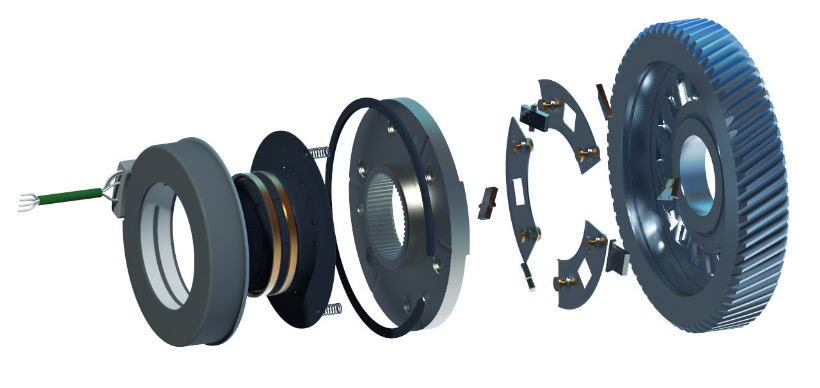
John Jennings, Director of Innovation and eMobility, Amsted Automotive
The demands on Electric Vehicles (EV) powertrain systems continue to escalate to better meet customer needs – specially extended driving range and better overall driving dynamics – and Amsted Automotive is developing solutions to meet those needs. The latest evolution for next-generation EV drivetrain systems are two variations of a multi-functional shift system with integrated one-way-clutch functionality.
The EV market is growing at a fast pace, creating new and unique challenges for our automakers and tier 1 automotive suppliers. Traditional internal combustion engine (ICE) drivetrains and EV drivetrains are not the same. Without the ability to meet the unique requirements of EV powertrain systems, there are missed opportunities for new success within the transportation sector. Electric propulsion is fundamentally different than ICE propulsion, and the ability to accurately control an electric motor allows for a fundamental paradigm shift that allows new transmission and drivetrain designs to be developed.
Multi-Speed EV Drivetrain
The next generation of EV propulsion systems will need to be further optimized for function, efficiency, range and cost as the EV market scales up. This includes the need for new solutions to improve energy efficiency and extend the range of EVs.
The focus on EV propulsion systems optimization is on right-sizing the eMotor, inverter, drivetrain and the system thermal management. There is also a special focus on reducing or eliminating any sources of mechanical drag and friction elements. Multi-speed drivetrains can provide additional opportunity to optimize EV propulsion systems beyond what can be achieved by right-sizing the individual components and systems alone.
Compared to a direct-drive EV drivetrain, a multi-speed system can increase the low-speed, high-torque capability and also increase the high-speed, low-torque performance and efficiency. Effectively, a multi-speed system enables increased propulsion system perfor- mance without increasing the size of the eMotor and power electronics. This solution also reduces the associated thermal loading. This is especially beneficial for applications with heavy loads and a lot of start-stop usage.
From a vehicle performance perspective, a multi-speed driveline system can help to improve energy efficiency, vehicle range, launch torque, towing capacity, gradeability, highway performance and thermal durability.
To illustrate the benefits of a 2-speed shift system, this figure shows a typical eMotor torque and speed map. Adding a Second gear can increase the low-speed, high-torque capability while also increasing the high-speed, low-torque performance and efficiency
Transition of Transmissions to EV Drivetrains
The overall principle for multi-speed transmissions is the same for ICE and EV drivetrains, which is to optimize propulsion system efficiency, engine or motor efficiency, vehicle range, launch torque, power and overall vehicle performance.
However, in an EV architecture, each axle may have a dedicated eMotor with the possibility of a dedicated multi-shift system. This leads to advantages for the EV architecture. The dedicated power at each axle allows for the torque and speed to be controlled independently between the front and rear axle systems. This enables the possibility of different features at each axle such as percentage torque split between axles, gear ratios and ratio staggering between the front and rear axles. Furthermore, the shift and disconnect functions can be controlled and synchronized using the propulsion motor controls. In the case of AWD systems, one axle can be used to compensate for the other axle during a shift in order to maintain continuous vehicle power and a smooth gear shift feel.
All of this creates opportunities for new and innovative approaches for managing multi-speed shift systems that were not possible without the accuracy and control of electric motor propulsion controls and simply are not possible in an ICE architecture.
Amsted Controllable Clutch Use in a Powershift Application
The Amsted controllable clutch incorporates two proven technologies: a controllable mechanical diode one-way clutch (OWC) in combination with an existing friction clutch.
