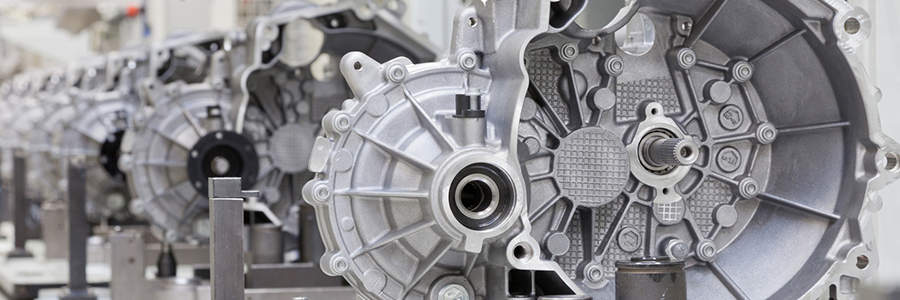
”To achieve consistent quality, you need to continuously synchronize customer expectations and your search for optimization potential”
said Tomoyoshi Sator, Senior Vice President Corporate Quality Assurance Division, Jatco Ltd. at the 11th CTI Symposium USA in May 2017 in Novi, Michigan. Jatco’s example is another clear reminder that tomorrow’s biggest challenge involves continuously self-optimizing internal processes (particularly in production), not meeting requirements in different markets or achieving breakthroughs in drive system frugality. That means manufacturers need to work out how to ensure consistent quality and efficiency across all international facilities – and also bring new and promising methods into production.
At the CTI Symposium on 5/6 December 2017, you’ll have another opportunity to verify these insights at first hand. The ‘Production’ session will present innovations ranging from material machine cutters through self-measuring transmission components to efficient factories. And at last, big companies too are showing that 3D metal printing is ready to enter mass production.
3D metal printing in mass production
Sintered powder metal components are becoming more widespread. In Europe, they often feature in manual and DCT transmissions; in North America and Asia, they are used for planet carriers, clutch components and gearwheels. Sinter technology offers a degree of freedom that makes highly complex 9 and 10 ratio transmissions possible by creating components whose power density exceeds that of conventionally produced items. [Stackhole Powertrain] 3D metal printing has great potential in terms of weight savings, more efficient ICEs and transmissions, noise reduction and functional integration. But the degree of freedom it offers also calls for a complete re-think in the way we design and produce standard mechanical components – and opens the door for totally new components while simultaneously reducing time-to-market. Using the example of electric powertrain components, Porsche Engineering will demonstrate how hitherto-impossible transmission construction solutions can now be achieved using new materials. At the same time, it’s becoming clear that progress depends on the material layering speeds of additive manufacturing technologies, and that hybrid production and joining procedures are urgently required in order to achieve mass production. [PORSCHE] Halving the process step count in manufacturing
Growing personalisation, driven by the customer expectations described earlier, means you need to produce a wide range of product variants. That trend will likely grow further in years to come. Yet mass production methods are already running flat out, particularly in terms of combining high productivity with maximum flexibility. As a result, new process technologies must integrate processes to eliminate superfluous steps, make work and quality creation more compact, and align them more closely. A few players are already demonstrating how well this can be achieved. Using the example of powertrain component manufacturing at Volkswagen Group, the production researchers from Hanover – together with various companies from the tool tech, measuring tech and machine making sectors – will show how combining processes from two high-performance manufacturing procedures can eliminate 50% of the steps while simultaneously making production more flexible. [IFW, VW] Self-measuring components
While measuring and quality monitoring process steps are certainly necessary, they also account for a large share of manufacturing times. When producing transmission components, many rotating parts need to be checked and monitored in cycle times. The only way to meet production requirements is with contactless measuring methods that do not require individual transmission components to be dismantled. [Jatco] In addition to providing process status data during production, measuring methods that are built into components can also yield data throughout the whole lifecycle of the vehicle, enabling failures or service intervals to be anticipated more accurately. For example, wear-resistant thin-layer sensor systems can monitor high-stress components such as bearings to measure load distribution and record characteristics data in direct contact with the rolling element. Other conceivable applications include bearing sensors and spacer washer sensors, or even using manufacturing tools themselves as sensors. [IST] Energy-efficient factories
Once you consider the whole factory instead of single components, the focus increasingly shifts to the specific energy footprint per automobile produced. Today, automotive plants can be benchmarked using energy efficiency indices. However, several factors affect a factory’s energy consumption. These include location-specific climate factors, production depth, various product characteristics and production technologies, and capacity and production planning parameters. Using the example of Opel’s auto factories, this year’s CTI will show how you can optimize not just powertrain components, but entire factories to keep them competitive in years to come. [OPEL]
by Dr Anke Müller, TU Braunschweig
The production session (including the above cited speakers and companies) will be one out of 16 technical sessions at the 16th CTI Symposium in Berlin this year. With more than 1350 participants from 25 countries who are expected to attend this year’s event from 4 – 7 December 2017 the Symposium has been growing continuously over the last years and has made it to the most important meet-ups for the industry.