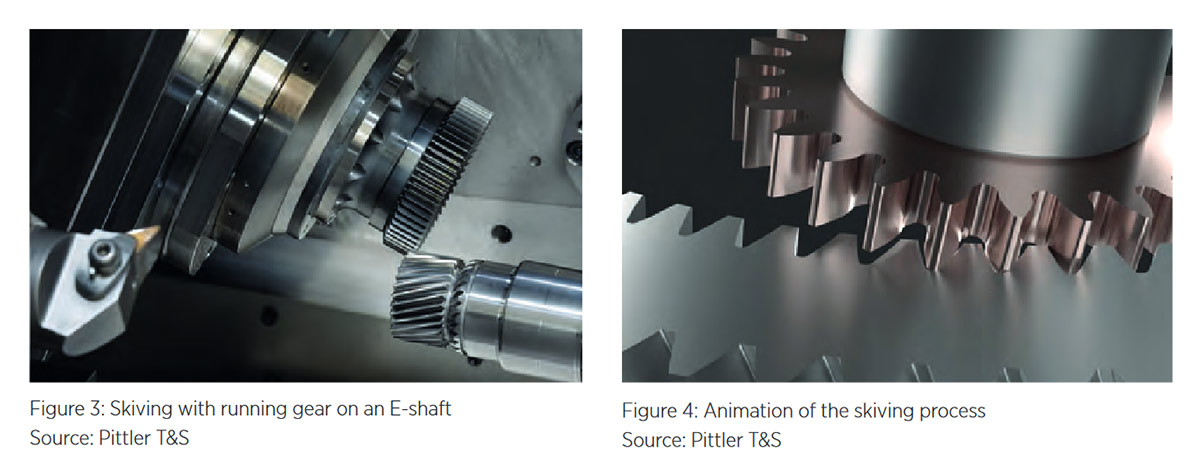
Perfect E-Shaft with Integrated Production Solution
For the transmissions of electric vehicles to develop the desired high torque under all driving conditions, a very large gear ratio is needed, which requires high speeds. And to ensure sufficient momentum at all speeds and enable the driver to accelerate without shifting gears, the electric drive has to achieve up to 15,000 rpms, which is about three times that of a typica combustion engine. This puts a lot of strain on the rotor shaft. The manufacturers of rotor shafts are thus facing new challenges, such as the significantly lower shape and position tolerances and the need for greater machining precision.
Lower shape and position tolerances as well as fine surfaces also help to avoid vibrations from moving components and thus minimize the background noise of the drive system, i.e., optimize the NVH behavior. Since electric motors work virtually silently, the noise emissions are much more critical than with a petrol or diesel engine.
Integrated production solution for E-shafts
In order to meet these very stringent requirements, the DVS TECHNOLOGY GROUP (DVS), an association of experienced companies with core competencies in the field of machining technologies, has developed a forward-looking, integrated production solution for the turnkey machining of monoblock E-shafts from raw to finished parts. This means that these complex drive components can be manufactured up to 40% more economically.
Soft machining by skiving
First in the production chain is the Pittler V300, an innovative multi-technological production solution that combines fully automatic turning, milling, and drilling operations as well as gear cutting using the highly productive skiving process. This enables complete soft machining of the hollow shafts in just two setups on one machine. It reduces setup, transport, and idle times, which means that the total processing time is also shorter. In addition, processing on just one machine means lower investment costs and a shorter time-to-production.
Skiving is used for the production of gears in green-machining. This is a metal cutting process for the production of gears which is based on a patent filed by Wilhelm von Pittler in 1910. Thanks to the latest developments in manufacturing technology, skiving has emerged as an efficient and flexible alternative over recent years for the gearing of components.
One of the characteristics of skiving is the oblique arrangement of the tool axis to the workpiece axis (Figure 3). This is called an axis intersection angle. This positioning of the tool, a defined axial feed, and the coupled speed of the tool and workpiece result in a relative movement. This relative movement “peels” the
tooth gap out of the workpiece along the main cutting direction.
