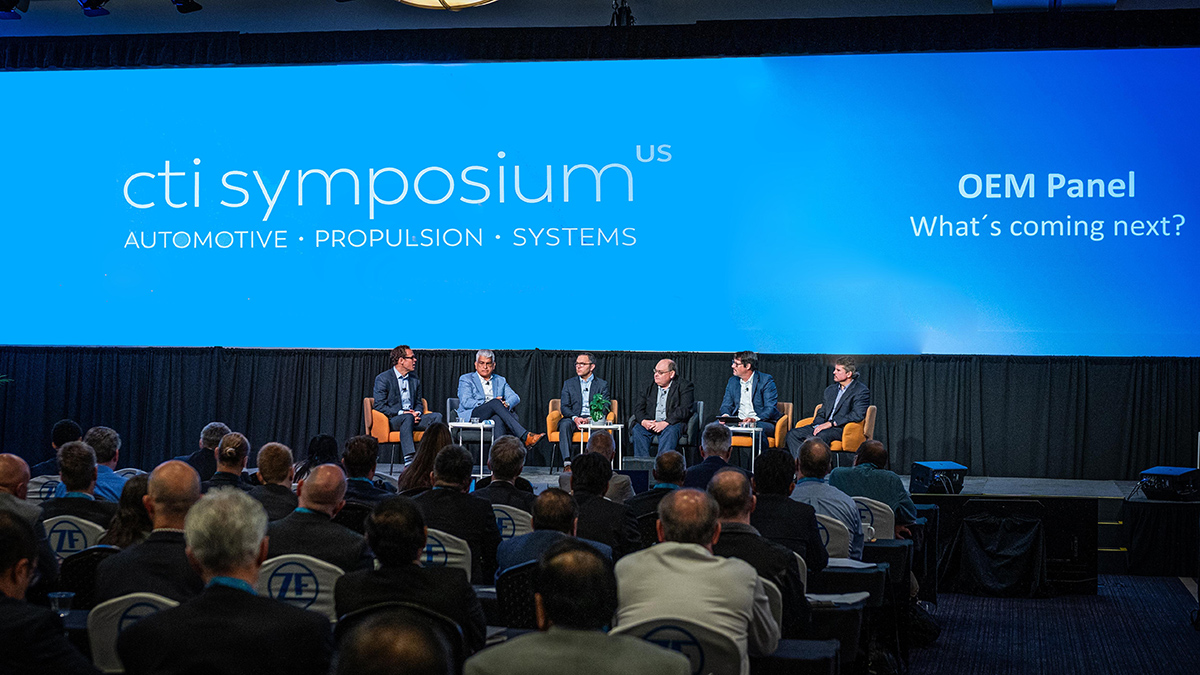
How is the electrification of light vehicles and trucks progressing? As the US CTI Symposium Novi 2024 showed, hybrid drives may be involved for longer than developers expected. Meanwhile, OEMs and suppliers are working tirelessly to make all kinds of electrified drives more efficient – and more sustainable.
The development came as something of a surprise. Just a year or so ago, the broad consensus in the industry was that there is no alternative to purely battery-electric cars (BEVs). Now, many OEMs are moving hybrid drives higher up the agenda again. At the CTI Symposium USA (Novi, MI, May 15-16, 2024), Chair Patrick Lindemann addressed this development right at the start of his introductory speech, saying BEVs were not catching on as quickly as expected, and in some cases registration numbers were falling. For the US market, Lindemann thinks advanced hybrid drives could still play a significant role up until 2040. Hence, hybrids featured more strongly again in this year’s conference program – both in the specialist lectures and in the discussions.
Obviously, that doesn’t mean the overall development strategy is being upended. As always, all sensible drive electrification solutions will continue to be discussed at Novi. This year, examples included: What are the trends in future electric motors, and what role will hydrogen play? To what extent can heavy trucks be electrified? How will battery technology develop further? And how is growing electrification changing vehicle production?
