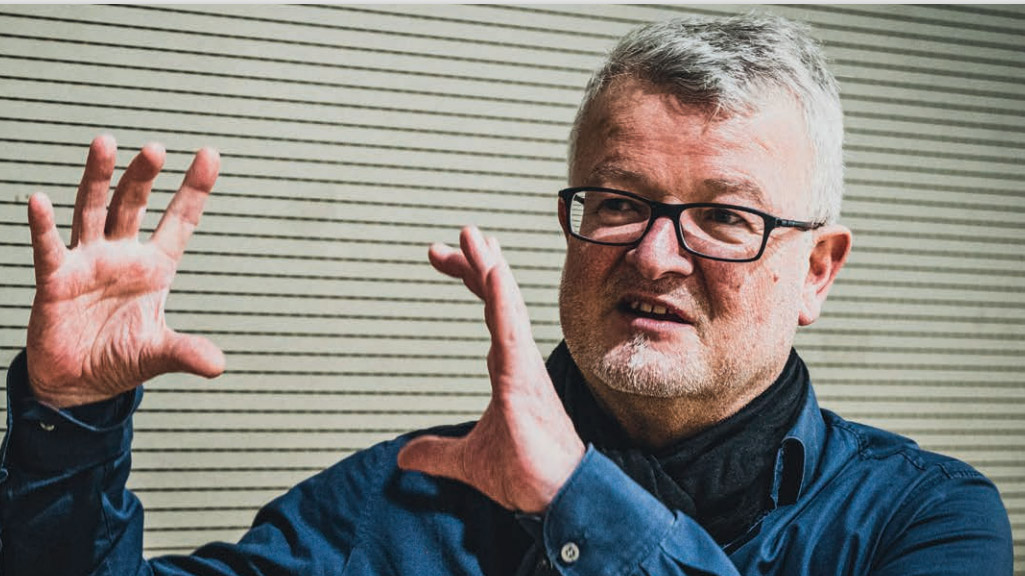
Professor Maximilian Fichtner, Executive Director & Head of Solid State Chemistry, Helmholtz Institute Ulm
Batteries are still the biggest cost factor in battery-electric vehicles. How can we reduce costs significantly to make EVs more affordable? How do we make batteries safer, and what
new materials are emerging? We asked Prof Maximilian Fichtner from the Helmholtz Institute Ulm for his insights.
Professor Fichtner, what significant advances can we expect at the battery cell level in terms of energy and power density?
A lot has happened at the cell level recently. We can construct larger cells and avoid the small-scale approach we had until now. That is because today’s manufacturing technology allows for manufacturing bigger units without defects. This results in systems with significantly less dead material – meaning packaging, housing and connections – and more room for the actual storage material. This, in turn, opens up completely new possibilities: You can either keep the same battery chemistry and get much more range. Or you can use the extra space for materials we haven’t used so far because while they are sustainable and cheap, they were too bulky. So these larger cells solve that issue. The keywords here are cell-to-pack and cell-to-chassis. Blade batteries, for instance, go in the direction of cell-to-pack. And Tesla, for example, is doing cell-to-chassis. In this case, you glue the cells together to make a solid block that becomes part of the chassis.
What materials do battery cells use in the future?
At the moment, the winner is iron phosphate. It doesn’t have massive storage capacity, but it’s cost-effective and safe, with a sustainable composition. Iron phosphate is used for cathodes, the positive electrode of the battery. In the anode, otherwise, we still have graphite. Currently, silicon-carbon composites for the anode are being developed, they will definitely come. These siliconcarbon composites have four times the storage capacity of graphite, which makes about a forty percent difference across the cell. So, simply by using a material like that for the negative terminal, we can achieve the goals we set ourselves for solid-state batteries, only using classic lithium-ion technology with a liquid electrolyte.
Some say solid-state batteries are safer than batteries with a liquid electrolyte…
With solid-state batteries, we’re actually going back to the roots of lithium technology by using the pure, metallic, lithium as an anode. That gives you a very compact lithium-metal storage. With graphite, the lithium diffuses into the rather bulky carbon host structure. That works well, as we know, but the lithium is diluted by a factor of eight. However, when using the Li metal and a liquid electrolyte, repeated charging and discharging leads to the formation of fine needles on the metallic electrode – so-called dendrites. These dendrites grow through the cell and can cause a short circuit. If you replace this liquid electrolyte, you can put a solid wall in their way so to speak. Of course, safety-wise, having no flammable electrolyte in the battery would make sense. However, solid-state batteries have had a great future for quite a while now … but they haven’t materialized yet.
How can you prevent thermal decomposition – and how much can new materials help?
Up until now, we’ve been using materials that decompose under heat – particularly cobalt oxide and materials with high nickel content. They decompose, and oxygen is released. In a high state of charge, this starts to oxidize the electrolyte. These are processes that can take place when the battery gets too hot. And the oxidation is exothermic, meaning it generates even more heat. That heat accelerates the process further still. The battery overheats, the electrolyte evaporates, you get overpressure in the housing, something cracks, the battery blows off and then the whole thing can ignite. But let’s say I use iron phosphate as the cathode material instead. That’s going to fail at some point too, but it won’t decompose exothermically and release oxygen. So there’s no self-heating process there.
Price is another crucial point. Which batteries would you choose for an affordable ‘People’s BEV?’
If I compare the different designs, right now cell-to-pack technology from the Far East can save 30-40 percent on construction and connection technology. Then you can use very affordable materials, for instance, iron phosphate. That costs less than half as much as high-nickel materials. So, with a combination of engineering design and cell chemistry, you can produce significantly cheaper batteries. In China, for example, I can buy a BYD with a range of 350-400 km under WLTC for €14,000.
In Germany, by the way, prices started from €30,000 in 2023, because that’s what the market allows. The Chinese say ‘thank you very much’ and double their margin. The next step is sodium-ion batteries for small cars. The first models are already on sale, from HiNa. And now CATL, the battery manufacturer, is supplying the first sodium-ion cells for another OEM. The small car from HiNa costs the equivalent of €9,000.
Where do Europeans, and Germans, in particular, stand on battery production? How do you rate their prospects?
Germany has stopped dragging its heels and is now almost a role model. It understands how vital it is to make batteries near where you make your cars. There is another aspect, however: battery manufacturers like CATL will soon be selling the whole skateboard, not just the battery. That’s an electric platform with four wheels and a range of 1000 km, with the charging and power electronics, electric motors, battery, etcetera all built in. So, manufacturers with no access to their own batteries will be outsourcing a significant chunk of the added value and will end up completely dependent on providers like CATL. Currently, Germany is planning for fourteen gigafactories by 2030. If they all get built, Germany could meet half of Europe’s demand for battery cells. The question then will be how far you go in terms of platform integration; it’s not just about the battery.
In a nutshell, what’s the big battery trend in the next few years?
Sustainable battery materials are the big trend. In terms of performance we’ve made considerable progress, so now these compositions – which are less powerful but more sustainable – can work very well. They can use their strengths to the full in the new battery designs, and we’ll take advantage of that. Everyone’s talking about iron phosphate. The Chinese are backing it, and, since mid of 2022, Tesla is using it in the positive electrode on more than half of its fleet. Germany will probably do the same thing. The result will be batteries that are significantly more sustainable and environmentally friendly.
Interview: Gernot Goppel