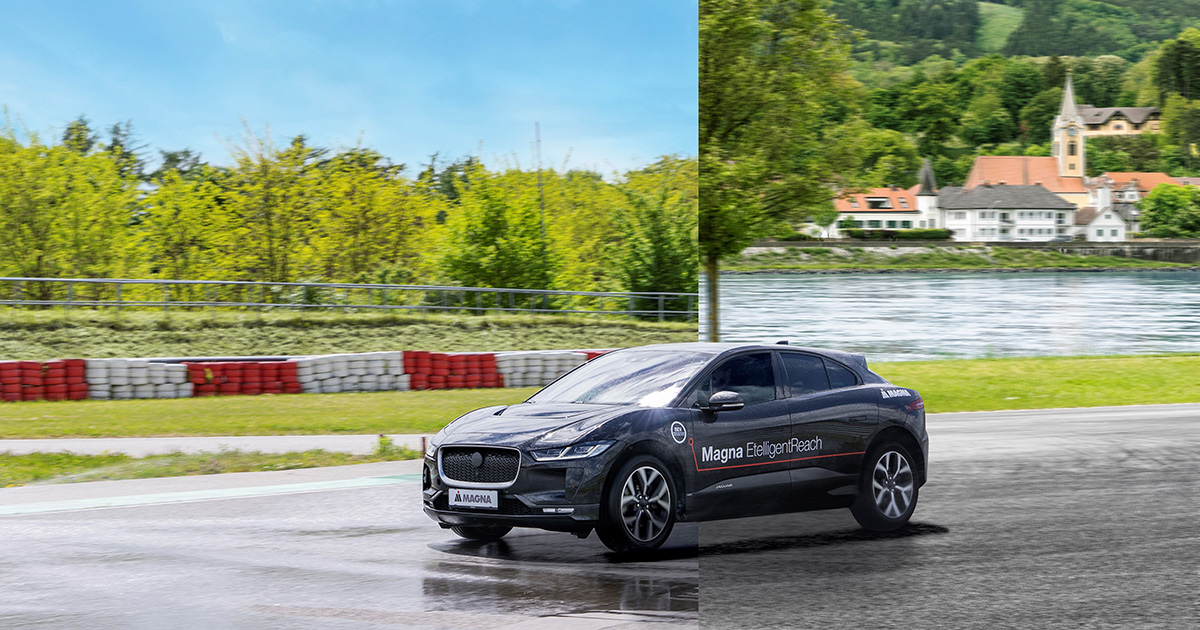
All-wheel drive electrification benefits dynamics, safety, efficiency, and convenience. Besides an advanced drive architecture, this requires consequent functional integration through software.
In electric all-wheel drives (eAWD), functions are increasingly defined through software. Magna improves efficiency as well as drivability through the ‘Magna Vehicle Motion Control’. This software-based system includes a control loop with five elements: Real Vehicle Input, Vehicle Physics Model, Vehicle Motion Control, the Smart Actuators, and the resulting Real Vehicle Behavior.
The central part of the loop is the Vehicle Motion Control strategy. This onboard software enables the vehicle to follow the targeted trajectory. It controls all relevant actuators like the e-drives, wheel brakes, possibly clutches, active chassis components, etc. For example, it will split the torque between both axles to increase driving stability and provide different modes for the driver. In the future, the data will be increasingly enriched by off-board data. The car will be able “to look ahead”. For example, Magna’s vehicle physics model feature “traction predictor” will watch the road surface ahead and include information from other vehicles through the cloud, which have passed the road earlier. All this data will be combined in the vehicle physics model.
For the Vehicle Physics Model, Magna uses all existing vehicle and drivetrain input. ADAS and cloud information etc. With this data, the vehicle will be modeled as a “virtual twin”. This allows for calculating how the vehicle moves, or how it will be positioned on the upcoming route. A crucial aspect of vehicle controllability is what is known as side slip calculation and the related active sideslip angle limitation. This angle describes how much the axles slip sideward in relation to the intended trajectory, leading to over- or understeering. In current state-of-the-art vehicles, closed-loop control is mainly done by comparing the actual yaw rate to the requested yaw rate and the actual accelerations to the requested one.
The Smart Actuators take the control strategy to the road. Besides the wheel brakes, torque vectoring elements, ABS/ESP, decoupling devices, etc., Magna also defines the e-motors as smart actuators due to their ability to exactly manage the torque. They can take over a large part of the wheel brake tasks in many driving situations. Magna is currently merging the e-motors and brakes into one single domain.
The last element in the loop is the Actual Vehicle behavior. The following example shows how different vehicle configurations will behave on the road. We compare an all-wheel drive vehicle without torque vectoring with an eAWD vehicle including integrated control of e-drive and brake. Both vehicles are driven on the same track by the same driver at the same speed. The image shows a typical situation:
The tire slip indicator in the bottom right shows how each wheel behaves in a certain driving situation. The circle of the wheel slip indicator essentially represents the friction value that may not be exceeded to maintain driving stability. Each dot represents one of the four wheels. The size of the circle represents the given friction value. In this example, the circle has a constant size during driving, because the friction value remains constant on the track. With a reduced friction value, the circle would be smaller. This illustrates, why the combination of the control loop steps described above, and the central role of the motion control software, is crucial.
In the driving situation shown, the eAWD vehicle with the integrated control of e-drive and brake (black) is stable, while the standard eAWD vehicle (white) exceeds the traction limits with its front wheels. The control software manages to keep the “stress” of each wheel on an almost equal level. While the driver of the white vehicle needs to make a lot of effort to keep the vehicle on the road, the black vehicle remains stable and still has a considerable safety margin.
The improved controllability enables several advantages: The efficiency benefits, because of improved brake blending and a higher regeneration share through the e-motor allowing for reduced power consumption. This especially applies to real-world driving, due to generally higher longitudinal accelerations than in current homologation driving cycles.
As to safety, the trajectory for every driving situation is significantly improved. It is easier for the driver to handle the vehicle even in critical situations like avoidance maneuvers, low friction spots, etc. This also applies to regeneration and braking, as the integrated software domain allows for better controllability.
The vehicle dynamics benefit from an increased achievable lateral acceleration and the related increase in cornering speed dynamics with the physical limits. Finally, the improved controllability like reduced steering effort, etc., as well as the predictive abilities allow for clearly improved comfort and convenience.
Experts:
Julius Meinecke, Senior Manager, Product Management, Connected Powertrain, Magna Powertrain
Simon Kaimer, Senior Manager, Vehicle Functions and Systems, Magna Powertrain