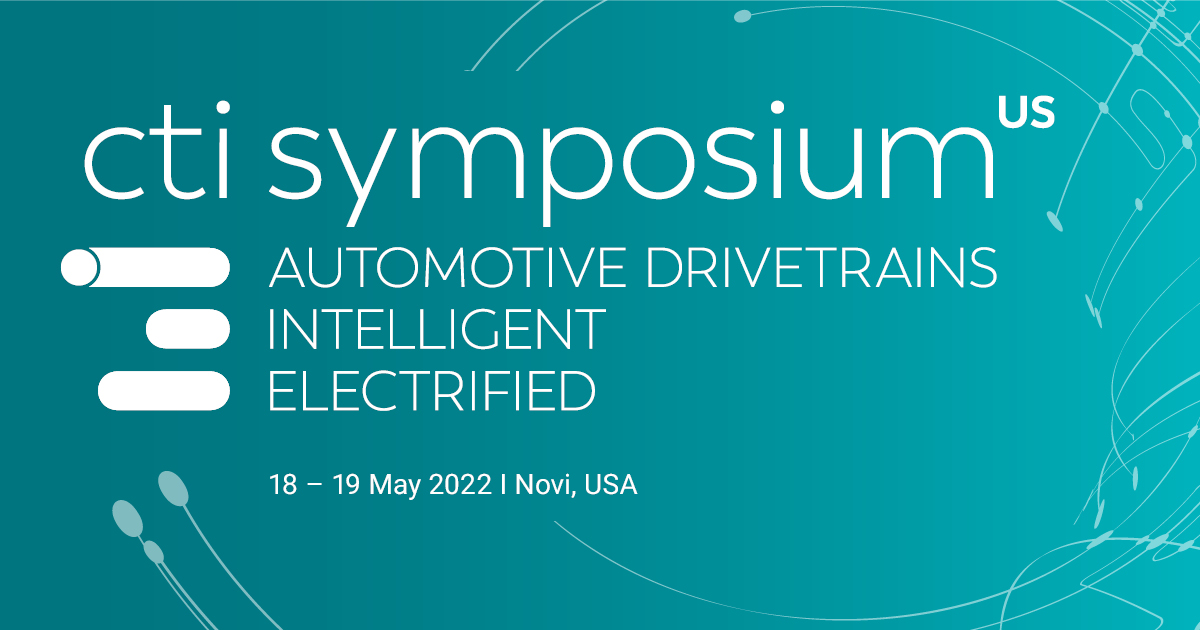
Technical progress knows no bounds, and it never stops. Every new benchmark inspires engineers to aim higher still. On the road to Net Zero Emissions, progress sometimes takes a big leap – and sometimes a series of small steps.
CTI Symposia – a forum for bold innovations
In our book, e-mobility is a daily struggle for the best idea. Different concepts (for example pure electric and hybrid drives) compete, and specific motor details (for example stator core and slot liners) are put to the test. The question of future E/E architectures also needs to be answered. For people who want to identify new trends early – and pursue them doggedly – our CTI Symposia are the ideal forum.
New development: a six-phase electric motor shines in a 48V system
48-volt systems in hybrid drives can play an important role in reducing fuel consumption and emissions. But so far, the relatively low output of 48V motors has been putting the brakes on efficiency.
Now a new development from AVL proves there is another way. The solution presented by Wilhelm Vallant (AVL List, Austria) is a 48V electric axle with up to 32kW peak power, installed in a P4 configuration hybrid vehicle. To achieve that higher performance level with low torque ripple, the e-motor is configured with 6 phases and distributed winding. This technology takes the 48V system to the next level of electrification. By significantly improving vehicle performance in pure electric drive modes, it makes a greater proportion of driving locally emission-free.
Due to the high-current, low-voltage electric motor design, non-linearities in inductance and resistors can affect performance dramatically. In his presentation, Wilhelm Vallant will outline the various issues involved and describe the development process and characteristics of the technical solutions. The e-motor and inverter were designed as a system, using sophisticated simulations. Besides higher performance, designers also focused on maximum efficiency and excellent NVH behavior; manufacturing processes and cost factors also had to be considered. Special attention was given to the winding arrangement – a key factor for motor performance in low-voltage/high-current systems. As a result, the team was able to ensure that maximum performance (with minor deviations) is also available in series production.
