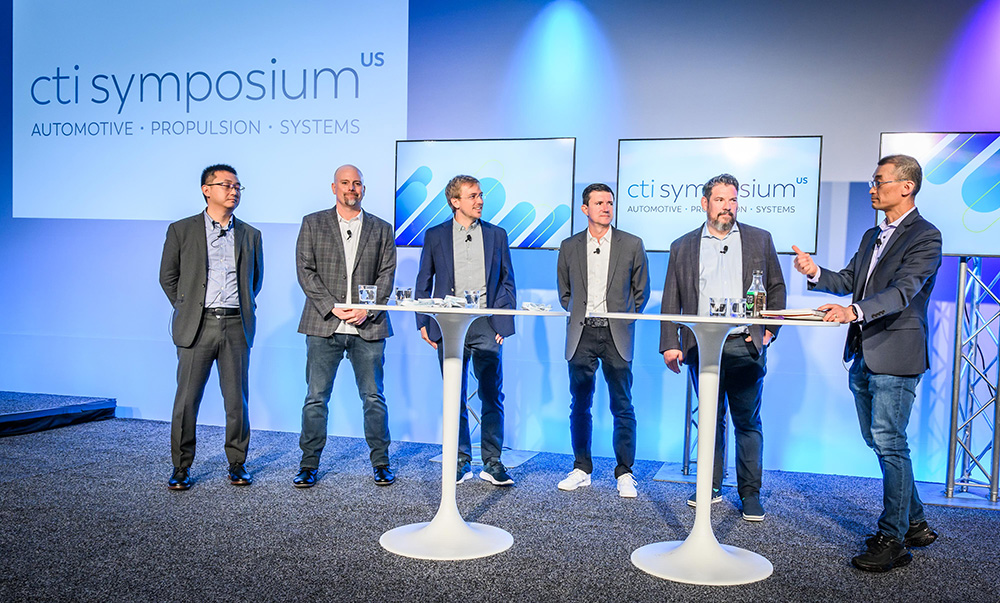
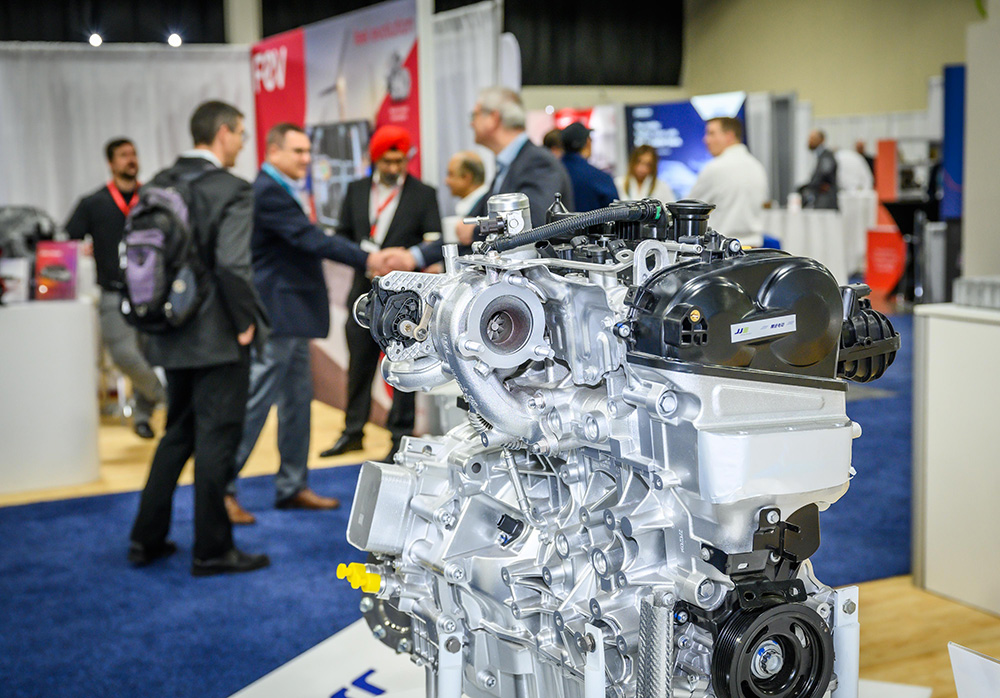
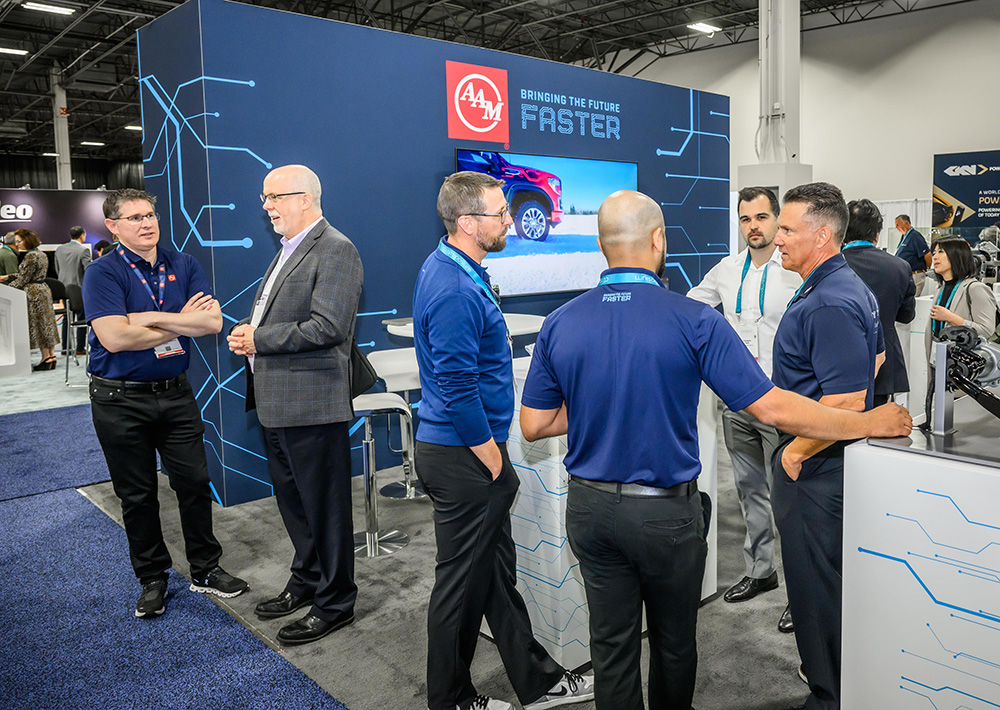
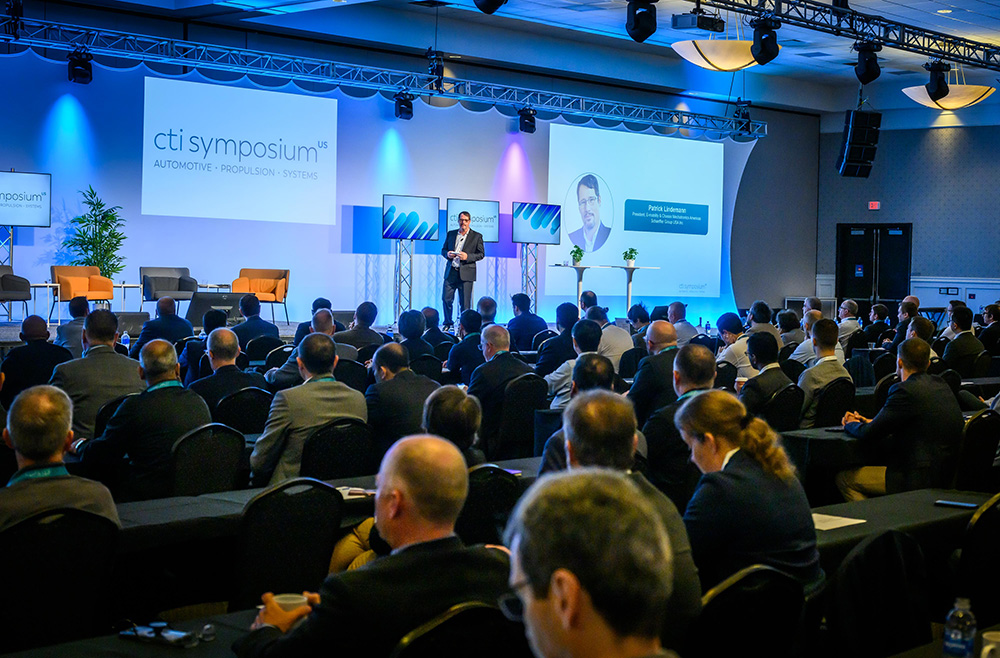
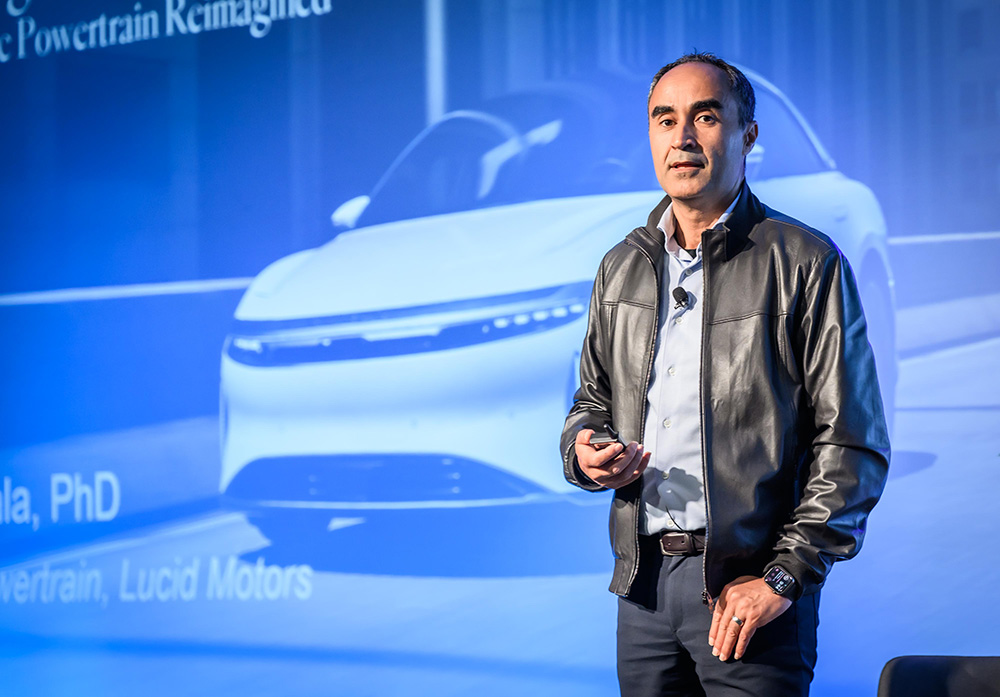
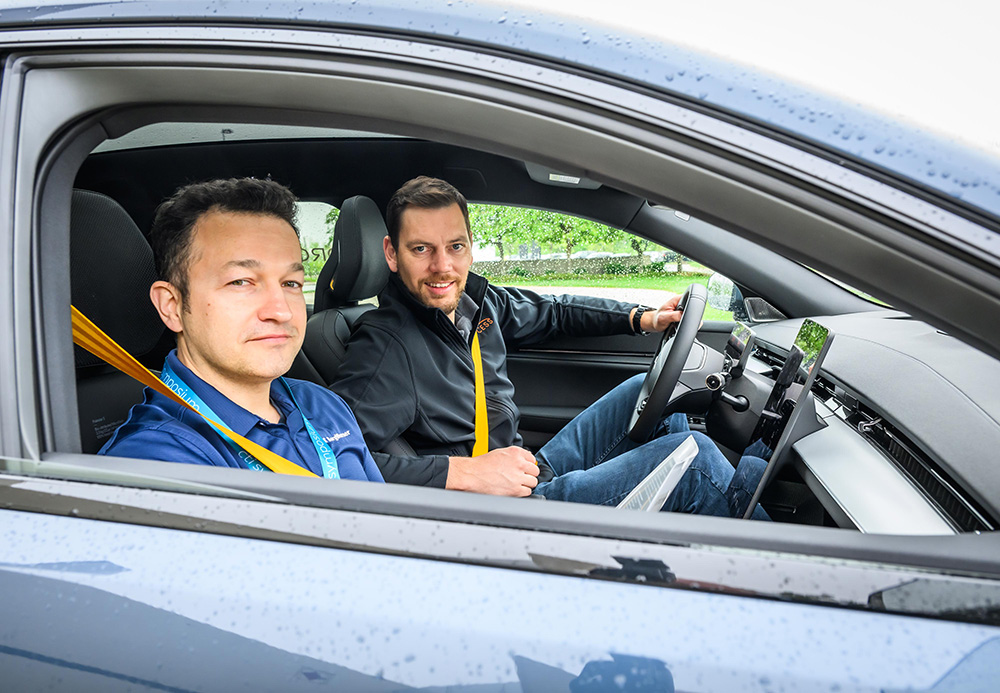
PLENARY SPEAKES AND PANELISTS 2025
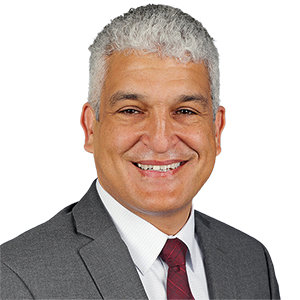
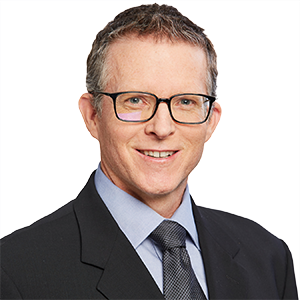
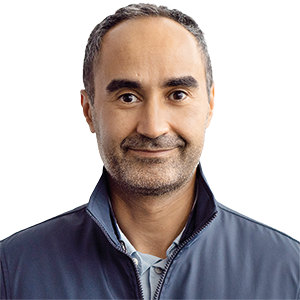
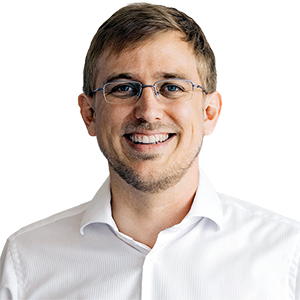
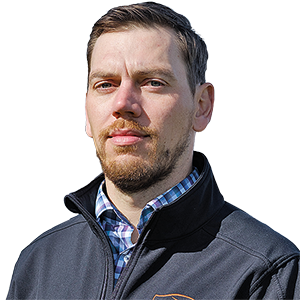
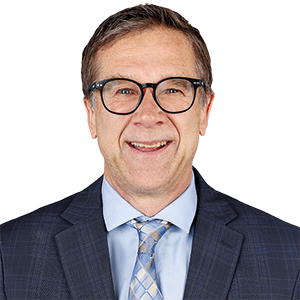
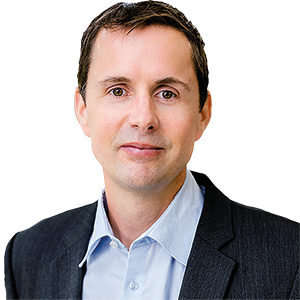
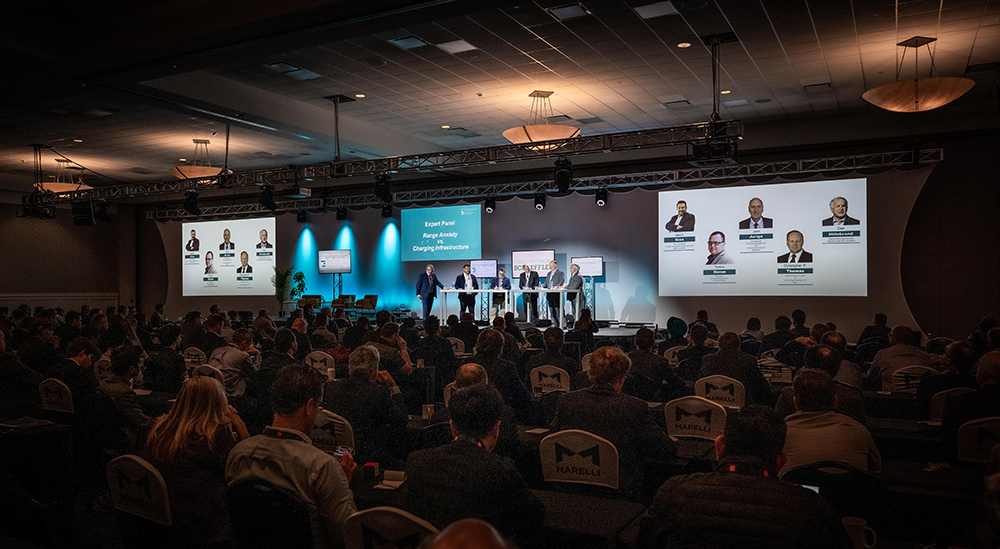
The Expert Summit for a Sustainable Future Mobility
