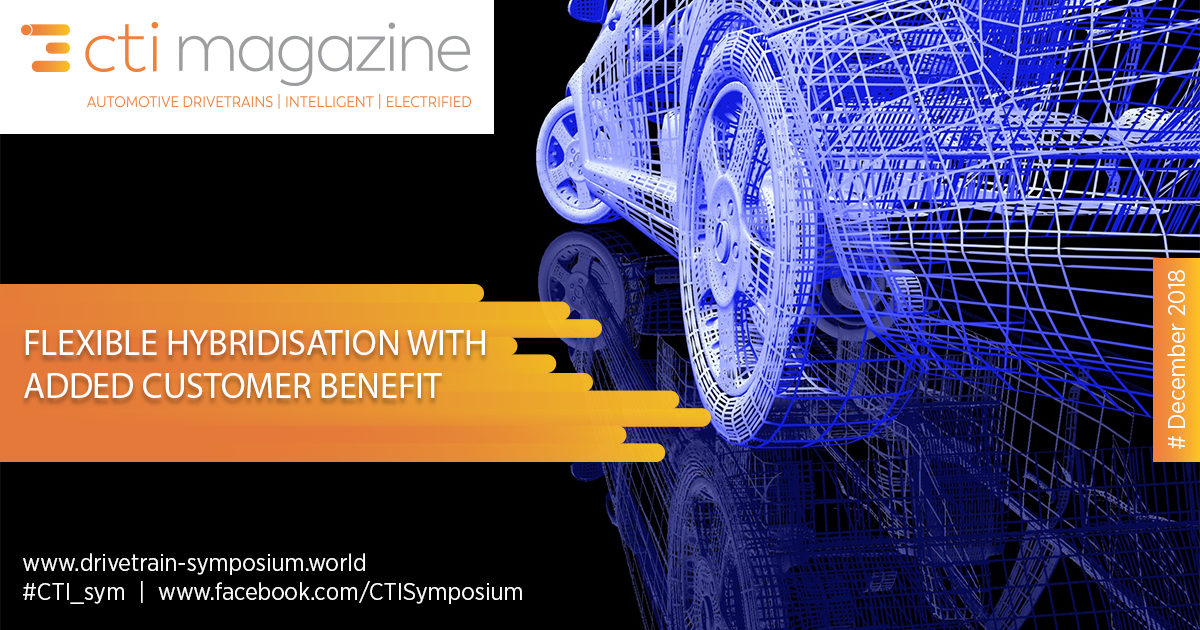
Electrification of conventional powertrains increases the number of possible variants and thus potential costs. However, end customers are not willing to accept these costs to fulfill legislation requirements. A modular and scalable electrification approach helps to create more flexibility and new customer value.
How increasing diversity can be controlled
In a conventional drive, front or rear engine combined with front-, rearand all-wheel drive principally enables six different drivetrain architectures – by adding e-motors for hybridisation, diversity increases many times over. What is more, electrification will increase the bandwidth of applications: for example, autonomous driving will trigger less powerful, more comfortable drives; at the same time, electrification enables “highend” all-wheel drives – and so forth. Fortunately, scalable drivetrain technology based on standardised building blocks enables tailor-made solutions for different global requirements, e.g. with regard to CO2 emissions, locally emission-free driving, or regionally specific customer preferences.
E-machine – the key scaling element
The e-machine (EM) plays a key role in this approach. Firstly, it is the core
component for lowering CO2 emissions. Secondly, the EM turns is an enabler for drive standardisation and scaling: the more the electric motor
takes on dynamic tasks, the fewer ICE variants are required for differentiation. Regarding the whole powertrain system over front and rear axle, the EM can make further contribution to reduce hardware complexity and add further benefit:
- Scalable, application-specific CO2 reduction
- Scalable longitudinal dynamics (traction, acceleration)
- Scalable lateral dynamics (torque vectoring)
- Scalable all-wheel functionality
- Scalable operation strategies through softwareThe prerequisite is a standardised kit of hardwarelike transmissions, axle components and e-drives as well as deep system expertise in terms of managing the drive components by software.