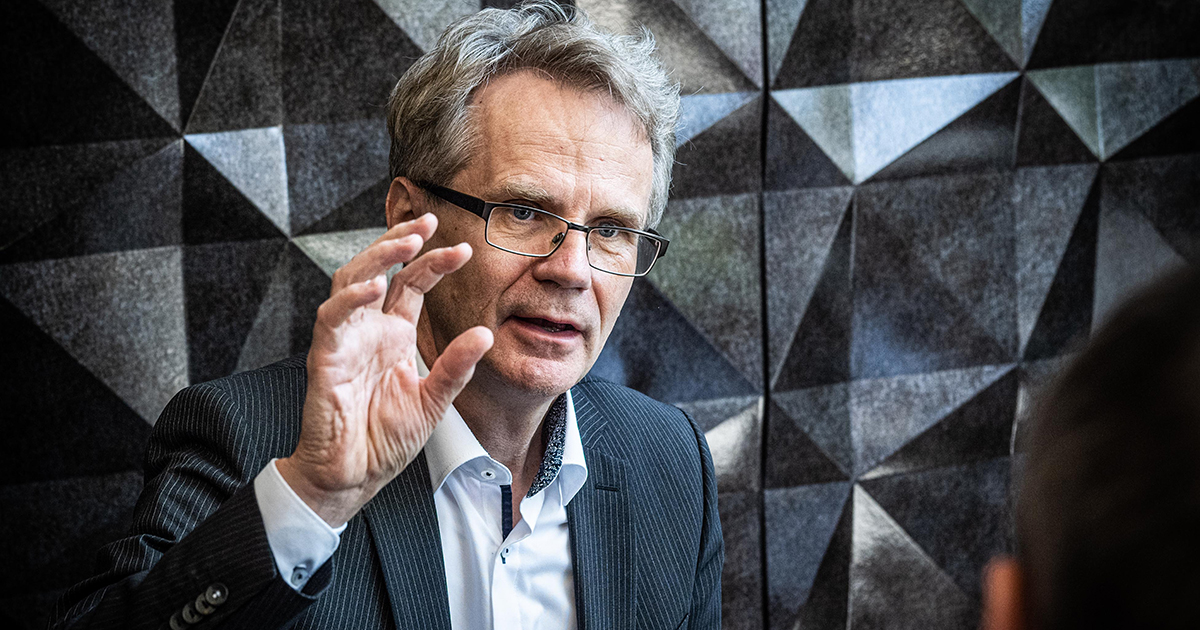
As electrification progresses, in-vehicle hardware and software architectures will evolve from distributed electronics to a “full car computer and zonal” model. We spoke with Patrick Leteinturier, Fellow Automotive Systems, Infineon Technologies, about these new architectures, new semiconductor materials, and the central role of “motion control”.
Increasingly, vehicles are becoming software-defined. What does that mean for the way OEMs and Tier 1/2 suppliers cooperate?
Software-defined vehicle (SDV) is a disruptive step in the digital transformation of automobiles and even wider the complete mobility sector. In SDV, the software takes a major role and a part of it migrates from the endpoint electronic control units (ECU) to the aggregation and transformation layer, or even to the central car computer. That will lead to a change of ownership. The OEMs do write the software on a higher level, which should speed up development, but the endpoint software that controls the endpoint devices will still be delivered by a supplier. The way tasks are shared will change. Either way, both parties will need to collaborate more than in traditional architectures. We’ll have to see who takes ownership of the development, integration, testing, and validation.
You foresee a change from distributed architectures and zone computers to Full Car Computer. When will that become a reality?
According to data from S&P Global Market Intelligence, Full Car Computer will have a market penetration of around 30% by 2034. The S-curve is starting now, and full adoption will take maybe 10 or 15 years to achieve. Practically all OEMs are working hard on this. For example, Volkswagen with Cariad. General Motors, Stellantis, and Ford are on it, and many others too. They’re not all at the same stage, and they are not running at the same speed and solution. General Motors, for example, are fully committed and are putting their full power behind it. Some OEMs may have a full car computer as early as 2027.
