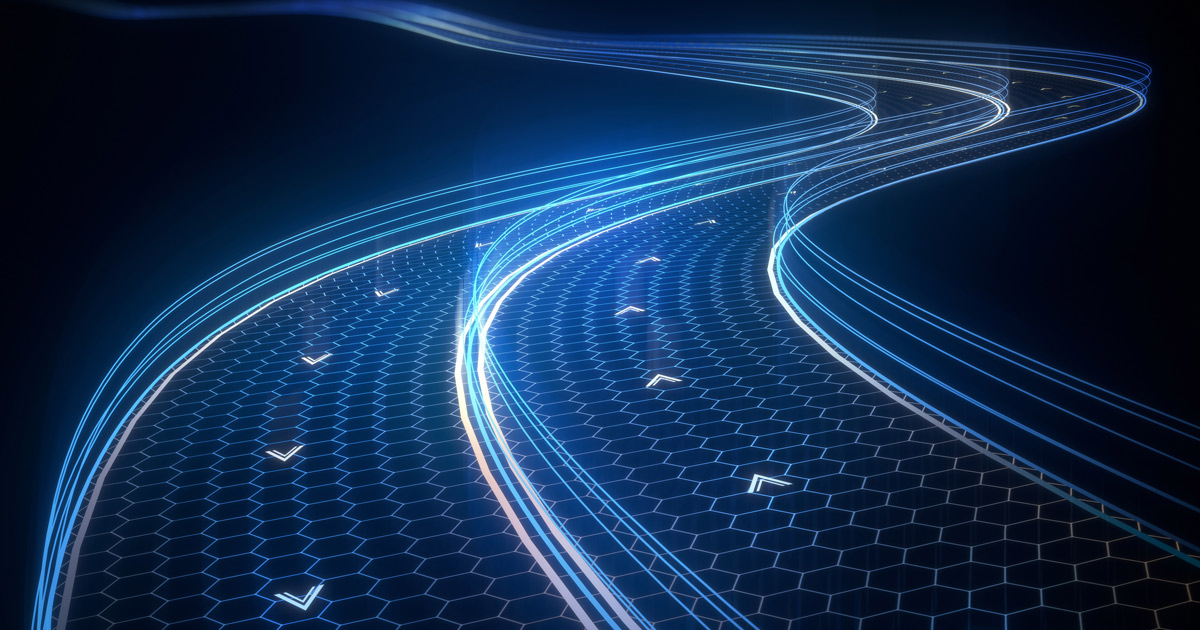
The heart of every automobile is still the power plant. Traditional values like horsepower, top speed or acceleration may be taking a back seat in EVs, but efficiency – which has a big impact on range – is growing in importance. To reduce package and weight, developers are striving for maximum power density – plus lower costs to make high-tech solutions more widespread and affordable.
Progress never stops. Yesterday’s record-breakers are tomorrow’s standard components – and a springboard to the next level. High-speed motors with 50,000 rpm … efficiency levels of 97% … what’s next?
CTI Symposium Berlin – welcome to the developer race
At CTI symposia, participants can hear all about best performances, new benchmarks and the latest attempts to raise the bar higher still. From research project to market-ready product, we present technological excellence at all stages of development. Experts from universities, suppliers and OEMs speak to a knowledgeable audience that wants to get a head start, and discover tomorrow’s champions today.
All systems go – at 50,000 rpm
Power density in BEVs (Battery Electric Vehicles) can be significantly improved by increasing the rpm of the e-motor(s) used. This permits a more compact build that delivers cost and space benefits. But where are the limits? Does the leap to ‘hyperspeeds’ of 50,000 rpm still yield economic benefits? And is the technology still manageable?
Bernd Morhard (Technical University of Munich, Germany) will illustrate how these questions were investigated in a joint research project called Speed4E. The Speed4E drivetrain uses two e-motors. They run at up to 50,000 rpm, and deliver up to 45 Nm of torque at the transmission input shafts. The standout design feature is the way the two different electric motors interact: both run independently, each with its own partial transmission.
Bernd Morhard will explain the test bench layout of the high-speed drive train, and will present exemplary test results that focus on the maximum speeds of up to 50,000 rpm. His initial figures for mechanical efficiency and drag torque are sure to be of particular interest. The speaker will pay special attention to the hydrous transmission fluid that is being considered. This fluid combines low friction with the ability to cool and lubricate the entire powertrain. The results show possible ways of improving the mechanical efficiency of BEV high-speed drives, and provide a fundamental understanding of the challenges inherent in very high rpm.