We’ll need hybrids a little longer
But let’s begin with the new trends in hybrid drives. These also featured in the OEM panel discussion with Mike Anderson, GM, Micky Bly, Stellantis, Greg Gardner, Ford, Jonathon Ratliff, Nissan, and Brian Schneidewind, Toyota. All the participants bar one agreed that in 2035, the BEV market share would probably not exceed 50%. The exception was Mike Anderson, who stood by GM’s strategy of being 100% electric by 2035, at least for light vehicles, but added: “We’ll adapt to developments until then where necessary”. Generally speaking, Ford foresees a very ‘blended’ market, with the move to full electrification progressing faster in cars than in SUVs and trucks. Nissan takes a similar view and is sticking with hybrid drives, especially for larger vehicles. Toyota is backing a ‘multiway path platform’, while Stellantis still plans to be fully electric by 2040.
In this context, the new RAM Charger was mentioned in the discussion, which “breaks all the rules” according to RAM. The truck has a purely serial drive, with a Pentastar V6 petrol engine that powers a 130 kW generator. The two electric drive motors produce 250 and 238 kW respectively. Stellantis claims an electric range of 145 miles, and a total range of 690 miles. According to Micky Bly, the group is taking a three-pronged approach: range extender drives, purely electric, but also 48V hybrids.
As for future hybrid architectures, the panel agreed that there would be different approaches, or “the right tool for the job,” as Mike Anderson put it. Greg Gardner thinks multi-speed transmissions for hybrid drives will still be available “for a good while yet.” Micky Bly does not see any convergence in hybrid architectures yet, saying Stellantis was also counting on suppliers to contribute flexible solutions. Toyota is focusing on powersplit for passenger cars, and also more on plug-in hybrids, where only the battery – not the drive itself – is scaled. In general, Toyota is focusing on platforms that work for both BEVs and xHEVs.
There were several specialist lectures on hybrid drives in the Deep Dive sessions. Aditya Dattawadkar, Schaeffler, described recent advances in hybrid architectures in his talk “Hybrids are Making a Comeback”. Sarah Zitouni, Aurobay, asked: “ICE is dead? – The Need for ICE through Hybrid”. Aurobay is a Volvo-Geely joint venture. It became part of Horse Powertrain, a global Geely-Renault joint venture, at the end of May 2024. Its business field covers dedicated combustion engines, hybrid transmissions and batteries. For several years, Geely has been backing series-parallel hybrid drives and combustion engines with a high efficiency of well over 40%.
Brian Schneidewind, Vice President of Powertrain Design, gave a plenary lecture called “A global development approach to Toyota’s 5th generation hybrid system for Camry”. He explained that while the Camry was essentially the same vehicle in all global markets, Toyota implemented detail solutions differently, taking local supplier structures and their respective capabilities into account. For example, oil pumps were constructed differently in Japan and North America, yet their function was the same. During development, different regions could take the lead: Ann Arbor, Brussels, Shanghai or Toyota City. The basic principle was this: “When a region had a particular technology lead, they took the global development responsibility”.
E-drives to become more efficient and sustainable
However the future looks for hybrid drives – they are part of an electrification process that is progressing overall, and comprises many facets. Of course, all-electric drives were still a dominant topic on the symposium. They were also discussed in the OEM panel mentioned above, including the enduring question of how many gears an electric drive needs. For Brian Schneidewind, Toyota, one is usually enough, with two driven axles plus disconnect as an alternative to two gears. Micky Bly, Jonathon Ratliff, Greg Gardner and Mike Anderson (Stellantis, Nissan, Ford and GM) took the same view.
Another interesting question was whether OEMs prefer to make electric motors in-house, or outsource their production to suppliers. GM wants to manufacture some PMSMs and ASMs in-house, but also involve suppliers. Ford wants to make mass-production motors in-house, but also retain a “good mix” of suppliers. Ratliff said Nissan were also looking at externally excited e-motor designs (like WRSMs and EESMs) being developed by several makers. Toyota prefers PMSMs for in-house production, but is likewise also looking at external alternatives. So the general view was that PMSMs would continue to improve significantly, but that developers were seeking to minimize the use of heavy rare earths (HRE) in magnets – or even do away with magnets entirely.
The impressive progress of electrification technology was also reflected in the high number of Deep Dive sessions on electric drive units, electric motors, batteries, thermal management, development tools, power electronics, electric components and electric motor development tools. On electric drives and electric motors alone, there were over 25 specialist presentations. As usual, these and other presentations are available as downloads for symposium participants.
