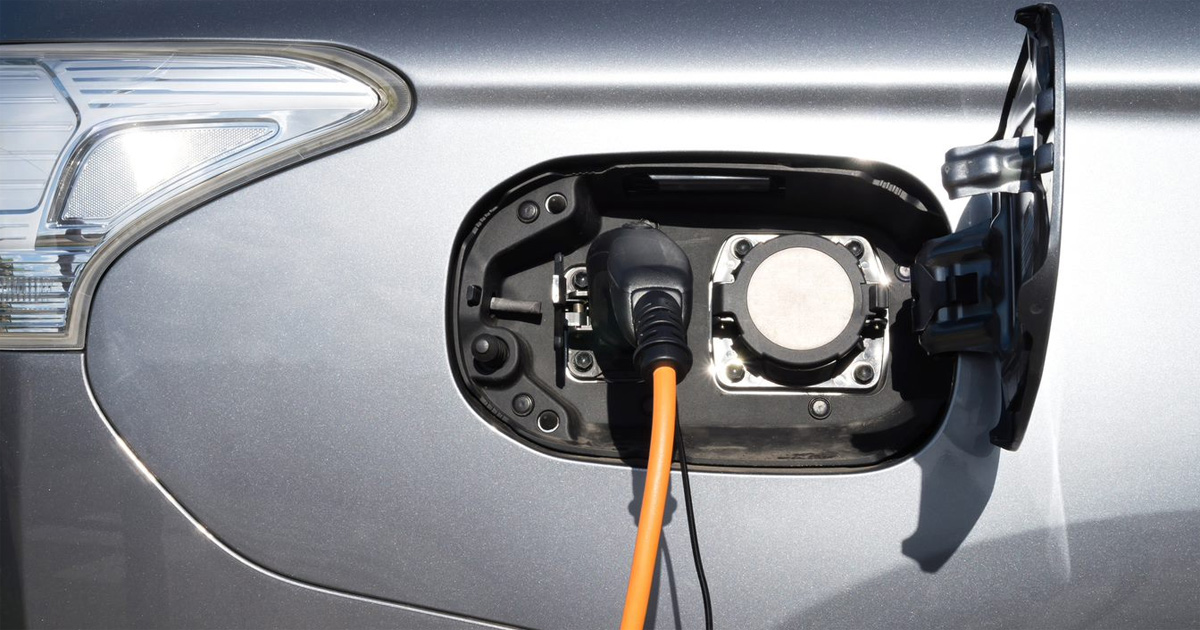
The pace of e-drive technical development has accelerated dramatically. Innovative solutions are as diverse as the applications they were designed for. In addition to efficiency and costs, OEMs are increasingly factoring sustainability and supply chains into their decisions. This applies to everything from small city cars to off-road SUVs and high-performance sports cars.
CTI Symposia accompany advanced technologies…
…from research to successful products. Once again, experts from universities, suppliers and OEMs will meet up at CTI Symposium Berlin to exchange their views on the latest trends and the next generation of e-drives. The topics they discuss in Berlin could well feature in tomorrow’s electric vehicles very soon.
Modular EDU family: six members – one mission
The task was not an easy one, as Dr Hakan Sandquist (InfiMotion Technology Europe AB, Sweden) will explain. An OEM asked his team to develop an independent EDU family with maximum application modularity – and no limits in terms of performance differentiation.
A multitude of customer requirements applied to a wide range of vehicle applications. This included hybrid, plug-in hybrid and battery electric vehicles, as well as 400V and 800V systems. The objectives were clear: to reduce complexity, costs, weight, packaging and time-to-market. Efficiency and performance, including torque and trailer load, also had to be ensured – all with a consistent focus on consumer requirements.
The mission was accomplished in close cooperation with the Geely Powertrain Research Institute. The result is an EDU family with six variants: four 400V versions (HEV, PHEV, BEV front / rear axle) and two 800V versions (BEV front / rear axle). All variants share the same oil-cooled permanent magnet electric motor unit, with stack length altered to increase power. Dr Sandquist will also cover the new, efficient oil cooling system with variable flow, the modular aluminium die-cast housing, and the differentiated inverter design (with IGBT or SiC technology). The open architecture software, developed in-house, is sure to be of particular interest.
With an EDU efficiency target of 95% (WLTC) for the 800V EDU derivative, the bar for efficiency was particularly high. The first-generation EDU family will enter production at the end of 2022; the second generation will follow as early as 2025.