The unique Amsted OWC enables automatic and seamless gear shifts with no torque interruption in conjunction with a friction clutch pack.The controllable OWC can be quickly engaged for reverse gear or electric regeneration without the possibility of blocked shifts. This core Amsted OWC technology has been used by global automakers in mass-production automatic transmissions, and there have been more than 60 million produced over the past 25 years.
Recently, the Amsted Controllable Clutch technology has been adapted for 2-speed EV applications in both co-axial (planetary) and parallel axis drivetrain architectures. The system incorporates the Amsted Dynamic Controllable Clutch (DCC) with electromagnetic actuation technology and is a bi-stable actuation design that latches in state without a constant power supply. The system shifts ultra-quick – 17 milliseconds – without the possibility of blocked shifts.
The Controllable Clutch system can be integrated into gears or differentials within the EV drivetrain to minimize package space. This system is currently on a production path to enable Powershifting for seamless and efficient electric vehicle performance.
Amsted Electro-Mechanical OWC Shift System (Next-Generation EV Shift System)
The next step of product evolution for the Amsted multi-speed shift systems is an electro-mechanical shift system that eliminates the drag losses associated with wet friction clutches. Leveraging the unique ability of electric motors and the ability to accurately control and manage on-demand torque, Amsted can eliminate the need for wet-friction clutches.
Starting with the Amsted Powershift System, the friction clutch and 2-mode OWC is replaced with one 3-mode (3-position) OWC system. This new multi-speed shift system offers a controllable bi-directional OWC with a forward OWC and a controllable reverse OWC operation. The new 3-position mechanical shifting system is created by combining the elements of a OWC (1st gear) on one gear while utilizing an on-off disconnect (2nd gear) on the other gear. The passive forward OWC and controllable reverse OWC when combined provide 1st gear forward drive, regen, and reverse vehicle functions.
The Amsted Powershift System incorporates a OWC disconnect and a friction clutch pack to provide the advantages of a multi-shift system for EV architectures using
proven, production technologies.
For further functionality, controllable-passive OWC modes can also be incorporated for the 2nd gearset in addition to the 1st gearset utilizing a common electro-mechanical actuator enabling additional vehicle functions that include 2nd gear forward coast. This can provide further shift customization to reduce shift time, improve shift smoothness and eMotor matching utilizing Amsted 4 and 5 mode actuation technology. In this configuration, the OWC and controllable OWC provide the shift transition functions, allowing the electric motor to transition between gear speeds. The OWC function then enables an automatic engagement and disengagement with the appropriately selected gears.
For example, to complete a 1st to 2nd gear upshift, the controllable OWC for reverse is disengaged and the forward OWC is then staged for a gear shift. The shift is accomplished by decelerating the propulsion motor, causing 1st gear to automatically disconnect via the OWC. When the motor speed matches the 2nd gear speed, the second gear OWC will automatically engage and complete the shift. At any point after the second gear is connected, the system is synchronized and the controllable OWC can be engaged for regen braking.
For a 2 nd to 1 st gear downshift, the order of shift sequence is simply reversed.
Advantage of Amsted Electro-Mechanical OWC Multi-Speed Shift Systems
First, we’ll look at the specific advantages compared to traditional Powershift System with friction clutches:
- Friction pack is eliminated
- Reduced weight of system
- Reduced package space
- Eliminated oil circuit and pump for friction pack
- Eliminated actuation system for friction pack
- Improved efficiency – no friction elements
- No wear particle contamination from friction surfaces (supports sustainability).
- Lower cost
Advantages compared to traditional dog clutch technologies:
- Smoother and faster shift times
- Automatic OWC shifting (gear engagement and disengagement)
- Shift times are managed only by the motor and motor controls – no synchronization is required between motor and shift actuation devices
- Simplified system controls
- System can shift when vehicle is stopped
- Improved reliability (no blocked shifts)
- Eliminates shift fork hardware and related package space
- Flexible design applications: can be used in both parallel-axis and co-axial drivetrains
- Options for 3, 4 and 5 mode operations
Who is Amsted Automotive?
In 2021, Amsted Automotive Group brought together Means Industries Inc., Transform Automotive, SMW Manufacturing, and Burgess-Norton Mfg. Co., Inc. to form a new and innovative technology team. The integration provides an expanded global presence with 21 facilities in North America, Europe, and Asia to serve the global automotive, off-highway and mining industries with a robust manufacturing footprint, producing over 100 million components and assemblies annually. The group combines design and engineering expertise, strategically aligned to be a leader in precision products and efficiency solutions for electrified, hybrid and ICE propulsion systems. Amsted Automotive Group plays an integral role in global automatic transmissions designed and manufactured in North America, Europe, and Asia.