New opportunities for suppliers
In the Supplier panel discussion on Day Two – “How to deal with the supply chain, sustainability and accessibility requirements and challenges” – supplier representatives shared their views. The participants were Zobeida Gutierrez, Valeo, Dhanashree (Dhana) Kad, ZF, Keiwan Kashi, GKN, and Chandra Krishnamurthy, BorgWarner. Again, there were some fascinating findings. Keiwan Kashi, for example, pointed out that copper supplies were finite, so developers need to reduce the percentage of copper in motors. Ms. Gutierrez said Valeo was working on developing closed material cycles in some fields. Krishnamurthy saw a need to develop modular systems that would enable scaling across hybrid and all-electric drives. Another important statement from Dhana Kad: “We shouldn’t just shift emissions to another sector – we can’t just shift to electric powertrains and think we’re done.”
At the CTI Symposium 2023, Micky Bly had spoken ironically of an electrification ‘bloodbath’ that could engulf many suppliers. In this year’s OEM panel discussion, Patrick Lindemann took up the thought, asking where the opportunities for suppliers lay, from an OEM perspective. For Brian Schneidewind and his fellow participants, the key fields are air conditioning and thermal management. Micky Bly said support was still needed for combustion engines, while Jonathon Ratliff cited battery development and production. Ford sees a need for external manufacturing capacities to cast new materials based on powdered metal, since production is space-intensive. Finally, looking to China, Mike Anderson said: “We need support to reduce the cost of batteries!”
Will BEV prevail in Long Haulage Trucks?
The question of how feasible full electrification is applies even more to heavy-duty trucks than to light vehicles. In a surprising plenary lecture entitled “The future of heavy-duty trucks – is one technology enough to decarbonize haulage?” Andreas Kammel, Traton, said that in long-haul applications, purely electric drives for heavy trucks would prevail more quickly than some people expected. Kammel believes that particularly in long haul scenarios, operators could quickly recoup their battery costs. Megawatt charging (MCS) would reduce charging times, and hence downtime. Particularly on interstates across the USA, an MCS infrastructure could be set up cost effectively. Also, travel times and routes were easy to plan. Given a successful infrastructure rollout, Kammel sees a clear lead for BEV in terms of TCO.
In his lecture “Integrated and modular – ZF’s future commercial powertrains”, Christian Feldhaus, ZF, said global variations in legislation and geopolitical conditions were the push factors, while TCO was the pull factor and infrastructure the enabler. While Feldhaus also sees BEV as the ‘endgame’, he predicts multiple drive options en route, with diesel remaining a player for quite a while. Since customers prefer different solutions, the industry needed a variety of drives, modular and scalable solutions, with flexible production facilities to match.
Challenges and solutions in batteries
On the Supplier panel, Chandra Krishnamurthy coined a memorable phrase, saying: “The devil is sitting on the battery”. There were also two plenary lectures on new battery developments:
Tim de Bastos, LG Energy Solutions, shared his take on current battery developments in his talk entitled “The state of energy solutions”. Firstly, the ‘pain points’ in EV proliferation were costs, infrastructure, range anxiety and the political environment. Hence, the requirements for new battery types were price, safety, fast charging ability and range. An 80% charge should take 10-20 minutes in the premium segment, and 20-30 minutes in the mainstream. With a full charge, range should be 700 or 500-600 km respectively. LG saw lithium-sulfur batteries and solid-state batteries as future technologies. Broadly speaking, Tim de Bastos defined four areas that determine quality: materials (e.g., eliminating cobalt in future), new processes (e.g., solvent-free dry electrodes), cell to pack with pouch cells, and better diagnostics via cloud and big data processes. The speaker then outlined LG’s next steps up to 2030 and beyond. The polymer-based semi-solid-state battery would enter series production by 2027, the lithium-sulfur battery by 2029, and the polymer-based solid-state battery by 2030. Further down the road, the sulfide-based solid-state battery could become reality. This would require no lithium, and would comprise high-nickel cathodes, silicon anodes and a solid electrolyte.