The contact kinematics of skiving require a tapered tool when the cutting point is on the direct line connecting the tool and workpiece axis. To avoid this, the DVS Group has further developed the POWER-SKIVING process: The cutting position is shifted in the Y direction out of the direct line connecting the tool and work-piece axis. This optimization enables the use of cylindrical tools with a substantial increase in tool life through frequent regrinding of the tools. Accordingly, the cost of tools is reduced significantly.
The quickly changing cutting forces of the skiving process cause vibration in the machine and the control system. That is why skiving requires extremely rigid machine structures, tool and workpiece carriers as well as highly optimized control circuits. This is precisely what the Power Skiving machine concepts from DVS were designed for.
Skiving technology comparison
Compared to other processes, skiving stands out due to a number of processing characteristics:
Skiving
Advantages:
- Short primary processing time
- High metal removal rate
- Moderate tool costs
- Can be combined with other machining methods
- Production of internal and external gears in one clamping
Disadvantages:
- New technology
Shaping:
Advantages
- Flexible
- Simple technology
Disadvantages:
- Long primary processing times due to idle stroke (about 3–8 times longer)
- Higher workpiece costs
- Can not be combined with other processes
Hobbing
Advantages:
- High metal removal rate
- Short primary processing time
- Low tool costs
- Proven technology
Disadvantages:
- Suitable only for external gears
- Requires larger run-out compared to skiving
Broaching
Advantages:
- High throughput with large quantities
- Very short primary processing times
Disadvantages:
- Suitable only for external gears
- Requires larger run-out compared to skiving
Using skiving for the production of gears with green machining has a number of advantages. Two of the unique selling points are the possibility of manufacturing internal and external gears in one clamping as well as the possibility of machining all-in-one or combine it with other machining.
Grinding and hard turning on the Buderus 235VH/M
The heat treatment of the shaft is followed by the first hard-fine machining step. Most rotor shafts have a similar design due to the required properties. A typical monobloc E-shaft consists of a running gear or spline, two bearing seats, two sealing surfaces, and a rotor seat. Depending on how the laminated core is fixed, the rotor seat is additionally provided with notches or spanner flats.
The bearing seats and sealing surfaces are machined by plunge grinding (Figure 10) and the rotor seat by peel grinding or plunge grinding (Figure 11). End faces and cut-ins are usually machined by hard turning during the same clamping, as a rotary turret can be integrated into the Buderus 235VH/M if required. Tolerances in the micrometer range should be achieved on the bearing seats, sealing surfaces, and rotor seats. Experience has shown that typical tolerance requirements range between 0.004–0.03mm for cylindricity, 0.002–0.025 mm for roundness, 0.005–0.08 mm for coaxiality, and 0.008–0.1mm for concentricity. For sealing surfaces and rotor seats, it is also necessary to obtain a peak-to-valley height of up to 1 μm. This accuracy is possible by grinding with the Buderus 235VH/M in a single clamping.
The 235 VH machine concept stands for the highest quality, low unit costs, and maximum adaptability. The innovative machine platform is specially designed for the machining of rotationally symmetrical shaft components with a diameter of up to 300 mm and a length of up to 1,000 mm.
The machines enable both combined and simultaneous machining processes. The flexible configuration options enable a wide variety of machining technologies from grinding, hard turning, and honing to the use of powered tools.
Buderus is also a specialist on the use of center drive technology. The latest development is the 235VM center drive machine with an advanced drive head. This head achieves a orking speed of up to 2,500 rpm and thus also enables the hard turning of components. The main advantage of the center drive technology is the fact that inner and outer geometries can be machined in just one clamping, which results in greater precision as well as significantly higher efficiency.
