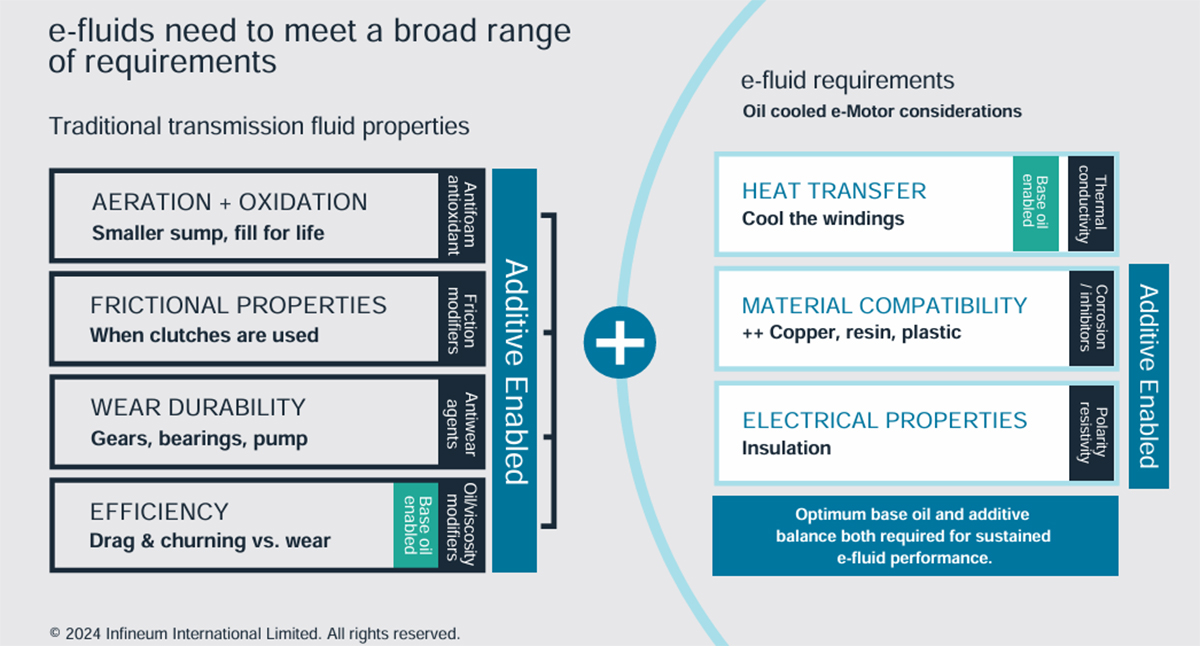
As automakers work to decarbonise, most are opting for powertrain electrification, an option that is driving growth in dedicated hybrid and electric vehicle transmissions. However, these systems present new performance challenges that require dedicated fluids to ensure their complete protection. As leaders in driveline additive technology and e-fluid formulation, Infineum has invested in the development of step-out technology and innovative new test methods to ensure our e-fluids deliver the required performance in critical areas.
Andrew Wood, Driveline Fluids Technologist, Infineum UK Ltd
Scott Campbell, Hitesh Thaker, Masahiro Ishikawa, Driveline Fluids Technologists, Infineum USA
The pressure to decarbonise, coming from both regulators and con sumers, means the number of hybrid and battery electric cars on our roads is growing. Which in turn means the use of reduction gearboxes and dedicated hybrid transmission systems are also increasing. This expanding electrified vehicle parc needs bespoke e-fluids, that provide not only traditional transmission fluid properties but also meet new e-specific requirements.
Fig. 1 e-fluid requirements
It’s a careful balance. As well as meeting all of the requirements in Figure 1, fluids must be formulated to optimise transmission performance and protection. And, in today’s lower viscosity environment, this is even more vital, which means careful component selection is important when formulating fluids for these applications.
These new electrified vehicle performance challenges require dedicated e-fluid technology. As leaders in driveline additive technology and e-fluid formulation, Infineum has developed dedicated e-fluids, optimised for excellent field performance. To assess these new fluids, we’ve developed innovative new tests in some of the critical areas, designed to be closer to the real-world application than currently available industry test methods. Two recent examples are a high-speed aeration test (HSAT) and an energised copper test (ECT), which have given our technologists new and exciting insights into fluid performance.
