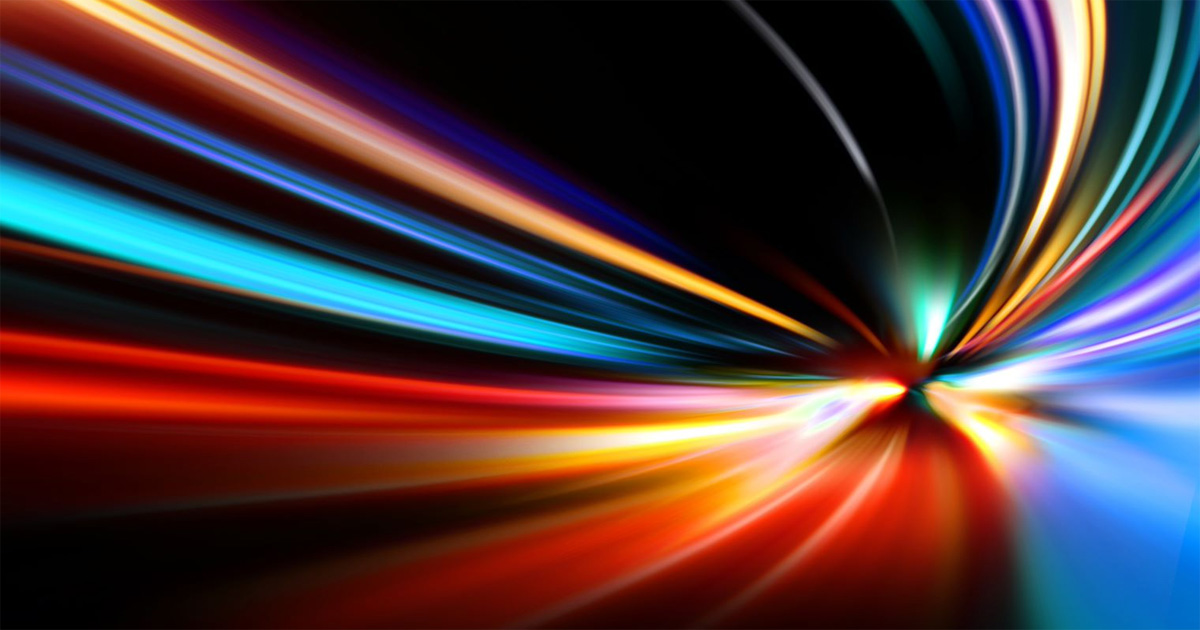
Tomorrow’s automotive mobility will be sustainable and carbon neutral. While that would be impossible for internal combustion engines, for battery-electric drives the goal is in sight. From the considerable heights already scaled, developers are aiming higher still by improving the operation and production of electric motors. Innovative technologies are boosting efficiency and range while lowering costs; valuable raw materials are being used more sparingly; and CO2 balances are improving, even during production.
Highly efficient – just like the CTI Symposium USA
At the CTI Symposium USA, experts and decision-makers from leading OEMs and suppliers will present their strategies and technologies for tomorrow’s carbon neutral mobility. Come and get the latest information live at first hand – and contribute to the discussion yourself. Explore the latest electric drive systems and their key components in twelve Deep Dive sessions. Discover the developments and field results that matter for you. On two days, in a single location, all this and more awaits you.
A comprehensive range of electric motors (PM, ASM, SSM, HPM), plus a star
Switching to electric drives is an urgent necessity. At the same time, the process is also paying off for companies and releasing synergies. “By continuously focusing on electric motor development, we have found further improvements in reducing our CO2 footprint during production, all while improving efficiency,” says Jonathan Getz (Schaeffler, USA).
Schaeffler’s broad range of modular electric motors offers ideal solutions for the diverse challenges posed by the world’s growing variety of electric drive vehicles. From traditional PSM motors to advanced magnet-free motors with powered rotor coils, sustainability is always baked in. Schaeffler uses special tools for eMotor optimization that take torque, power, efficiency, strength and NVH into account, all while balancing the financial and environmental costs of the motor.
As a special example of this development work, Jonathan Getz will highlight the Separately-Excited Synchronous Motor (SSM). Here, replacing the permanent magnets with rotor windings has substantially reduced both the CO2 footprint during production, and the dependency on rare earth materials. Special optimizations to the cooling system, plus the use of brushless, inductive transmitters, further boost the motor’s efficiency.
Schaeffler’s advanced PSM, ASM, SSM and HPM (Hybrid Permanent Magnet) motors for different applications offer solutions that are efficient and sustainable, yet also cost effective. The electric motor designs can be applied to build to print, build to motor, and even build to system specifications.
WLTC is too imprecise – more highway, more range for LCV
Light commercial vehicles (LCV) in particular are virtually made for battery-electric drives, says Daniele Zecchetti (Marelli Europe, Italy) in his introduction. As delivery vehicles, their local emission-free operation guarantees them access to current and future urban clean air zones. The electric drive ensures low downtime and service costs, and range is rarely an issue because vehicles can charge at the depot overnight.
