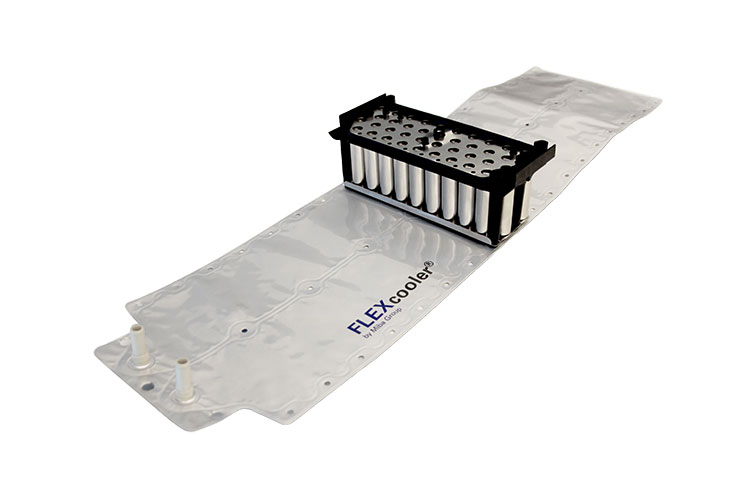
Traditional battery cooling takes the form of a plate, usually made of aluminum, with embedded channels for the coolant. The battery cells, which are usually surrounded by a metal sleeve, and the cooling plate are rigid. Direct contact, for instance due to manufacturing tolerances, always results in an air gap and thus poor thermal conductivity. By adding thermal conductive pastes, good thermal coupling can be achieved at this point.
Miba’s flexible battery cooling system now replaces the cooling plate with a heat exchanger that adapts to the shape of the battery cell. The flexibility of the heat exchanger enables direct thermal contact between the heat exchanger and the battery cell, even without the use of a heat-conducting paste. The flexible battery cooling is compatible with every cell type on the market, whether pouch, prismatic or cylindrical cells of all formats. The same applies to the cooling direction. The Miba FLEXcooler® can be integrated to cool the bottom, pole, tab or side of any type of battery cell. Once the FLEXcooler® has been integrated in the selected cooling direction, it inflates due to the coolant flow in its flow field until a positive connection is made between all surfaces to be cooled, without the need for TIM or other filling agents
The advantages of a flexible battery cooling
- Flexibility
- 100% reduction of the gap filler
- Compensation of manufacturing tolerances of the battery
- Applicable for round prismatic and pouch cells
- Lightweight and slim design
- Reduction of intercellular spaces to a minimum.
- Low weight – up to -80% of the raw material
- Improved recycling process and effort
- Low CO2 footprint
- Performance
- Safe and smart components
- Uniform cooling over the entire battery
- Electrically non-conductive