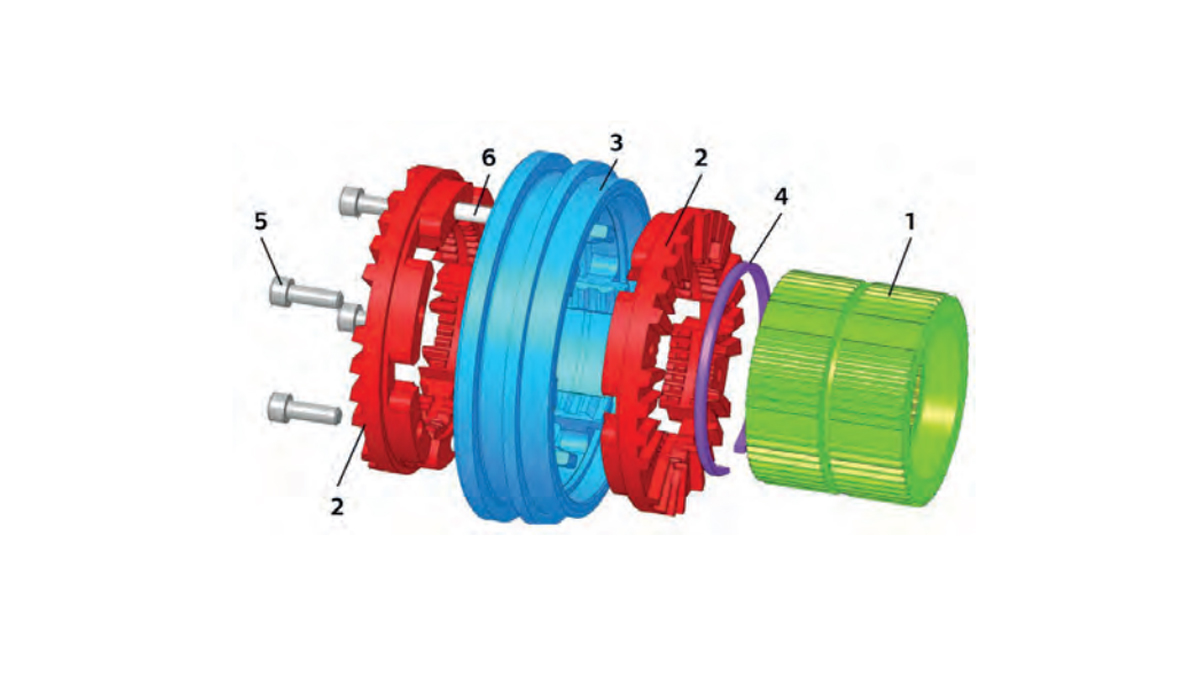
Gabriela Achtenova, Michal Jasný, Jiri Pakosta, Rômulo do Nascimento Rodrigues
Center of Vehicles for Sustainable Mobility, Czech Technical University in Prague
Dog clutches are cost-effective but often suffer from angular backlash, causing discomfort. A novel, patented design has been developed to eliminate this issue using a purely mechanical blocking mechanism. This design, fully interchangeable with conventional mechanisms, requires no extra modifications but needs an external synchronization system.
Featuring innovative gearshift dogs and blocking mechanisms, it was tested with two prototypes on test benches. The results showed the design’s effectiveness, and robustness especially for hybrid and electric vehicles, addressing key shortcomings of traditional clutches.
Introduction
Greenhouse gases, CO2 regulations, alternative fuels, and vehicle electrification are critical issues driving the rapid growth of hybrid (HEV) and electric vehicles (EV) [1]. This shift demands innovative solutions in automotive engineering. This research focuses on developing a new gearshift mechanism to meet these demands. In HEVs and EVs, the electric motor can act as an external synchronization mechanism, potentially reducing costs. Parallel hybrids, requiring a wide range of gear ratios, benefit from cost-effective gearboxes like manual parallel shaft gearboxes (MT) or automated versions (AMT) [2][3]. These gearboxes commonly use synchronizers, a prevalent gearshift mechanism in passenger cars [4].
