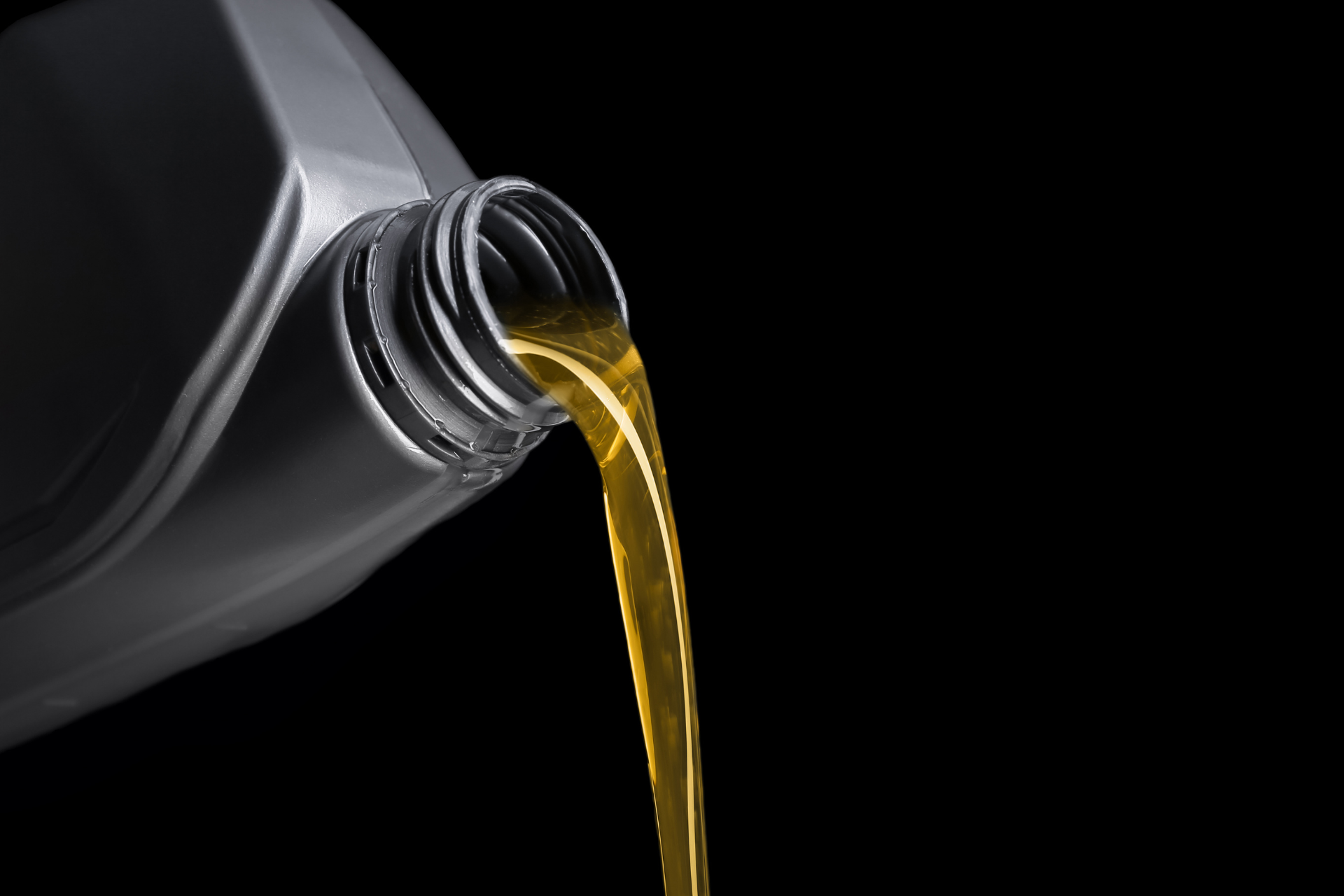
Specialized e-fluids play a key role in electric drives. Whereas ICE drives only need a water pump and a radiator, modern electric powertrains require complex thermal management systems. Using immersive cooling with ultra-low viscosity e-fluids, developers can achieve highly integrated, highly efficient 3-in-1 e-drives. All these topics, with their many facets, are well worth exploring in depth.