Secondary e-drives for the magic ten percent
The thrust when overtaking, the off-road grip of your AWD, the torque vectoring that defuses tricky situations: secondary electric drives may only boost the main drive temporarily. But when they do, they play a crucial role.
“In practice, secondary drives are active on average for ten percent of driving times at most,” says Daniel Lindvai-Soos (Magna Powertrain, Austria). Hence, we should evaluate the properties of various e-motor types differently in secondary and primary drives. Currently, the two most important secondary drive approaches involve either asynchronous (ASM) or permanent synchronous motors (PSM) that can be switched on or off as required, via a decoupling unit. Magna has compared and evaluated both variants in a detailed study. In his talk, Daniel Lindvai-Soos will cover all relevant criteria such as reaction times, drag loss, performance characteristics, weight and packaging, as well as costs at material and system level.
Which solution is preferable depends on the overall system view and the use cases concerned. Sports cars and SUVs, for example, usually have very different requirements. After cost, peak performance is also an important criterion; continuous power is less important, as this is provided by the primary drive. Daniel Lindvai-Soos will also examine the risks and opportunities that affect the availability and cost of the raw materials used for windings, housings, magnets etc. He will close with a detailed outlook on which next-generation drive solution is preferable for specific applications from an overall system perspective.
Heading for the future – innovative 800V technology
Lukasz Roslaniec (hofer powertrain, Germany) will present no fewer than four forward-looking technology components in Berlin, all in a single product. In the first development step, innovative 800V 3-level inverter technology boosts efficiency and enables the use of gallium nitride (GaN) solutions for 800V applications too. GaN semiconductors play a key role in increasing the efficiency, range and lifecycle of electrified vehicles. The 800V GaN 3-L inverter technology can be easily combined with both high-speed asynchronous motors, and with permanent magnet synchronous motors.
The next development boost comes from hofer powertrain’s recently patented Form Litz Winding technology. This delivers a copper filling density of up to 65% for high continuous power at maximum rpm and high motor efficiency. Special insulation ensures long motor life, despite the fast switching operations of the converter. The 3-in-1 concept can be optionally supplemented with an HV boost system. This uses motor inductance to enable compatibility with 400V charging stations in a cost- and space effective way (= 4-in-1 system). The result: a future with dramatically faster charging – and no range anxiety.
The technologies have already been verified using prototypes. Lukasz Roslaniec will go into the development methodology, and will describe technical details of the overall system for a specific automotive application.
Two innovative e-motor solutions: from strategic vision to implementation
When configuring next-generation electric motors, the first aim is to meet high technical requirements at minimal cost. But for long-term business success, it’s equally important to see the bigger picture too. By opting not to use rare earths, companies can take responsibility for people and the environment while also avoiding cost and availability issues in their supply chain.
As Holger Oechslen (MAHLE International GmbH, Germany) will explain in Berlin, MAHLE has combined technical skills and strategic visions to address these challenges with innovative e-motor solutions. The speaker will begin by presenting the MAHLE Contactless Transmitter (MET). This electric motor has no permanent magnets and transmits energy inductively, without mechanical contact or wear, between stator and rotor. This core technology is being used for the first time in the automotive industry. It is maintenance-free throughout its service life, and is compatible with oil – two key prerequisites for future applications. The motor is over 95% efficient in the drive system’s most common driving conditions.
MAHLE has achieved another technological leap with the Superior Continuous Torque (SCT) e-motor, a development recently presented at IAA TRANSPORTATION in Hanover. This ‘compact endurance athlete’ can deliver an impressive 90% of maximum performance continuously. Classic application examples include driving an e-truck over mountain passes, or repeated sprints in a sports car. The key to this enormous resilience is an innovative integrated oil cooling system. Using driving cycle simulations and prototype tests, Holger Oechslen will explain in detail the influence this has on various applications.
A high power density event: CTI SYMPOSIUM Berlin
With top-notch speakers and a wealth of cutting-edge topics, this year’s CTI SYMPOSIUM in Berlin will once again be a highly informative event and an exciting forum. Top up your information tanks in the plenum and in the twelve sessions. Explore product innovations at the CTI SYMPOSIUM EXPO. And find out for yourself how longitudinal and lateral acceleration feels – at the CTI SYMPOSIUM TEST DRIVE.
Welcome to Berlin!