This research aims to replace the synchronizer with a new, cost-effective gearshift mechanism that eliminates the need for synchronization while maintaining or surpassing the synchronizer’s functions [5]. Typically, a dog clutch is the simplest gearshift mechanism for constant mesh gears but has been limited by driving comfort and NVH (Noise, Vibration, and Harshness) concerns. In electric powertrains, NVH issues include gear whine and gearshift mechanisms [4],[6]. Reducing angular backlash is crucial for minimizing NVH, a feature of the new mechanism, while ensuring cost-effectiveness and compactness. More compact gearboxes tend to be stiffer, further reducing NVH [7].
This research introduces a patented dog clutch design addressing angular backlash, a common issue in traditional mechanisms [7]. Using a purely mechanical blocking system, it minimizes backlash and improves shifting quality. The form of dogs enables very fast disengagement of the speed even under load. Rigorous prototype testing confirmed its functionality, durability, and comfort, making it suitable for vehicle gearboxes.
Final design of dog clutch with blockchain mechanism
The clutch assembly (Figure 1) includes a hub (1) on the gearbox shaft, a sliding gear (2) that moves axially to engage gears, a gearshift sleeve (3) for controlling movement, and a blocking ring (4) to secure the sliding gear in positions. The sliding gear is split into two halves connected by screws (5) and pins (6). One blocking ring locks the sliding gear in all three positions (engaged/neutral/engaged) and secures the gearshift sleeve in neutral. No changes to the standard MT/AMT gear selector mechanism are needed. The design’s uniqueness is confirmed by Patent No. 307443[8] and the utility model „Schaltungskupplung“ [9]. Following design optimization, prototypes of dog clutches with a blocking mechanism were produced. Two clutches for the MQ200 gearbox were made to engage 1st, 2nd, 3rd, and 4th gears, see Figure 2. The prototype production was funded and supported by ŠKODA AUTO.
Gearshift process
The blocking ring stays concentric with the hub due to its constant contact with the sliding gear or gearshift sleeve. With six contact points, the ring maintains its shape during compression. To prevent uneven deformation, which could interfere with gear movement and cause excessive wear, the ring’s ends are bent inward. Figure 3 illustrates the gearshift process, where shifting the right gear involves:
Position 1 – neutral:Black arrows show axial backlash between the sliding gear and the gearshift sleeve. The blocking ring holds both components – sliding gear (upper) and sleeve (lower) – in neutral;
Position 2 – engagement preparation:The sleeve moves right, compressing the blocking ring, while the sliding gear remains in neutral until backlash is resolved;
Position 3 – engagement in process:With backlash removed, the sleeve pushes the sliding gear right, and the blocking ring stays compressed;
Position 4 – engagement termination:The sliding gear reaches its maximum position, engaging the gearshift dogs. Both components stop moving axially, and the blocking ring is no longer compressed;
Position 5 – engaged: The blocking ring expands back to its original position, fitting into the sliding gear’s groove, preventing clutch disengagement due to torque;
Position 6 – disengagement preparation:The sleeve moves left to compress the blocking ring. Axial backlash is present, keeping the sliding gear engaged;
Position 7 – disengagement in progress:The blocking ring is fully compressed, backlash is gone. The sleeve moves the sliding gear to
Position 8 – Disengagement Termination: The sleeve reaches neutral, but the sliding gear remains slightly engaged due to kinetic energy. The decompressing blocking ring helps move the gear to neutral;
Position 9 – Neutral:The dog clutch returns to the neutral position, same as Position 1.
Prototypes of the clutch were designed for the MQ200 gearbox, where the blocking ring withstands axial forces up to 2 kN during dog engagement, transferring a maximum torque of 200 Nm. The force needed to engage and disengage the clutch via the gearshift sleeve is about 45 N, which is well within permissible limits and comparable to manual shifting forces. The sliding gear and gearshift sleeve have been optimized for powder metallurgy. For the sliding gear, only grooves for the blocking rings and threads on one half need machining, while the gearshift sleeve requires machining of the inner groove for the neutral position. The outer groove, for the gear selector fork, is for prototype compatibility and can be omitted in future designs. No additional parts are required between the sliding gear and gearshift sleeve, ensuring concentric alignment with the hub. The blocking ring is fixed securely and cannot rotate around the shaft axis due to the pin.
Verification of the dog clutch
The fulfillment of the requirements for the dog clutch with a blocking mechanism needed to be validated against the design specifications. First experiments were static to verify the shift force and unwanted disengagement. The resulting gearshift force required to compress the blocking ring was measured to be 45 N.
Further was experimentally tested that the blocking ring functions as intended, preventing unwanted disengagement of the clutch.