Essentially, this performance profile is what defines LCV electric drive specifications, whereby both LCVs and passenger cars use WLTC to certify emissions and fuel consumption, or to measure their electric range. But today, that strong focus on urban deliveries is no longer enough for battery-electric LCVs. Good efficiency and range in extra-urban and typical highway conditions, with maximum payload, have also begun to influence electric powertrain specifications and design.
Marelli has developed a method for systematically developing and optimizing electric motor design according to defined requirements. Daniele Zecchetti will explain the tool chain used, and will present the results of vehicle simulations in relevant cycles. The goal was to find the best compromise between range, maximum total weight and costs for LCV electric drives, in line with the new framework parameters.
Convincing technology, low cost – a wheel hub drive that forces you to think again
“Today’s electric vehicles still suffer from low efficiency and insufficient range, especially in cold weather and when driving on the freeway,” says Dr. Alexander Rosen, co-founder of the German start-up DeepDrive. In WLTP and EPA, the average plug-to-wheel efficiency of modern electric vehicles is below 60%. Now DeepDrive has developed a new motor architecture for in-wheel motors that focuses on high efficiency, especially in everyday driving situations.
The motor topology is based on a highly innovative radial flux approach with novel winding technology. The no-transmission motor presented by the speaker offers high specific torque densities of up to 60 Nm/kg. The special design of the stator reduces iron losses and enables very high efficiency levels, especially in the partial load range. Dr. Rosen will discuss in depth the critical issue of unsprung masses; the solution includes the innovative integration of a lightweight brake system.
Until now, the main obstacle for wheel hub drives has been their cost. Dr. Rosen will counter this by showing how the DeepDrive wheel hub drive combines sparing use of materials (e.g. for the magnetic mass and sheet metal packages) with simple, cost-effective manufacturing processes (e.g. for the windings).
His case study for a mid-size vehicle will show how these wheel hub drives can reduce EV purchase and operating costs by up to €5,000 while also increasing range by 20% with the same battery capacity. The drives are suitable for all EV types, from compact cars to premium SUVs and even sports cars.
The heart of the electric motor – innovative solutions for rotor and stator windings
To a large extent, coil windings are what determine the efficiency and cost-effectiveness of electric traction motors. So in addition to the established stator manufacturing processes (hairpin and insertion technology) and wound rotors (flyer and needle windings), there is still a demand for innovations – especially with the shift toward higher voltages in e-traction drives.
Summing up his company’s strategy, Kumar Rajasekhara (Marsilli, USA) has this to say: “We have developed solutions that get the best out of traditional technologies by combining their advantages, and reducing their drawbacks.”
The speaker will begin his presentation with an update on the latest developments in Marsilli’s Distributed High Density (DHD) stator winding technology. This patented winding solution is specifically used to reduce high-frequency losses and ensure high flexibility in e-motor design and the winding scheme, and also boasts a high fill factor. Last year, the winding technology was introduced to the North American market with a comparative analysis based on 400V, 3,500 RPM DHD-wound motors. This year, Marsilli will present study results in which DHD-wound prototypes also performed well at higher voltage (800V) and higher (18,000) RPM.
As his second focus point, Kumar Rajasekhara will cover new rotor winding technologies for Externally Excited Synchronous Motors (EESM). Marsilli has developed two new solutions for high performing rotors that achieve the winding scheme stability and geometric winding scheme accuracy demanded by high-voltage drives. The speaker will present and analyze the features, functionality, differences and use cases of both solutions in detail.
Production lines for hairpin stators – processes, modules and surprising insights into copper wires
Since EV drive motors need stators in large quantities – and will continue to do so in future –, flexible and highly efficient production lines are required in order to meet market demand. Matthias Weber (Felsomat, Germany) will describe the latest developments in hairpin stator manufacturing. When designing customer-specific configurations, the entire process chain, modular processing machines and buffer loops are all examined.
The most critical part of the hairpin stator is the CU wire used. The composition and material specifications needed for this wire go beyond the specifications that are commonly listed. This leaves automotive OEMs and stator line manufacturers in the dark, a situation Felsomat was not prepared to accept. “We have carried out many trials, laboratory and specification tests, leading to endless application adjustments,” says Matthias Weber. The speaker will share these insights with his audience. The knowledge obtained through researching material properties and tolerances plays a key role in enabling production lines to run at optimal speeds and tolerances, and contributes directly to optimal stator quality.
Turn off your screen – and come to CTI Symposium USA
Get out of the office for two days and visit the CTI Symposium USA! Follow the discussions live in the plenum, then catch up on the latest news from your specialist field in the sessions. During the breaks, check out important innovations by taking a tour of CTI Expo. Series and demo vehicles await you at our CTI Ride & Drive parcours, where you can experience real-world progress in electric propulsion for yourself, either behind the wheel or as a passenger. As for networking, the CTI Networking Night @Meadow Brook Hall is the place to be. Get talking with colleagues, speakers, exhibitors and sponsors over delicious food and drinks – and make valuable new business contacts in a relaxed atmosphere!
Welcome to the CTI Symposium USA.
Visit the CTI SYMPOSIUM USA