Only together we can create a sustainable future mobility. CO2 reduction is critical for automotive drivetrain. Here the battery electric drive using renewable energy is the focus. What can we do to increase efficiency and reliability, reduce cost and at the same time reduce the upstream CO2?
At CTI SYMPOSIUM the automotive industry discusses the challenges it faces and promising strategies. Latest solutions in the fields of electric drives, power electronics, battery systems, e-machines as well as the manufacturing of these components and supply chain improvements are presented. For the bigger picture market and consumer research results as well as infrastructure related topics supplement the exchange of expertise.
CTI SYMPOSIA drive the progress in individual and commercial automotive transportation. Manufacturer, suppliers and institutions are showing how to master the demanding challenges.
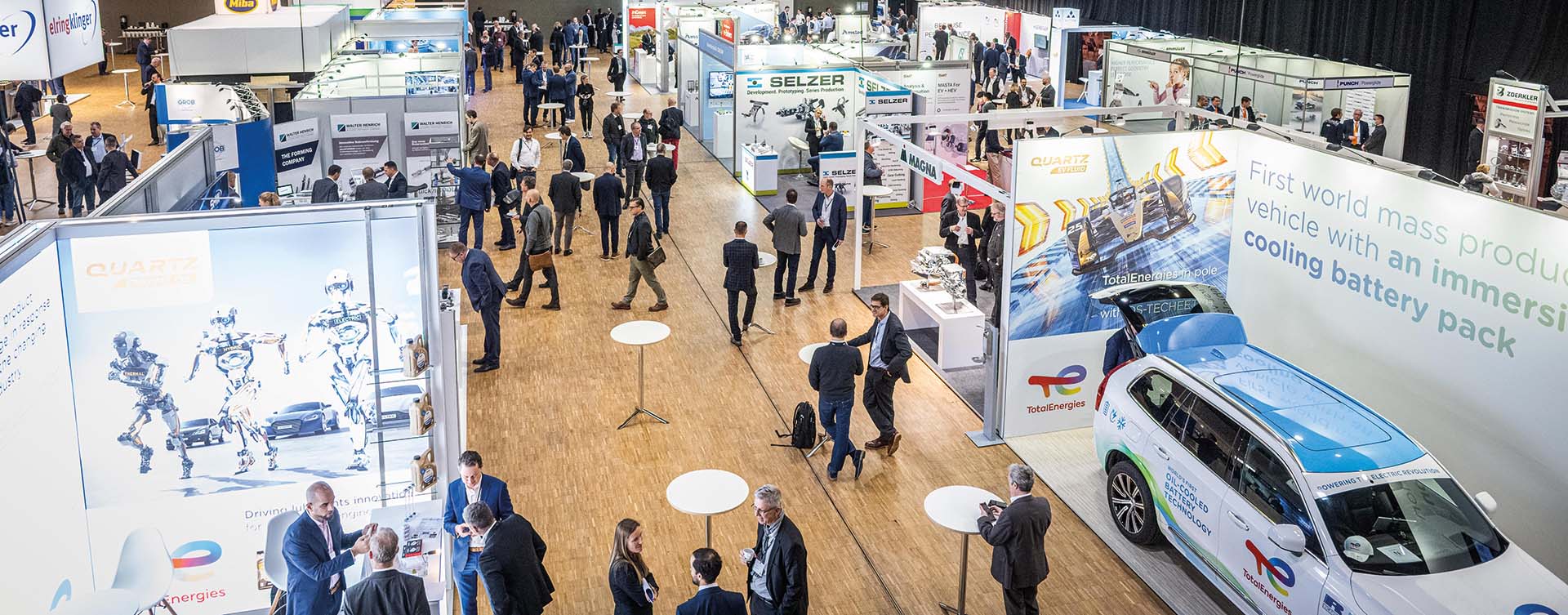
Specials
- Deep Dive Sessions on Passenger Cars and Commercial Vehicles
- OEM & Supplier Panels
- Explore the latest products and innovations in the accompanying exhibition
- Ride & Drive: Enjoy a full-feature tech experience in series and demo vehicles
- Women@CTI Special Program
- Start-up Area
- Extensive networking opportunities