How will the physical bus systems change with this migration?
The common understanding is that Ethernet-based communication will become much faster. There are some limitations with CAN. The Ethernet reaches from the endpoint to the aggregation and transformation layer; it will usually be 10BASE-T1S. Then from the zone controller to the central car computer, it will be fast Ethernet. Gigabit Ethernet is already in use, but now we are even talking about 50 Gbps. With CAN or LIN, we have some limiting factors. LIN is super low-cost and very simple, but end-to-end encrypted communication is almost impossible. It is not feasible for reprogrammable functions over the air, for example. If you want a more advanced endpoint, CAN could do that, but it would need some additional CANsec to enable security end-to-end. To simplify, it depends on the SOTA “software over the air” strategy from OEM to deploy the right physical bus.
When computing is centralized, what new challenges and opportunities could arise in terms of functional safety?
Today, we have a car with distributed electronics. But in the future, many functions will be synchronized on the central car computer layer. Take vehicle motion, for example. In terms of synchronization, this has the highest complexity. You have four wheels, each with just a few square centimeters of grip on the road. And via these small friction points, you control propulsion, regenerative braking, mechanical braking, steering, suspension, etc. When we apply e-motor power to each wheel, the propulsion can steer, brake, and propel. Of course, there will be more complexity in the way sensor and actuator information need to be handled and merged. We need a seamless OS platform, dependable electronics, new security, as well as fail-operational and redundancy concepts. But on the other hand, a centralized vehicle motion control setup, in conjunction with by-wire technology, also offers new opportunities. If one wheel fails, for example, the other three can compensate via all the integrated actuators, including the e-motors.
Let’s talk about semiconductors: What materials will tomorrow’s semiconductor materials use, and what are the benefits?
Firstly, SiC is a technology that was developed a long time ago for higher efficiency in solar and wind energy. We have been in volume production for a long time, and we have a lot of experience in manufacturing. We know all the figures for reliability and robustness. SiC is superior because it lets you reduce the internal resistance and the conduction losses of power electronics. And it’s also quite good in terms of switching, so you have lower switching losses. This is extremely beneficial at part load. On the other hand, the material and its processing are rather expensive. However, we can blend SiC and IGBT (Insulated-Gate Bipolar Transistor). IGBT will work very efficiently at full load, and the silicon carbide will be used for part load. You could combine these properties across two axles – for example, IGBT at the rear and SiC at the front. But you can also combine them within the same power module, make a multiple die, and put them in parallel. This blend is much more efficient in both propulsion and regeneration and enables around 12% more range. On the other hand, the next technology GaN is already on the horizon and we are preparing that as well to be used in automotive applications and further increase efficiency to pay into decarbonization.
Semiconductors help to improve efficiency and range. But they are also part of a control system that requires a lot of energy. How can that be optimized?
That’s a great question! People need to understand that we‘re not just talking about propulsion and regenerative braking. There are a lot of energy consumers, you still have to power up and supply a large number of electronic components. So you need to be very careful about your power mode, and your strategy for deciding whether an ECU needs to be on or off. Imagine you‘re at home, for example, and you hook your EV up to the charger. It’s going to be plugged in for a long, long time… so gradually, even low energy consumption will add up to high consumption. So the aim is to only power the electronics you need. With a software-defined vehicle that is widely networked, you have to power the central computer, which consumes quite a lot of energy. On the other hand, it is also the ‘brain’ that handles power supplies vehicle-wide. Whether it’s single zones, endpoints, or whatever, power consumption can be reduced or even switched off. So if my battery capacity runs low while I’m driving, for instance, I could switch off the cabin air conditioning or heating. The good thing about the car computer is that it has all the data to make the most efficient decisions. So yes, a central computer does consume energy. But more importantly, it’s an enabler for intelligent energy and load management.
Interview: Gernot Goppelt