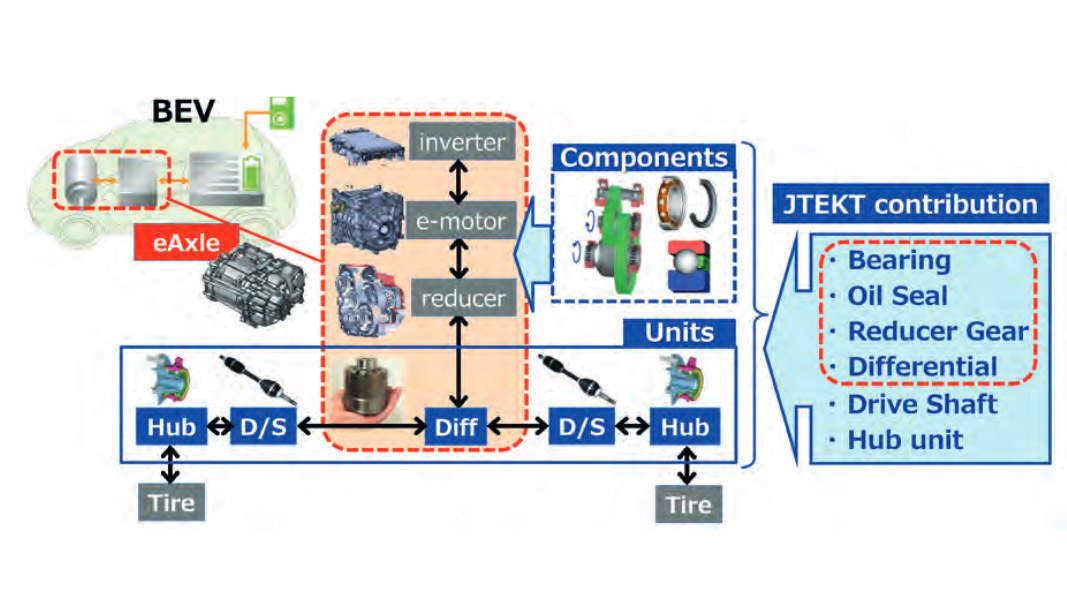
Makoto NISHIJI, Chief Engineer Driveline CE Dep’t, Automotive Business Unit, JTEKT Corporation
JTEKT contribution for e-Drive system
The automotive industry is developing technologies to respond to the once-in-a-century transformation for realizing a carbon-neutral, recycling-oriented, safe and comfortable society. As the powertrains of automobiles become electrified, the requirements for the e-motor based driveline systems and units that handle the vehicle movement are changing significantly. To take this evolution to an even higher level, reliability and cost reduction are essential, but it is also important to address improvements such as better power consumption (loss reduction, weight reduction, efficient regenerative braking), mountability (size reduction), low NV, and added values (4WD function, Torque control devices, etc.). To achieve this, JTEKT is conducting technological development for e-Drive system by several units/components aiming for “No.1 & Only One” in each field. (Fig. 1)
eAxle improvement by JTEKT Ultra Compact products
Following to the strong demand for higher power density eAxle in future, JTEKT has developed “Ultra Compact” product series, covering Differential (JUCD), Ball Bearing (JUCB) and Conductive Ball Bearing (JUEB), Oil Seal (JUCS) for eAxle size and weight reduction.
Figure 2: Co-Axial eAxle with JTEKT Ultra Compact products
Fig. 2 shows application example for 150kW class Co-Axial stepped pinion reducer eAxle. Co-Axial eAxle has advantage for packaging in height and front-rear axial length, therefore higher power density compared with traditional 3-Axis parallel offset reducer eAxle, but the eAxle width remains wide because of side-by-side e-motor, reducer, and differential layout. By introducing JTEKT Ultra Compact products, we estimate -70mm width and -7kg weight reduction from typical Co-Axial eAxle arrangement, therefore we can contribute eAxle power density improvement furthermore.
JUCB® Features and Advantages: Compact and High-speed performance
The most important requirement for bearings due to the shift to BEVs is higher rotational speed. In some cases, the maximum rotational speed ratio between the conventional power source, the engine, and the motor can exceed more than three times. The problem is the deformation of the cage due to centrifugal force. With a typical resin cage, when the limit speed is exceeded, the cage pockets deform due to centrifugal force, causing interference with the rolling elements, and the increased rotational resistance causes abnormal heat generation, leading to seizure.
