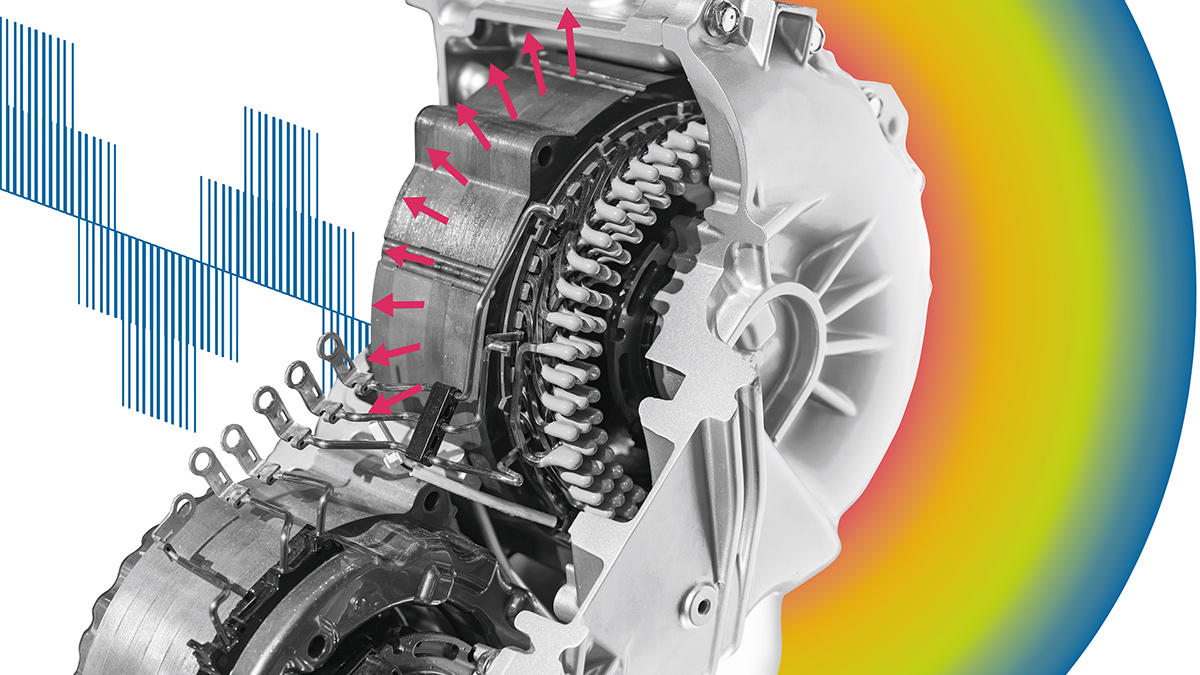
Tackling noise issues after manufacturing can be expensive and may degrade electric drive performance for efficiency, cooling, and weight. Therefore, an efficient virtual prototyping workflow of e-NVH is critical for accelerating development times, reducing prototyping, manufacturing & testing costs, and improving engineering productivity.
The prediction of acoustic noise and vibration in electric drives requires modeling and simulation of all excitation mechanisms, including mechanical forces (e.g. tire/road, gear friction forces), aerodynamic forces (e.g. windshield, fans), and electromagnetic forces. These three sources of acoustic noise must be considered together due to masking effects. For example, the unpleasant tonalities of magnetic noise produced by inverter switching harmonics might be covered up by windshield noise at high speed.
In electrical drives, magnetic excitations come from the converter and the associated traction motor. The frequencies of magnetic forces depend on slot/pole/phase combination, while their magnitude depends on magnetic circuit geometry and control. This makes electromagnetic noise, vibration, and harshness (e-NVH) a unique discipline that requires dedicated troubleshooting and mitigation tools.
Manatee software, now a part of the SIMULIA brand of Dassault Systèmes, is a specialized computer-aided engineering (CAE) software for the assessment and control of magnetic noise at all design stages of electrical machines and drives. It helps designers identify the best tradeoff between electromagnetic & NVH performance. Manatee expands the SIMULIA multiphysics simulation portfolio, which includes Abaqus, CST Studio Suite, Opera, Simpack, and Wave6. Leading vehicle and powertrain developers use these robust and proven simulation technologies for the virtual prototyping of vehicle components, subsystems, and systems, including electric drives.
e-NVH simulation requires electrical, magnetic, structural dynamics, and acoustic models. The traditional method for evaluating e-NVH has been for a CAE expert to use general-purpose FEA software and manually combine all the physics. This process requires setting-up each solver and their interfaces, such as mesh-to-mesh projections, time vs. frequency domain and discretization. It also requires scripting to call this customized model combination at variable speed and to obtain relevant output quantities such as A-weighting for human ear sensitivity. This complex workflow, which is generally maintained and run by a single CAE expert, results in a bottleneck in the numerical simulation process, preventing the use of NVH metrics in design iterations.
To overcome this issue, Manatee provides a unique algorithm to accelerate variable speed e-NVH calculations without loss of accuracy. It contains its own multiphysics models with predefined couplings, but can also be easily interfaced with other CAE software.
In addition, Manatee comes with predefined workflows adapted to each engineering role. The multiphysics simulation can be set up with the click of a button thanks to standardized interfaces that enable collaboration between electromagnetic and mechanical departments. Electrical engineers can set up the electrical machine and run electromagnetic calculations at variable operating points; the result is a Magnetic Look-
Up Table (MLUT). In parallel, mechanical engineers can import the electric powertrain modal basis. The MLUT can be provided to NVH engineers and the modal basis to electrical engineers. This way, noise mitigation techniques based on electromagnetic and mechanical design can be investigated in parallel. NVH engineers can track if NVH targets are fulfilled at all stages of new product development.
An efficient collaboration of control, electrical, mechanical & NVH engineers also requires a user-friendly interface, where all physical quantities can be easily visualized and post-processed. Manatee comes with insightful plots to help quickly identify which magnetic force excites which structural mode. New specialized e-NVH solutions are regularly developed, supporting all engineers finding solutions to reduce noise & vibration levels (skewing, notching, Harmonic Current Injection, etc).
Manatee also provides parameter sweeps, global optimization with predefined e-NVH metrics and design exploration tools to find the best tradeoffs between electromagnetic & NVH performances.
The robust and user-friendly features of Manatee provide a unique, collaborative CAE environment specialized in the assessment and control of electromagnetic noise & vibrations. By using Manatee during the design stages, designers and engineers can significantly accelerate the virtual prototyping of electric drives, resulting in shorter development cycles, reduced prototyping costs, and better NVH risk management.
For more information visit: https://www.3ds.com/products/simulia/manatee