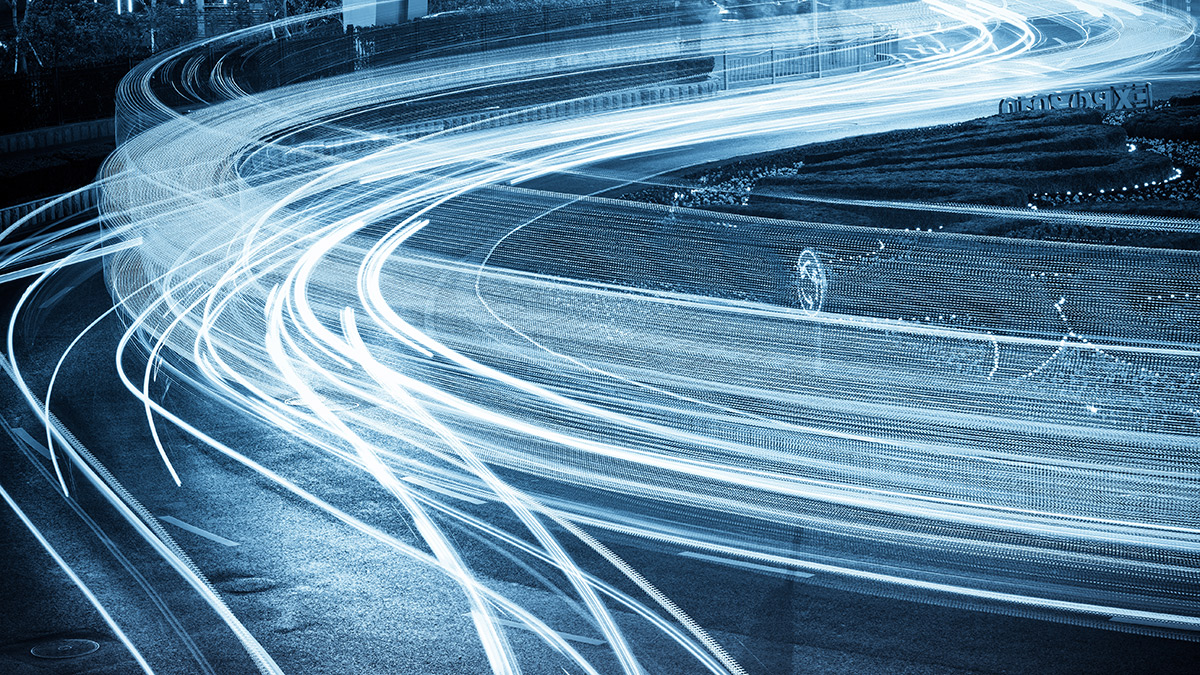
Progress never stops. With electric drive technology evolving rapidly, developers can now meet customer requirements even more precisely and comprehensively, while higher efficiency also increases the performance and range of battery-electric drives. So what’s next? One thing’s for certain: With customers seeking more independence and flexibility, plug-in hybrid drives are staging a comeback.
CTI Symposium USA – covering all the angles with the customer in mind
In twelve Deep Dive sessions, specialist lectures will cover the latest electric drive systems and their key components. In the plenum, prominent representatives from OEMs, suppliers and universities will discuss their strategies and technologies for tomorrow’s CO2-neutral mobility. The goal: Advanced automobiles that, ultimately, only need to convince one person – the driver.
Raising many bars. And clearing them all.
“With our next generation eDrives, Magna aimed to set new standards in KPIs such as efficiency, power-to-weight, torque-to-weight, power-to-price and torque density,” says Daniel Lindvai-Soos (Magna Powertrain, Austria). Further goals included a drop-in solution on the hardware and software level, higher product and production sustainability, and improved system integration. As the key figures he presents will show, the company has certainly succeeded.
Magna’s NextGen drive is significantly lighter and smaller than the current version. The 29% reduction in the Z-dimension is particularly important, since it enables horizontal and vertical integration into the rear and front vehicle space. The new drive offers 94% efficiency in WLTC, and 93% including real-world highway driving. This improves efficiency over a wide speed range, and expands application flexibility. The new eDrive uses significantly less aluminum and rare earth material, and the CO2eq for production has been cut by around 25%. Among the new technologies making their debut in the NextGen drive are the HV Embedding SiC Power Modules. These reduce electrical losses and improve efficiency. Daniel Lindvai-Soos will also be giving an overview of software-oriented advantages such as OPP (optimized pulse patterns), the thermal operating strategy, active peak load damping, state-of-health monitoring, and other end-user functions. A digital twin is part of the new Magna NextGen drive. It simplifies integration into the operational strategy, and supports the ‘drop-in solution’ approach.
“What could we do better?” How Toyota learns from its competitors.
Space is a valuable commodity in battery electric vehicles (BEVs), and customers want vehicles whose drivetrain components all combine high performance with efficient use of space. The study presented by Jaret Villarreal (Toyota, USA) will focus on the power density potential of compact, single-axle powertrain systems. The study began by reverse-engineering a competitor’s geartrain. Using this model, an in-house optimization workflow then explored the feasibility of reducing its size further, without compromising on standards.
Jaret Villarreal will provide insights into the workflow and software used, and will discuss the results of the optimization. The study clearly demonstrates the possibility of considering optimization at earlier development stages for BEV transaxles, and also highlights the need for continuous improvement. Using the latest technological advances, Toyota engineers can now pursue multiple competing goals simultaneously, all in specific workflows. These include efficiency, NVH, durability, size and cost. As a result, they can create designs that offer customers the best possible driving experience.
Control losses with high-speed motors? Not with Surface Acoustic Wave (SAW) sensors.