CTI SYMPOSIUM GERMANY 2024: The big picture, plus all the details
The transition to sustainable mobility is one of today’s key issues, and one to which we are deeply committed. In 14 Deep Dive sessions with over 80 specialist presentations, our focus in Berlin will be on two things: precise research results, and real-life products. Because these individual steps are what bring us closer to our ultimate goal.
New technology analyzes heat management, including fuel efficiency
Hyundai Transys has developed a new analysis technology that predicts the heat transfer performance of 3-in-1 electric powertrains, quickly and accurately. The method that Sang-Min Park (Hyundai-Transys) will present in Berlin analyzes the heat management (heating/cooling) and fuel efficiency of a 3-in-1 system in real time under specific driving conditions, based on the torque requirements and rpm of the powertrain. The new technology involves three elements. First, the company developed a heat transfer analysis model that would run as fast as possible. Second, they added a model that can accurately predict the temperature of each individual powertrain component. And third, they developed an integrated model that reflects the results of heat transfer in the powertrain when analyzing vehicle fuel consumption. To verify the method’s fuel efficiency predictions, Hyundai compared them with an analysis of heat transfer performance (heat exchanger capacity, etc.) of a Hyundai IONIQ 5 in MCT mode. As Sang-Min Park will explain, developers have already used the new analysis technology on Hyundai Transys HEV and EV powertrains, to hone their competitive edge.
Immersion cooling for batteries: More efficiency, more safety
Direct immersion cooling is becoming more widespread in electric powertrains. In the field of battery technology, however, developers remain sceptical due to the hardware adjustments required. But if Ilaria Travi (Petronas) has her way, that could soon change. In the study she presents in Berlin, she will show the real-life benefits of immersion cooling. Petronas ran flow simulations to compare the results of indirect cooling with water/glycol coolant, and direct cooling with various dielectric fluids. The results were then validated by testing real battery cells with different geometries, cylindrical and pouch cells. The data shows that in a standard WLTP cycle, immersion cooling is up to 5% more effective than standard indirect cooling.
Petronas also ran thermal runaway studies to evaluate the safety benefits of immersion cooling. In real-life thermal runaway tests with cylindrical NCA and NMC cells, a central cell was heated to trigger thermal propagation. The results indicate that direct dielectric cooling can delay thermal runaway by up to six minutes. This would give vehicle occupants valuable time in which to escape, and offer the battery management system a window in which to secure the system.
New valve block type solves issues in the refrigerant circuit
Adding heat pump functionality to the refrigerant circuits of BEVs makes them significantly more complex. As Frank Hohmann (IAV) will describe in Berlin, IAV GmbH has now developed a new type of valve block, together with a customer. The aim was to simplify the refrigerant circuit – and hence reduce system costs – via high levels of integration. Unlike conventional solutions, where each changeover valve requires a separate electric actuator, the new valve block requires just one electric actuator overall. So by eliminating actuators, connections and controls, the new development reduces costs.
The refrigerant valve block was developed on the basis of the R744 refrigerant circuit in the VW ID.3. It can also be used in a modified form for other refrigerant circuits and common refrigerants, such as R1234yf and R290. Frank Hohmann will present the innovative valve block in detail, and will round off his presentation with an outlook on the next development steps.
A successful co-operation: Developing a tailor-made Electric Driveline fluid for an e-axle platform
New technologies for innovative e-drives bring fresh tribological challenges in their wake.
Building on their long-standing cooperation, Magna Powertrain and FUCHS have now implemented a new project. This involves harnessing their broad experience in conventional drive technology to develop an innovative electric driveline fluid (EDF) that is perfectly tailored to Magna Powertrain’s e-drive platform. As Thomas Kraft (FUCHS Lubricants Germany) will explain in Berlin, the main aim was to find solutions in four key areas: optimized oil viscosity for efficiency, wear protection and NVH; oil foam formation and entrainment at higher e-machine rpm; compatibility with copper and other e-machine materials; and clutch performance with torque vectoring. The new fluid – FUCHS BluEV EDF – ticks all those boxes, and is suitable for use across the entire Magna Powertrain e-drive platform portfolio.
