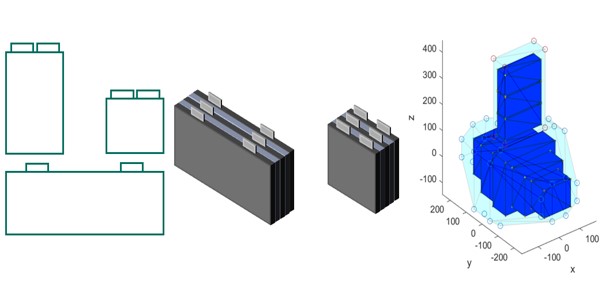
The installation space that is available for a battery system is usually a limiting factor regarding the possible capacity and power of a battery system. A battery cell which, in contrast to standard formats, is produced in variable sizes and formats can be advantageous, since it can be adapted to an individual installation space. The flexibility in the format of the cell results in new degrees of freedom and thus a large number of possible arrangements and interconnections of the cells in an existing installation space. This flexibility also results in an increase of the solution space and the solution variety, so that both the synthesis under consideration of different, function-relevant boundary conditions and the evaluation of the system properties are supported by the development of a method.
Figure 1: Pouch cells produced in different formats
Therefore, the authors present a method that enables automated optimization of the topology of a battery system based on the arrangement, function-relevant boundary conditions, interconnection logic, and resulting energy and power of the battery system.
Increased design solution space and complexity by usage of format flexible pouch cells
One of the main benefits of pouch cells is their simple casing using pouch bags. In contrary to cylindrical or prismatic cells produced in VDA standard formats they offer the possibility to be manufactured in various sizes and formats. Currently this approach is mainly used for customer electronics using only single cells. Applying this approach to battery systems with multiple cell modules as in electric vehicles, creates a number of degrees of freedom in the design of the battery system as well as increasing complexity during development of such a system.
On the one hand, the available installation space must be utilized in the best possible way in order to increase both the energy content and the potential performance of the battery system. Using cells of different formats offers potential, particularly in complex installation spaces. On the other hand, in this context, technical feasibility must be taken into account on both the product and production sides, and a reasonable degree of flexibility must be defined. In particular, the interaction of the cell and module shape with the potentially necessary temperature control system and mounting system must already be taken into account during the design space optimization.
In addition to challenges in positioning and sizing of cooling components and cells another challenge has to be considered resulting from different electrical properties of the cells. Different formats of the individual cells lead to different cell volumes and therefore to different capacities and resistances of the individual cells. A connection of cells with different properties can lead to unequal load distribution between the cells and therefore unequal heat generation as well as unequal state of charge developments which can limit the usable energy and power of the battery system. These facts limit the possibilities of connections between different modules which have to be taken into account during investigation of different connection topologies. These connection topologies can consist of different parallel and series connections of all available modules possibly restricted by different voltage levels and distances between the modules. This challenge therefore makes a combined mechanical and electrical approach inevitable.
A new approach for synthesis and evaluation of cell assemblies with pouch cells of different format
In the current state of research there are already some approaches that consider installation space optimizations of battery systems with respect to different aspects such as mechanical properties of the housing structure [1], thermal and electrical properties of the battery system [2] or overall product properties as power or weight distribution [3]. However, the current state of research does not offer any approaches that demonstrate the potential of the usage of a pouch cell produced in a format-flexible manner and also enables this potential by a method for optimization during the design process of a battery system. The new overall approach presented in this article is shown in Figure 2.
Figure 2: Overall approach of topology optimization of a cell assembly
For an initial parameterization of the model, a number of parameters have to be defined based on the specific application scenario. A definition of the battery systems voltage level, maximum module voltage, cell thickness and additional parameters regarding the installation space of the cooling system such as the cooling plate thickness and amount are necessary before starting the installation space optimization. In addition, potential size restrictions in production of the cells can be defined. After definition of the available installation space a scan of the installation space is performed for all spatial directions with a defined increment representing a modules thickness, to determine the maximum possible lengths and widths of the battery system. Based on this information multiple potential module arrangements are generated.
Based on each generated module arrangement module properties are defined. To increase the solution space each module can exist with two different voltage levels and regarding different capacities. The capacity is defined based on the cell volume of each individual module. For each module arrangement an analysis of potential electrical interconnections is done. In a first step, the interconnections are evaluated based on the distance between the interconnected modules. Secondly, they are evaluated based on their feasability regarding the modules and systems voltage level.
In a final step each feasible interconnection topology is evaluated based on its usable capacity and load distribution between the different parallel paths of the topology with respect to maximum c-rates of the cells and unequal state of charge developments. An optimal solution is found by synthesis and evaluation of multiple module arrangements and interconnection topologies.
The presented method offers a possibility for battery system optimization using format flexible pouch cells in an early stage of product development. Main challenges result from property differences of the individual cells. An ideal solution of usable capacity as well as load distribution between the different topology parts has to be found to avoid safety, balancing and cost issues.
Acknowledgements
This work was funded by the Baden-Württemberg Ministry of Science, Research and the Arts within the project “AgiloBat” as part of the Innovation Campus Mobility of the Future.
M.Sc. Philip Müller-Welt (Doctoral Researcher)[1], M.Sc. Konstantin Nowoseltschenko (Doctoral Researcher)[1],
Dipl.-Ing. Katharina Bause (Head of Research Department Drive Systems and Clutch and Tribology Systems)[1],
Dipl.-Ing. Sascha Ott (Managing Director Institute of Product Engineering and KIT Center Mobility Systems)[1] and
Univ.-Prof. Dr.-Ing. Dr. h. c. Albert Albers (Head of Institute of Product Engineering)[1]
1 IPEK – Institute of Product Engineering at Karlsruhe Institute of Technology (KIT), Kaiserstr. 10, 76131 Karlsruhe,
philip.mueller-welt@kit.edu
Literature
[1] D. Wagner, „Methodengestützte Entwicklung eines elektrischen Energiespeichers zur
Erschließung von Leichtbaupotenzialen als Beitrag zur Produktgenerationsentwicklung“.
Dissertation, Institut für Produktentwicklung (IPEK), Karlsruher Institut für Technologie
(KIT), Karlsruhe, 2015.
[2] F. Frank, „Optimierter Hochvoltbatterieentwurf hinsichtlich mechanischer, thermischer
und elektrischer Randbedingungen unter Berücksichtigung der Produktionskosten“. Dissertation,
Universität Duisburg-Essen, Duisburg, 2018.
[3] K. Kuchenbuch, T. Vietor und J. Stieg, „Optimierungsalgorithmen für den Entwurf von
Elektrofahrzeugen“, S. 548–551, doi: 10.1365/s35148-011-0128-7.