Gear honing – advantages of honing for generating grinding
The last step in the DVS process chain before the hollow shaft is ready for installation is gear honing. In recent years, the DVS subsidiary Präwema has further developed a technology that enables lower friction losses when the gears roll off. This so-called “power honing” process is now standard in much of the international vehicle industry. The honed gear surfaces are critical for the reduction of noise levels and to lower energy consumption in electric vehicles.
High workpiece qualities are achieved through some unique processing properties of honing. For example, as the cutting speeds do not exceed 12 m/min there is no grinding burn, which is usually an almost invisible byproduct of grinding due to too high cutting speeds. A high induced surface tension can also increase the service life of the gearing and reduce the risk of pitting. Moreover, the entire toothing width is machined simultaneously using the plunge method, and the surface structure runs diagonally across the flank to improve quiet running.
In addition, short cycle times, low tool costs, and the possibility of processing closely adjacent gears that cannot be processed by a worm grinding wheel make honing extremely economical.
The extremely productive process enables ultra-precise machining in gearing qualities IT below 6 and super-fine surfaces with an Rz under 1. For optimal NVH behavior, specific micro-geometries (e.g., profile angle and profile shape deviations) can be used for the running gears. Test results are available upon request.
Tool solutions for gear honing
Another important factor for gear honing are the tools and their geometry and material. The tool solutions tailored to the respective process ensure the highest level of quality when it comes to the surface and profile of toothed components. The product range of DVS Tooling covers the entire scope of gear honing tools. The main products include the PRÄWEMA ORIGINAL honing (Figure 11) and the VarioSpeedDresser (VSD) dressing tool (Figure 13).
The forces applied during gear honing for highly precise machining results are enormous. These forces in combination with component-specific influences can lead to undesirable vibrations during machining, which must be absorbed to prevent inaccuracies. This is why PRÄWEMA ORIGINAL honing rings have two zones: The geared processing zone enclosed by a second zone, the so-called damping zone. This second zone dampens the vibrations that occur during machining, preventing their transfer onto the honing head and the machine.
Pre-cut PRÄWEMA original honing rings feature quality that comes much closer to the required series quality than comparable honing rings on the market, which is usually only achieved after dressing during the process. We make this possible with Vario Speed Profiling® (VSP for short), which yields extremely high pitch accuracy and profile shape quality through profiling during rolling, while at the same ensuring that the entire honing ring gearing remains at a constantly high quality.
The latest generation of PRÄWEMA SynchroFine® gear honing machines uses the so-called VSD technology for dressing the honing tools. “VSD” stands for Vario Speed Dressing® and describes a dressing process with a geometrically defined cutting edge in which only the leading cutter of the dressing tool enters the honing ring. Compared to conventional dressing with diamond dressing gears, VSD dressing tools achieves previously unattainable profile shapes and accuracies. The achievable roughness improves from 2.0 μm to 1.3–1.4
μm. Through the use of our proprietary DVS LaserCut finishing technology on the VarioSpeedDresser, the surface quality and profile quality of toothed components can be increased even further. During a special vibration process, the achievable roughness can be increased from 1.3–1.4 μm to 0.8 μm using a refined VarioSpeedDresser and a honing ring with special grain. The downside is that the honing time increases by 3–5 seconds.
Economy with maximum precision
By precisely coordinating all process steps, the integrated manufacturing solution developed by the DVS TECHNOLOGY GROUP enables the production of high-quality rotor shafts that meet all the requirements of EV transmissions. With this process, the DVS Group also enables highly efficient production while at the same time significantly reducing the cost per unit. In some cases, the costs are up to 40% less compared to conventional production.
Media relations:
DVS TECHNOLOGY GROUP . Kerstin Stumpf-Trautmann . Head of Marketing
Johannes-Gutenberg-Str. 1, 63128 Dietzenbach, Germany
Phone: +49 6074 3040640 – Mobile +49 171 7528052
E-mail: kerstin.stumpf-trautmann@dvs-technology.com
Website: www.dvs-technology.com