The dynamic tests were dedicated for verification of function and for endurance tests. The first phase of clutch prototype testing used an inertia test bench with the output shaft connected to a large inertia disc. Tests focused on smooth shift sleeve movement and proper engagement / disengagement of the dogs. No unexpected behavior was observed.
The gearbox was connected to the gearshift robot on the inertia test stand, and gearshifts were performed with various input parameters. Mismatch speed was controlled by the difference between the stationary input shaft and the rotating wheel or by gear ratios between two gears. Figure 4 shows data from a gearshift with 3rd gear engaged at a mismatch speed of 30 RPM. The gearshift process began at 0.96 s, with rising displacement and force curves. A sharp drop in force at 1.02 s indicated compression of the blocking ring, allowing the sliding gear to move. The force increased as the dogs engaged, and by 1.08 s, engagement was complete. The gearshift took about 60 ms.
To proceed with dynamic check of the blocking mechanism, the gearbox was moved to dynamometric test bench. The function for the 3rd and 4th gears were performed with positive result. Due to test bench capacity 1st and 2nd speed were not tested.
Service life (endurance) tests were conducted for the 3rd and 4th gear clutches on the inertia test bench, with each gear being shifted 180,000 times and the gearbox output set to 89 RPM. This low speed simulated a mismatch speed of around 140 RPM, optimizing the gearshift process and eliminating the need for external synchronization. Each shift took just over 2 seconds, resulting in 220 hours of continuous testing per clutch and blocking ring.
Conclusion
The new patented dog clutch with a blocking mechanism enhances efficiency and reduces costs for electric and hybrid vehicles. It offers minimal angular backlash (less than 0.1°) and can disengage under load, improving shifting comfort and torque transmission. This purely mechanical design is compatible with standard gear selectors, including sequential shifting, and requires no additional modifications. The clutch’s blocking ring withstands high axial forces, preventing unwanted disengagement. Prototypes, tested in a standard five-speed gearbox, demonstrated up to 30 mm axial space savings compared to conventional synchronizers. The design supports effective serial production using powder metallurgy and has proven durability with a service life of 700,000 cycles.
References
[1] PILLOT, Christophe. The Rechargeable Battery Market and Main Trends 2020-2030. Lyon: Avicenne Energy, 2022.
[2] HOFMANN, Peter. Hybridfahrzeuge – Ein alternatives Antriebssystem für die Zukunft. Switzerland : Springer, 2014. Second edition. ISBN: 978-3-7091-1780-4
[3] NAUNHEIMER, Harald et al. Automotive Transmissions: Fundamentals, Selection, Design and Application. Berlin : Springer-Verlag, 2011. ISBN 978-3-642-16216-8.
[4] FISCHER, Robert et al. The Automotive Transmission Book. Switzerland: Springer International Publishing, 2015. ISBN 978-3-319-05262-5.
[5] MEHRGOU, Mehdi et al. NVH Aspects of Electric Drives-Integration of Electric Machine, Gearbox and Inverter. 2018. SAE Technical Paper 2018-01-1556. doi: 10.4271/2018-011556. ISSN 0148-7191.
[6] Wu,G.,Zhang, X.,& Dong, Z. (2015). Powertrain architectures of electrified vehicles: Review, classification and comparison. Journal of the Franklin Institute, 352(2), 425–448. doi: 10.1016/j.jfranklin.2014.04.018
[7] TŮMA Jiří. Vehicle Gearbox Noise and Vibration. New Delhi: John Wiley & Sons, Ltd., 2014. ISBN 978-1-118-35941-9.
[8] ČESKÉ VYSOKÉ UČENÍ TECHNICKÉ V PRAZE, FAKULTA STROJNÍ. Řadící spojka. Inventors: JASNÝ, M., G. ACHTENOVÁ and J. PAKOSTA. File No. MPT F 16 D 11/10. Patent No. 307443. 22. August 2018. Czech Office of Industrial Property. Patent.
[9] SCHECHISCHE TECHNISCHE UNIVERSITÄT IN PRAG, FAKULTÄT FÜR MASCHINENBAU. Schaltungskupplung. Inventors: JASNÝ, M., G. ACHTENOVÁ and J. PAKOSTA. IPC-Class F16D 11/00 (2006.01). File No. DE: 20 2018 103 633.5. 26. June 2018. Deutsches Patent- und Markenamt. Utility model.