New switching cell concept: will efficient SiC technology soon go mainstream?
Si IGBT and SiC (silicon carbide) are both in the running as potential power semiconductors for inverters. For Philippe Hamon (Valeo eAutomotive, Germany), the favourite is clear: “The demand for SiC is increasing faster than expected. Not just in the premium segment, but in mainstream applications too.” Inverters based on SiC work more efficiently than those based on Si (IGBT), and offer users up to 5% more efficiency under WLTP. Although progress has its price – SiC wafers cost three times more than a Si IGBT alternative – OEMs are still switching to SiC because the lower spend on batteries (or range increase for the same price) outweighs the extra spend on the inverter.
As Philippe Hamon will explain, Valeo eAutomotive has started developing a new switching cell concept for next-generation 800V SiC inverters (SOP 2025). The new switching cell comprises the power modules (3 for the 3-phase version), the cooling box, the DC link capacitors, and the current measurement. This means Valeo eAutomotive is concentrating on the ’heart’ of the inverter, which accounts for the lion’s share of performance and costs. In fact, this assembly costs around 2/3 of the inverter’s overall price (the other significant factors are the control board and housing). The new concept ensures tremendous scalability – from 120 to 300kW – for 800V and 400V applications. With this strategy, Valeo eAutomotive is confident it can supply competitive products that will satisfy the demand for efficient SiC technology and accelerate their market penetration. All e-axle applications can benefit from this on a broad basis.
E-motor design for LCVs – systematic optimization
Light commercial vehicles (LCVs) use the same powertrains as passenger cars, albeit with some modifications. While this applies to both combustion engines and battery-electric drives, it poses special challenges for e-motor designers.
Daniele Zecchetti (Marelli Europe, Italy) will present a method developed at Marelli that enables designers to optimize electric motors systematically for use in LCV applications. The challenge involves meeting the special objectives of battery-electric LCVs in terms of driving cycles and speed, while simultaneously optimizing efficiency under specific operating conditions so range targets are met under WLTC.
Daniele Zecchetti will present the findings from vehicle simulations in relevant cycles, and will also explain both the tool chain used to develop e-motors in general, and the electromagnetic and thermal simulations in particular. Other important aspects will include the effects of the maximum converter current and gear ratio on the construction of the electric motor. In addition to WLTC range considerations, LCV powertrain efficiency on longer motorway journeys can also be very important, and must be taken into account when configuring the motor and selecting the size of the converter. The aim of the systematic optimization process is to achieve a convincing compromise between motor size, efficiency (under WLTC and on motorways), package and e-motor costs.
New wave winding – the key to high-efficiency, lightweight e-motors
The ideal electric motor achieves maximum torque and efficiency with minimum active mass (magnets, winding) and production costs. This is the postulate on which Prof. Dr. Roland Kasper (Otto von Guericke University Magdeburg, Germany) has built his development strategy. Active copper parts in the slots and air gap are maximized by adapting the shape and using a high fill factor; passive copper parts in the winding overhangs and connections are minimized by making conductor lengths as short as possible. By shortening the end windings to their physical/geometric limit, phase resistance, axial length and motor weight can all be reduced while efficiency is boosted to previously unattainable levels. This is particularly beneficial for all mobile applications that demand high energy efficiency and low weight, such as vehicle or drone drives.
The electric motor presented by Roland Kasper uses a new type of wave winding with a very high packing density. This winding significantly outperforms existing electric motors in terms of torque density and efficiency. For participants, the in-depth description of the winding design and the methods for its inexpensive, large-scale production should be of particular interest. Based on FE calculations, Roland Kasper will present exemplary design results for a) a wheel hub motor with a transmission for a cargo bike (torque 14 Nm, active mass 1.2 kg, efficiency 95%), b) a vehicle drive motor (torque 350 Nm, active mass 7.8 kg, efficiency 97%) and c) a drone motor with air gap winding (torque 3 Nm, active mass 0.2 kg, efficiency 95%). The calculation results for the cargo bike drive have been verified by test bench measurements on a prototype.
CTI SYMPOSIUM GERMANY – an arena for technological excellence
When it comes to progress in electric mobility, the CTI Symposium in Berlin presents what matter most: quantifiable results. In twelve sessions and the plenum, you can experience at first hand how developers are competing in disciplines like sustainability, efficiency, power density and scalability. You can also be there when leading technology champions present their products at the CTI EXPO – and take the latest tech for a spin at the CTI TEST DRIVE.
Welcome to CTI Symposium Berlin!