Material compatibility testing
With motors now being placed into the transmission, a number of materials are being introduced that are significantly different from those used in conventional powertrain architectures. For example, the copper wire and connections are susceptible to corrosion, which can lead to electric current leakages or to a short circuit in the transmission. These potential issues mean many OEMs see copper compatibility as an important e-fluid design parameter.
With motors now being placed into the transmission, a number of materials are being introduced that are significantly different from those used in conventional powertrain architectures. For example, the copper wire and connections are susceptible to corrosion, which can lead to electric current leakages or to a short circuit in the transmission. These potential issues mean many OEMs see copper compatibility as an important e-fluid design parameter.
Infineum’s energised corrosion test (ECT) uses a single printed circuit board with copper grids, that can be used with a covering board to provide a capillary gap (Figure 2). Board spacing can be tuned with a spacer washer and various board designs have been used to investigate trace spacing impact.
Fig. 2 The oil immersed energised corrosion test (ECT) allows us to screen technology to ensure good copper compatibility.
Tuning trace and board spacing had a significant impact on fluid performance (Figure 3). These data highlight the critical importance of tuning test conditions and set-up to screen for real world performance.
Fig. 3 Impact of trace and board spacing
The novel video imaging system has delivered new insights into copper corrosion mechanisms (Figure 4).
Fig. 4 Deposit / dendrite growth between anode and cathode
This new rig is helping us to better understand some of the parameters impacting corrosion and the ways corrosion progresses. These insights will be helpful in developing advanced e-fluids capable of delivering better material compatibility performance.
New high speed aeration test
Infineum has also developed a high-speed aeration test (Figure 5), which more closely matches the conditions found in high-speed e-motors and gearboxes vs the standard ASTM test – addressing a gap in e-fluid performance.
While ASTM D892/D6082 use airflow to generate foam in the test fluid the foam may not be representative of aeration experienced in real world electric vehicle hardware, where e-motors and gears spin at >20,000 rpm – much faster than in conventional ICEs.
In electrified applications, high speed shear from gears and bearings can lead to increased aeration of the driveline lubricant. This is a challenge since it can cause cavitation. This leads to irregular fluid film and loss of hydraulic performance, resulting in wear.
Using the existing ASTM D892 and D6082 foaming test as a starting point, our objective was to mimic the impact of parts spinning at speeds of up to 27,000 rpm and to add in a high-speed shearing and churning effect to simulate the aeration caused by parts spinning at these very high speeds. Automation and video capture help to ensure heating and timing accuracy.
The newly developed High Speed Aeration Test (HSAT) has been used to assess the impact of fluid viscosity, viscosity modifier and anti-foam selection on aeration.
Following the successful development of this new test, Infineum is pursuing options for industry standardization of the HSAT.
Fig. 5 The Infineum HSAT test set up mimics the effect of parts spinning at extremely high speeds under shearing/churning
Conclusion
As leaders in driveline additive technology and e-fluid development, Infineum has invested in developing new test methods to provide insights into critical performance areas. The deeper understanding of materials compatibility and aeration is helping us to develop step-out dedicated e-fluids with the optimal performance balance designed to protect electrified transmission systems.
Our new test methods give us a fast and effective means to screen a wide number of formulations.
Following on from these laboratory tests, our advanced e-fluids are tested in real-world conditions. We have already completed almost three million kilometres of field trials across the globe – testing our extensive e-mobility product portfolio in a wide range of hybrid and electric vehicles.
Infineum technology is setting the e-fluids benchmark with next generation products to provide performance you can rely on.
About Infineum
Infineum is a specialty chemicals company with strong research and development capabilities focused on innovative chemistry that plays a crucial role in sustainability. They provide products essential for the electrification of mobility and work towards making internal combustion engines as clean as possible. Their expertise extends to generating sustainability advantages for numerous new markets globally. The company has a rich heritage supported by leading-edge research and development activities, having been innovators of additive products for nearly 80 years. These products are used in automotive, heavy-duty diesel, and marine engine oils, diesel fuels, and specialty applications such as transmission fluids and gas engine oils. Their smart solutions have become key components of today’s most demanding applications and advanced hardware systems. The organization operates worldwide production facilities with sales representation in more than 70 countries.