- Outstanding evening event
Topics
- Transformation of the Automotive and Supplier Industry
- Markets. Policies and Sustainability
- Latest Electric, Hybrid and ICE Propulsion Technology
- Passenger Cars and Commercial Vehicles
- E-Motors & E-Motor Development
- Traction Batteries
- Power Electronics
- Chassis and Electrified Powertrain Integration (NEW)
- Thermal Management, Cooling and Lubricants
- AI in Powertrains
- Virtual Development Processes
- Cost Reduction
- And more
Follow us on LinkedIn
Updates from cti-symposium.world
World’s First Disconnect and Locker Combo Differential (DL ComboTM)
JJE’s New Solution for High-Efficiency, High-Capability eAWD Dr. Yang Cao, Transmission Manager, JJE Technologies JJE Technologies proudly presents the DL Combo™, the industry’s first fully integrated disconnect and locker differential system. By combining eDisconnect and eLocker functionalities into a single, compact unit, this innovation provides electrified all-wheel-drive (eAWD) vehicles uncompromised off-road capability and low energy […]
Continue readingOEMs should be more aggressive about an ‘AI First’ approach
William Wei, EVP and CMO, Skymizer Generative AI has made massive progress in the last few years and may substantially change how drivers interact with their cars. We talked to William Wei, EVP and CMO at Skymizer, an AI infrastructure company based in Taiwan. Mr. Wei gave us some interesting insights into how in-vehicle AI […]
Continue readingElectrification, digitalization, and the circular economy go hand in hand
Interview Rudolf Bencker, Senior Vice President Inventions and Innovations Management, powertrain BMW has steadily grown its sales of battery-electric vehicles but stands by its Policy of powertrain technology openness. We spoke to Rudolf Bencker, Senior Vice President Inventions and Innovations Management, about the company’s powertrain and digitization strategies, starting from early research.
Continue reading