Core problem solved: high-speed production of traction motor stacks with bonding varnish
How do you produce rotor and stator cores for traction motors at high speeds and volumes, at low costs and in perfect quality? In his presentation, Max Thieme (Schuler Pressen, Germany) describes the optimal solution for this challenging task.
First, the speaker will present and compare the basic methods for stamping sheet metal for electric motors. He will focus on ultra-modern bonding techniques such as interlocking, gluing and bonding varnish/Backlack, all of which can be used to combine metal sheets into a complete package. Bonding varnish in particular offers convincing benefits. Unlike interlocking and welding, this process rules out short circuits between individual sheets. As a full-area bonding method, it also outperforms gluing – no liquid can penetrate, and thermal conductivity and NVH behavior are both better.
Finally, Max Thieme will explain why progressive dies are the best way to produce traction motor stacks in typical quantities and sizes. This method kills two birds with one stone: high speed stamping, and high quality bonding. To eliminate the downside of handling separate sheets, a fully automated system collects sheets below the progressive die and brings them to the gluing stations in a controlled and secure manner. These gluing stations are freestanding units that offer full control over all process parameters such as pressure, temperature and time. The solution is usually offered as a turnkey system that covers everything from winding off the raw material to the finished laminate stacks. That said, retrofits for existing machines are also available.
Higher power density – innovative slot liners turn air into efficiency
As all designers of electric motors know, seemingly small improvements can yield tangible benefits. In his presentation, DeeDee Smith (Solvay Materials, USA) will show that optimizing the insulation materials used in electric motors is a good case in point.
Specifically, the issue concerns the slot liners that shield the stator core from the winding. As OEMs progressively migrate from 400 volt systems to 800 volts or higher, it’s becoming clear that traditional paper/paper laminate insulation is no longer ideal. To address that issue, Solvay has been working with e-motor designers to evaluate the suitability of Ajedium™ PEEK slot liners as a new high-voltage, high-temperature solution. As their findings show, Ajedium™ PEEK slot liners are an advanced alternative that combines excellent electrical and mechanical performance with greatly reduced thickness. In some cases, volumes can be reduced by up to one third, compared to established solutions.
Engineers can exploit this advantage to increase the motor’s power density, either by making the e-motor more compact or by using the free space in a way that enhances performance. The thermoplastic PEEK film is temp-resistant to 240 °C and offers improved thermal conductivity – more than three times that of current paper and paper laminate materials. This in turn helps to reduce overall motor temperature.
Free from domain boundaries – Bosch is backing a innovative E/E architecture
With the complexity of modern vehicle systems growing exponentially, the key challenge for electrical/electronic (E/E) architectures in e-mobility is how to keep that complexity under control.
In the strategy developed by Bosch, the VCU (vehicle control unit) plays a central role. As Nitya Hadya (Robert Bosch, USA) explains in his presentation, the VCU coordinates powertrain components or takes partial command of their functional scope. Examples include inverter and battery management systems, and transmission and engine management. Battery charging management (communicating with the charging station via a standardized interface) can also be integrated into the VCU.
This facilitates the introduction of new functionalities – including across existing domain boundaries – while also saving resources in subordinate control units. Thanks to modular, configurable hardware and software, the VCU can be designed flexibly to accommodate future requirements. The VCU-S in the presentation is designed as an Embedded Integration Platform that includes separate and independent software partitions within the controller. It delivers the necessary reduction in complexity while enabling fast, easy integration and updates, legacy software integration, multi-partner collaboration, coordinated security concepts and more besides.
The bottom line: this technology represents an evolutionary development that lets OEMs keep using existing software, tool chains and competencies, yet simultaneously spans an arc to a revolutionary E/E architecture of the future.
CTI SYMPOSIUM USA – good to see you again!
At long last, the CTI SYMPOSIUM in Novi (18–19 May 2022) will take place again as a live event. Come and enjoy a top-class program with prominent guests. Be there when tomorrow’s trends are discussed in the plenum and in the eight technology sessions. Explore the CTI SYMPOSIUM EXPO, our fascinating showcase for innovations. And broaden your horizons – and your network – in dialog with international experts and fellow participants.
Welcome to CTI SYMPOSIUM USA!