Taylor Hansen spoke on behalf of Webasto, a company many people still associate with roof solutions. But Webasto is also a leading supplier of aircon systems, which spans the arc to battery technology. In her presentation “Traction battery considerations for medium and heavy-duty vehicles”, Hansen covered solutions for commercial vehicles. She began by saying that requirements varied widely across different applications in terms of range, operating behavior, packaging, robustness, thermal management or safety. Sometimes, objectives could conflict – for example service life vs. range, since the latter required a higher discharge capacity (specifically, 90 vs. 80%). Severe-duty applications had their own specific requirements, for example in terms of thermal propagation, salt-water safety or operation in mining. Interestingly, Hansen said cylindrical cells were more powerful, while prismatic cells were more durable and less expensive. On the subject of common battery chemistries, she said LFP (lithium iron phosphate) had several advantages over NMC (nickel manganese cobalt oxide): LFP could endure more charging cycles, was cheaper, and more thermally stable. On the other hand, NMC offered higher energy density and higher efficiency at low temperatures. LTO (lithium titanium oxide) was also an option for severe-duty and marine applications: its discharge capacity and thermal stability were very high, but at around $1000/kWh, it was also very expensive, she said. Taylor Hansen closed by touching on two other important topics. ‘Harmonious’ thermal management could yield up to 30% more range, and batteries should have redundant battery management – primarily to increase safety.
New production concepts for BEVs
The day before the symposium, there was an excursion to Caresoft in Livonia, MI. Here, the company gave fascinating insights into the benchmarking of electric cars from Tesla, Ford, VW, BYD and others. The visit went down well with participants, and may be repeated in future. In his plenary lecture “Global automotive modular evolution for electric vehicles”, Matthew Vachaparampil, Caresoft, addressed one aspect of the topic. Among other things, he compared various methods of bodywork production, including Tesla’s ‘Giga Casting’ and ‘Unboxed Manufacturing’. The speaker showed how these cost $150 to $300 more in materials, but save 30% in work time, meaning they saved money overall. As audience questions revealed, however, conflicting objectives are at work here. For example, fewer body parts could be a disadvantage when repairs are needed.
Abey Abraham from Ducker Carlisle spoke on “The role of aluminium, steel, and other materials in the future of NA automotive mobility”. He began by echoing the view that in 2030, a good 60% of cars will likely still have an ICE on board. Nevertheless, lightweight construction was definitely necessary in order to cut fuel consumption. Aluminum would partly replace steel, but lightweight high-strength steels would also become more important, as would material composites, including in combination with steel. Abraham also predicted more processes like Giga Casting to save work steps and weight, saying that Honda, for example, was also heading in that direction. For batteries, Abraham expects more cell-to-pack designs, despite accessibility issues. He also emphasized the importance of recycling, even with lightweight construction; materials such as carbon fiber were not suitable.
More variety, more female engineers
The foremost insight from this year’s CTI Symposium Novi is probably that hybrid drives will be around for longer than expected. As chair Patrick Lindemann said at the end: “There is no hybrid comeback; hybrids were never gone.” That said, it would be wrong to cast doubt on the industry’s determination to electrify. As the examples and arguments given here show, developers are continuing their quest for new and better solutions in all areas of electrification. The current development could argue in favor of stronger hybrid electrification, and for scaling components like electric motors, power electronics etcetera as part of an overall electrification strategy. We look forward to seeing how this topic evolves – first at the CTI Symposium Germany in Berlin (December 5-7, 2024) – and, of course, next year back in Novi.
Finally, two other highlights at Novi deserve a special mention: The new, dedicated Female Session on May 15 was highly successful, and very well attended. The CTI has entered into a partnership with the AWA Foundation to involve women more closely in the symposium as participants and speakers in an exchange of experiences and experts on the diverse topics of the industry. With more female plenary and specialist speakers this year, and also in the panel discussions, the first fruits are already appearing.
Something else was also new this year: In addition to his summary, chair Patrick Lindemann invited the entire advisory board up on stage to review their impressions, together with the audience. There were driver-friendly drinks all round, and the casual, family-like atmosphere gave birth to several new ideas, such as focusing more on lifecycle assessment (LCA) in future. After all, this will be a key lever for further reducing CO2 emissions efficiently and credibly – whether from BEV, FCEV or advanced hybrid solutions.
Author: Gernot Goppelt