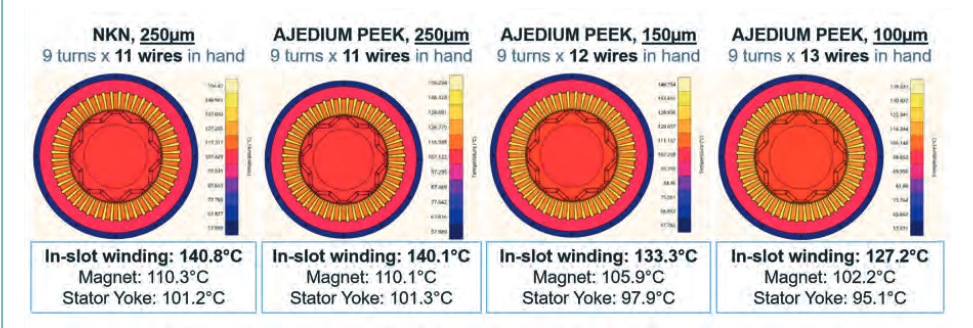
DeeDee Smith, Luigi Marino, Brian Baleno
Solvay Materials
A significant challenge for eMotor 800 Volt designers is to design smaller and more compact eMotors. Successfully doing so allows for the potential to reduce the mass of both the eMotor and battery pack. A new slot liner material, Ajedium™ PEEK films, gives engineers the design freedom to down-size their eMotor as well as achieve weight savings.
Most eMotors utilize conventional slot liner materials such as paper and paper laminates. A major challenge for both paper and paper laminates is that as eMotors move from 400V to 800V systems, the increase in voltage leads to an increased thickness of the slot liner.
Engineers typically need to balance the copper fill factor, the heat rejection capability, and achieve the right level electrical insulation that guarantees the right life expectancy and reliability. Therefore selecting the right slot liner insulation properties and thickness plays a pivotal role in the overall design of the eMotor.In order to quantify the value of using a PEEK slot liner, a virtual engineering software was used (ALTAIR FluxMotor 2021). Figure 1 below shows the eMotor design conditions used in the simulation.
Figure 1: Design inputs for virtual engineering simulation
Three different thicknesses of PEEK slot liners were used in the study: 100 micron, 150 micron, and 250 micron and compared to 250 micron NKN (paper laminate).
Figure 2: Virtual engineering results comparing NKN to PEEK
Virtual engineering determined the number of conductors that can be allocated in the slot by maintaining the same number of turns and winding layout. Figure 2 above shows the improved thermal behavior enabled by PEEK (vs NKN) where Ajedium™ allows for increased slot fill factor (at 100 and 150 microns), reducing not only winding but also other sub-components temperature.
The PEEK design advantage is enabled by using thinner slot liners which improve fill factor and heat transfer, thanks to the lower needed thickness and the higher thermal conductivity value of PEEK (0.17 W/mK).
The efficiency and thermal benefit of PEEK can be factored into more compact eMotor designs. The considered temperature reference was the peak value obtained during a targeted drive cycle simulation and not just the one obtained on a single operating point, which can be misleading.
A 250 micron NKN slot liner was used as the baseline and simulated over the targeted drive cycle. The same was done with 150 micron PEEK slot liners. The same motor length (84 mm) was initially taken into account, which showed a temperature drop. The next step was to factor in the reduction of the maximal winding temperature in an effort to make the eMotor more compact. A reduction in the motor length results in an increased motor temperature because there is less heat dissipation. This occurs due to the lower heat exchange surface, and a higher eMotor load (phase current). The overall target was to reduce the length until the original maximal winding temperature was observed again. These steps are summarized at Fig 3.
However, the fully optimized design with a thinner and more thermally conductive slot liner would probably have a slightly different L/D (length over diameter) ratio. Hence, this optimization method would lead to conservative results on the benefits that an improved slot liner would provide.
Figure 3: Stator and Rotor mass reduction with thinner PEEK (150 micron) slot liners
Figure 4 summarizes the overall aspect of optimizing eMotor slot liner thickness. Not only do thinner PEEK slot liners provide both motor compactness and light-weighting, up to 6.3% reduction in this case study, there is also a 2.1% improvement in motor efficiency. This efficiency figure is calculated as the average obtained for the simulated drive cycle. The drive cycle was purposely designed to span all the typical operating points, with reasonable cumulative time spent on each of them. Therefore, this result has a direct impact on the expected range of the BEV as well as the potential battery downsizing for that same range.
Figure 4: Summary of Results with varying slot liner thickness
Figure 4 summarizes the overall aspect of optimizing eMotor slot liner thickness. Not only do thinner PEEK slot liners provide both motor compactness and light-weighting, up to 6.3% reduction in this case study, there is also a 2.1% improvement in motor efficiency. This efficiency figure is calculated as the average obtained for the simulated drive cycle. The drive cycle was purposely designed to span all the typical operating points, with reasonable cumulative time spent on each of them. Therefore, this result has a direct impact on the expected range of the BEV as well as the potential battery downsizing for that same range. Finally, PEEK provides many design advantages over paper and paper laminates. Some benefits of using PEEK slot liners include improved eMotor efficiency, potential reduction in the length of the motor, and also weight reduction of both the stator and rotor.