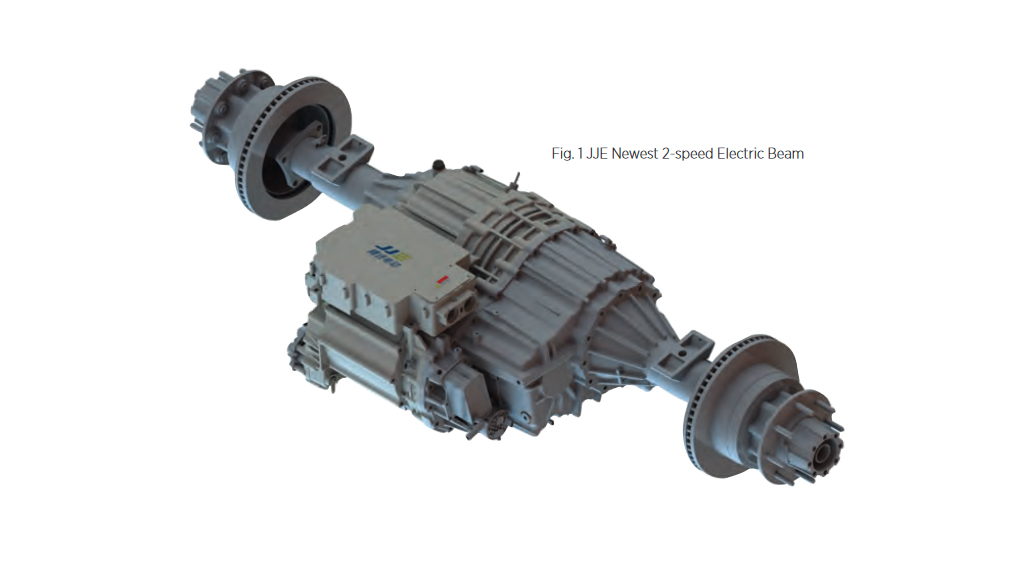
Ping Yu, CEO, Chief Engineer, Founder, Jing-Jin Electric
Dr. Yang Cao, Transmission Senior Supervisor, Jing-Jin Electric
The electrification of medium duty truck grows rapidly. JJE’s newest electric beam axle family can cover up to 11T (or class 6 in North America) trucks, including single-speed and 2-speed systems. Multiple advanced technologies are integrated into the electric beam system, such as bi-stable electromagnetic bi-directional shifting clutch, bi-stable eLocker, linear park lock system, and active cooling and lubrication. These functions’ control is all in the electric beam axle’s inverter, which is mounted on the axle. 800V, high power hairpin motor and SiC inverter are used to produce strong capacity, and high efficiency across wide operating range.
The 2-speed axle features a high efficiency hair-pin electric motor, a 400kW SiC inverter with “safe towing” feature, electro-magnetic shifted 2-speed gearbox, with neutral position that also serves as a disconnect, bi-stable differential eLocker, linear park lock system. With 2-speed gearbox, the beam axle’s wheel-end torque is up to 15,000Nm, and the maximum vehicle speed is over 160km/h. Integrated design for motor and gearbox reduces the axial length of the system.
JJE’s 2-speed beam axle features high performance and high output speed, with little power degradation at high speed. Its efficiency is high over a wide speed range – especially in comparison to a single speed axle thanks to the 2-speed gearbox.
Fig. 2 JJE Electric Beam at the Rear of a Truck Demonstrator
Fig. 3 JJE 2-speed Electric Beam Performance
Electric Motor
JJE has a mature hairpin motor designs to cover performance requirement of wide range of vehicles. For this electric beam axle system, the electric motor’s peak power reaches 420kW at 650Vdc, with 97.4% maximum efficiency, and over 90% of the efficiency map is above 88%. The water-oil combined cooling allows the electric motor to produce high continuous power.
2-speed Gearbox
The 2-speed gearbox provides high launch torque, high vehicle speed and high efficiency over broad duty conditions, and helps contain motor’s top speed for better reliability and durability. It also broadens high efficiency operating range, and significantly reduces thermal loading in the system at high speed. A 2-way, bi-stable electromagnetic clutch is used for shifting between 1st gear and 2nd gear, with neutral position. The neutral position is a natural “disconnect”. Combining this rear axle with neutral with a constantly powered front eAxle, the vehicle efficiency can be improved. JJE’s patented DirectFluxTM Bi-stable eLocker enhances functional safety of the locker and eliminate the power consumption. Proven park lock system is implemented on the motor shaft, or the “lowest torque” point of the system. An oil pump provides active oil lubrication, which allows low oil level in the gearbox, reduces gear churning loss.
SiC Inverter
The electric beam axle has an 850V SiC inverter integrated on it, with functional safety level up to ASIL D. Multiple functions − such as motor control, differential locker control, 2-speed transmission control, park lock control − are integrated in the inverter, taking advantage of inverter’s high functional safety control platform. With backup power supply, the inverter enables “safe towing”, a feature highly desired by customers. It is a critical safety redundancy in the event of 12V power supply loss.
DirectFluxTM Bi-stable Electromagnetic Clutch
Patented bi-stable electromagnetic clutch is JJE’s one of the most advanced technologies. It is used for gears shifting and locking the differential in the electric beam axle system. This technology has been successfully used as a differential locker in JJE’s 300kW SiC EDM and as a disconnect in JJE’s new AWD EDM.
DirectFluxTM electromagnetic clutch takes advantages of its innovative magnetic circuit design. Compared to the more conventional reluctance flux magnetic circuit design, the DirectFluxTM design greatly reduces flux leakage, and therefore utilizes magnetic flux more effectively to generate force. However, the conventional reluctance flux design cannot avoid magnetization of parts near flux circuit, or “flux leakage”, which causes less effective utilization of magnetic flux. As a result, DirectFlux acts 2-3 times faster than a reluctance flux design.
The bi-stable clutch is inherently fail-safe as it won’t change state in the event of loss of power. This feature gives bi-stable clutch a higher safety level than mono-stable clutch. For differential locker, it will prevent sudden locker release due to the loss of power or control failure. For transmission shift, it will prevent gear unexpected back to neutral which will lead the vehicle loss of traction. On energy consumption side, the bi-stable clutch’s feature of “zero holding current” eliminates holding current and in turn achieves zero power consumption.
In the development stage of an electromagnetic clutch, a software platform based on several simulation tools is built for more precise simulation result. This platform covers signal, electric, electromagnetic, and mechanical aspects. It addresses almost every detail, including software control, PCB layout, electromagnetic transient simulations, multi-body dynamic simulations, and strength. It provides strong support to the clutch’s development.
Electric beam axles are designed for pickup trucks, light duty trucks, or medium trucks. As the beam axles get electrified, a lot of traditional technologies no longer fit. JJE takes advantage of its knowledge in electric drive, strong R&D capabilities on motor, inverter, transmission and clutches and expertise in system integration, creating the 2-speed electric beam axle for the large medium truck segment.