Robust e-fluid cooling concepts for e-drives with high power density
Next-generation EVs require highly integrated powertrains that can perform on a par with their larger counterparts, yet dissipate heat within a smaller volume. Dr Stephan Schlimpert (Flanders Make) believes that directly oil-cooled motors are a promising solution, but says some challenges still need to be overcome in order to make them robust. By way of a solution concept, he will present a robust design methodology, coupled with novel cooling and non-contact sealing technologies. The methodology was developed in close cooperation with Lubrizol, and included rigorous testing and analysis of material compatibility with a dielectric oil under various operating conditions. Using the novel Design Guide and the non-contact sealing concept, a robust e-motor with modified robust materials was created. It has a power density of 50 to 70 percent, and incurs no additional churning loss from oil penetrating the air gap. The Guide that Dr Schlimpert will present in Berlin sets out a strategic approach to fluid powertrain compatibility without the need for costly design iterations. It also outlines the next steps towards a unified e-fluid solution for electric vehicles.
Optimizing e-fluids: Do standardized drive cycle tests (WLTP) tell the whole story?
OEMs are switching to lower viscosity fluids, and wish to quantify potential efficiency improvements in electrified powertrains without compromising on hardware protection. For this, as Andrew Wood (Infineum UK) will explain in detail, WLTP tests alone are not enough. The only way to obtain sufficiently differentiated test results is by combining WLTP with steady-state tests that cover the entire operating range. Infineum has conducted both WLTP and steady-state tests in electric drive units at different temperatures, loads and speeds. The company has also examined the effects of viscosity (low and ultra-low viscosity fluids), the quality of the base material (Class III and IV base material), and boundary friction additives. In addition to efficiency gains, the tests also examined the impact on hardware protection. In Berlin, Andrew Wood will be discussing a wealth of individual results in detail. For example, it can be proven that boundary friction additives significantly improve efficiency, especially at low speeds and high temperatures –a fact that WLTP tests do not reveal. The new findings can assist companies in developing special lubricant formulations for high-efficiency e-drives. Infineum is currently in contact with a number of customers and OEMs to assess their interest in this approach.
Diverse challenges: Lubricant solutions for electrified heavy-duty drivetrains
The wide range of electric motor concepts and architectures for on-highway applications calls for various specific lubricant solutions. As the market leader, Shell has now launched a new e-fluid portfolio with tailor-made products for wet and dry electric motors. In his presentation, Leonard Kieckebusch (Shell Global Solutions) will discuss the demands that different electric HD drivetrain systems make on specific e-fluids. With wet electric motors, for example, what are the trade-offs in terms of wear protection, corrosion protection and electrical properties?
The specific test procedures used in the heavy-duty sector are equally fascinating. Shell uses drivetrain test benches to compare the properties of candidate fluids at various relevant load points. These load points vary from city buses to long-haul transport, and must be carefully selected in collaboration with the OEMs. When developing new lubricants, the overarching focus is sustainability. In Berlin, Leonard Kieckebusch will present examples of circular economy initiatives and low-carbon components for e-fluid formulations, such as reclaimed base oil.
Ultra-low viscosity e-fluids: Reduce to the max
Low viscosity e-fluids offer better heat management, and can further improve the efficiency of directly cooled electric motors. Hence, developers now strive to take viscosity values as low as possible. But as Dr Amanda Eastwood (Lubrizol) will ask at the start of her presentation: “How low can we go?” Lower viscosity can sometimes weaken the strength of the oil film, and to protect the hardware, appropriate wear behaviour – as defined by original equipment manufacturer (OEM) engineers – must be ensured. With this in mind, Dr Eastwood will discuss and answer the question of what viscosity values can actually be achieved in real life. As she will show, new advances in e-fluid powertrain technology mean there is no need to compromise on other performance aspects, such as transmission wear and bearings protection. Dr Eastwood will conclude her analysis by sharing results on how the new e-fluid technology performs in real-life e-hardware.
Welcome to the CTI Symposium Germany!
Be there on December 3rd and 4th, 2024, when decision-makers and experts share their cutting-edge insights into the topics that are moving our industry. Discover your personal highlights in a two-day program packed with special Deep Dive sessions, lectures and discussions – both in the plenary session, and at CTI EXPO.