JTEKT has developed a combination cage concept that can minimize deformation. Two resin parts of the same shape are combined to create a structure that suppresses deformation of each other, ensuring cage strength. Furthermore, in order to downsize, JTEKT have developed a bearing, JUCB® (JTEKT Ultra Compact Bearing®), which reduces the bearing width to almost the ball diameter size by minimizing the cage width (Fig. 3).
Figure 3: JUCB® (JTEKT Ultra Compact Baring®)
By optimizing the cage mold and that conditions, JTEKT achieved high-speed rotation of over 2 million dm-n (bearing high-speed performance index: multiplication of ball pitch diameter (dm) and rotational speed) under oil lubrication.
UEB® Features and Advantages: Compact and Conductivity
In bearings used in motors (especially driven by inverters), a potential difference may act between the inner and outer rings of the bearing due to magnetic flux imbalance inside the motor. Sparks (electrolytic corrosion) are generated at the contact between the rolling elements and the raceway due to this potential difference, which is known to cause washboard-like damage to the raceway. Conventional technology has taken measures to insulate bearings, such as using ceramic balls as insulators and forming an insulating coating on the outer ring surface. In addition, measures have been put into practical use to bypass the potential between the tracks other than the bearings using a separate circuit parallel to the track. JTEKT has developed JUEB® (JTEKT Ultra Earth Bearing®), which uses a conductive material in the seal to bypass the current path to the seal and avoid electrolytic corrosion on the bearing raceway. JUEB will provide a compact bearing with a conductive mechanism, contributing to improving the reliability of eAxle. (Fig. 4).
JUCS® Features and Advantages: Compact and Sealability
The oil seal installed at the connection between the differential and the drive shaft must be able to prevent oil leakage from the inside and contamination from the outside. If the seal width is shortened to make the seal smaller, the lip length will also become shorter, and if the conventional design is used, the ability to follow eccentricity to the shaft will decrease. In addition, the rubber will become hard at low temperatures, worsening the ability to follow the eccentricity. As a result, there was a problem that oil leaks were more likely to occur.
We have developed an acrylic rubber material with improved low-temperature properties and have improved its ability to follow eccentricity at low temperatures by optimizing the tension force composition ratio (rubber, spring). The acrylic rubber also has improved elasticity and can maintain the same oil retention capacity as conventional products. As a result, the JUCS® (JTEKT Ultra Compact Sael®) makes it possible to shorten the seal in the axial direction, contributing to the miniaturization of e-axles. (Fig. 5).
JUCD® Features and Advantages: High torque density and safety performance
Compared to typical bevel gear type open differential, JUCD® (JTEKT Ultra Compact Diff®) has an increased gear mesh quantity and wider gear mesh width at larger gear mesh diameter between planet gear (PG) and side gear (SG). This is possible by using small diameter parallel axis planet gears which are directly supported by the housing bore similar with journal bearing structure. As a result, JUCD has higher torque density (= strength/volume) than typical open diff. Required differential gearing functional volume for JUCD will be less than half compared with open diff. for the same strength. (Fig. 6)
Figure 6: JUCD® (JTEKT Ultra Compact Diff.®
PG outer diameter – HSG bore direct contact structure generate torque sensing limited slip diff effect, which brings vehicle performance improvement advantages for safe and confident drive under daily various driving situations. This LSD function works not only drive mode, but also coast mode or even regenerating braking mode, therefore it will bring potentially better power consumption for BEV in real world by minimizing wheel slip/spin situation and friction brake activation.
Planetary Carrier integrated JUCD
In case of Co-Axial stepped pinion reducer, planetary carrier and differential housing will have same rotational speed, therefore it is possible to integrate those two functions into one housing, but typical open diff. bevel gear will be located at the side of planetary carrier in to avoid radial dimensional interferences and maintain assembly possibility of the differential components into one-piece housing thru its window. (Fig. 2)
JUCD can reduce differential radial and axial dimension significantly keeping the same required strength. By using this advantage, it is possible to locate the differential well inside of the planetary reduction gearing for reducer width improvement by full axial overlap.
On top of JUCD, JUCB and JUCS could be also integrated into the reducer for further width/weight improvement not only for reducer, but also for eAxle, and even vehicle level. (Fig. 7)
Figure 7: Planetary carrier integrated JUCD in eAxle reducer
Cylindrical JUCD housing together with the same number of differential PG set and reducer stepped pinion gear set reduce planetary carrier stress variation at each stepped pinion support during torque transfer situation. This is also interesting advantage to minimize tooth contact variation of the stepped pinion set, so that it will be easier to define common and optimum tooth micro geometry for the reducer gearing for low NV, and better durability.