There is a growing trend towards high-speed, high pole count motors. But to maintain controllability, they require higher switching frequencies from the power electronics. As David Hind (Drive System Design, UK) and Ryan Maughan (Transense Technologies, UK) will explain, current solutions can quickly reach their limits here. Field Oriented Control (FOC) has a high computational burden, while Direct Torque Control (DTC) suffers from the poor accuracy of the torque estimators used.
David Hind and Ryan Maughan will be presenting a new method that uses SAW (Surface Acoustic Wave) sensor technology to overcome these shortcomings. By embedding SAW sensors, developers can obtain robust, precise, high-speed readings of torque and shaft temperature in real time. SAW sensor technology has already proven itself in motorsport and aviation, and is suitable for use in production motor drive systems. “Transense Technologies has been working with Drive System Design (DSD) to explore the potential of integrating torque sensors into the control loop of electric motors,” say Ryan Maughan and David Hind. “Using DSD’s extensive simulation capabilities, new control algorithms can be implemented and assessed.” The speakers will discuss the findings of this work, and will demonstrate an improved method of motor control using SAW torque measurement feedback. Specifically, they will quantify the reduction in computational overhead compared to FOC. This can indicate what increase in inverter switching frequency – and hence potentially motor fundamental frequency – can be achieved from a motor control perspective.
Torque management systems – the masters of traction and driving dynamics
For maximum driving pleasure and safety, ample torque alone is not enough. You also need to distribute that torque optimally between the wheels and axles and convert it into traction, always in line with specific driving scenarios. Modern electric drives can use various torque management systems (TMS) to achieve this aim. But which works best in which specific case?
This is the question that Josefin Frisk (BorgWarner, Sweden) will be addressing in her lecture. As EV models become more diverse, the range of drive architectures for different segments and performance levels is expanding too. In the past, several TMS implementations have been proposed – one electrical machine per wheel, for example, or an additional electrical machine to supply differential torque, carefully actuated friction clutches to replace the differential, or an electrically controlled limited-slip differential. All these TMS architectures provide additional degrees of freedom for the vehicle controls. They also affect energy consumption and performance in different ways, change how the vehicle feels for the driver, and how it performs under challenging driving conditions. In addition, they offer potential for differentiation, and significantly improve safety. As you might expect, each architecture involves an inherent trade-off. In her presentation, Josefin Frisk will quantify and explain the differences between various TMS options for BEV architectures in terms of energy consumption, vehicle performance, packaging and cost. And in the process, she will answer the question we asked at the beginning.
A surprising comeback: What’s next for hybrid drives?
There’s no missing the resurgent interest in hybrid drives, as a glance at our agenda at CTI Symposium USA will confirm. With high-ranking representatives from leading OEMs, the panel discussion on this topic promises to yield interesting insights. In the plenary session, hybrid pioneer Toyota will be sharing details of its development work on the new hybrid system for the Camry. And last but not least, hybrid drives will feature in individual contributions to the Deep Dive sessions.
Advanced hybrid systems – the best of both worlds
There are good reasons to favor hybrid drives as a bridging technology. As Aditya Dattawadkar (Schaeffler Group, USA) will point out, most US customers want an electric vehicle that won’t make them alter their lifestyle too much. They are used to driving big vehicles for hours on end with just short breaks before they resume their journey. By offering the flexibility customers seek in terms of range and energy sources, hybrids tick all these boxes and deliver the best of both worlds: ICE and BEV.
Business-wise, hybrid vehicles are the ideal way to keep using existing technologies while simultaneously promoting the switch to pure-electric drives. Some engines and transmissions are the result of decades of development work, and are highly efficient, cost-effective and reliable. As Aditya Dattawadkar will explain, Schaeffler is working hard on hybrid systems that can be flexibly adapted to customer needs. The company benefits from the knowledge gained from ICE drivetrains, and also from advances in electric motor development. Schaeffler has several ideas in production, and more at advanced stages of development. In his lecture, Aditya Dattawadkar will showcase some of the latest hybrid vehicle technologies, then address the growing demand for hybrid systems and show ways in which it can be met. His application fields will range from passenger cars to pickup trucks and light commercial vehicles.
Integration in perfection – a pioneering approach for a PHEV P3 pickup truck
What’s the best way to integrate a high-performance P3 hybrid system in a 4WD light truck? The research paper presented by Larry Pritchard (BorgWarner, USA) gives a surprising answer: “Put it in the transfer case!”
This innovative integration approach eliminates the need for conventional planetary transfer case range sets, and significantly simplifies packaging. The primary goal of the research study was to enhance the electrical proficiency of these hybrid systems, and specifically to extend their electric-only range. The aims are to reduce reliance on combustion engines, and to achieve higher levels of electrification. The optimized sizing of electric drive train components, including 400 and 800 volt systems, plays an important role.
Larry Pritchard will present key advantages and interesting technical highlights of the P3 hybrid drive system. These include on-demand front axle braking energy recoupment, which the integration of the P3 system into an active transfer case makes possible; using the hybrid drive as a power generator and energy source at remote worksites, and the fact that a PHEV P3 pickup truck can meet ambitious emissions targets. The research will help developers to build efficient, versatile light trucks that satisfy users to the full in terms of driving performance, independence and sustainability.
CTI Symposium USA – three days that make a difference
Discover an informative and inspiring program on May 15th and 16th! Follow the specialist lectures in twelve Deep Dive sessions. Play an active role in the plenary discussions, and explore the latest developments at CTI SYMPOSIUM EXPO. Enjoy a test drive with CTI RIDE & DRIVE – and grow your business network at our CTI NETWORKING NIGHT.
Welcome to CTI Symposium USA!