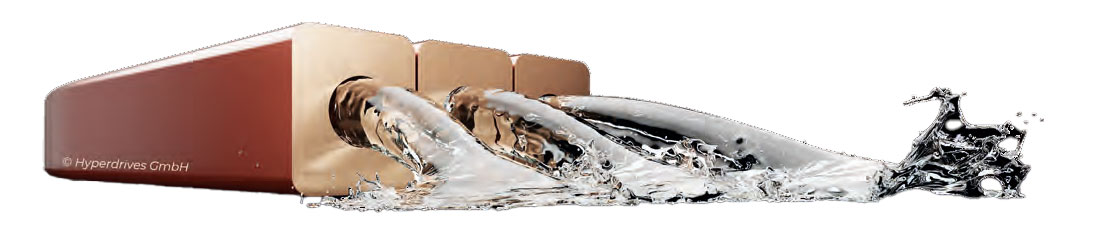
Michael Numberger, CTO, Hyperdrives GmbH
Hyperdrives’ hollow conductor technology improves stator cooling for electric motors by an order of magnitude, achieving exceptional power density and efficiency. Seamless integration of proprietary manufacturing processes into existing hairpin stator lines makes it ideal for high-volume automotive, heavy-duty and aerospace applications.
Introduction and objectives
The ongoing electrification in the automotive sector and other industries demands a new generation of electric drives that are more powerful, efficient, and cost-effective. A central challenge is thermal management, as high power densities must be combined with more efficient heat dissipation. Hyperdrives‘ hollow conductor technology presents a novel solution for stator cooling, boosting both power density and efficiency while reducing motor production as well as operational costs. This article aims to present the technical innovations, performance capabilities, and application areas of this technology.
Technical basis
Hyperdrives’ technology utilizes hollow copper conductors, focused on optimizing the heat flow between cooling fluid and copper winding. At maximum torque, over 90% of total motor losses are attributed to the copper winding. Hyperdrives achieves an unprecedented low copper-to-coolant temperature gradient by leveraging several key design features:
- Direct coolant-to-copper contact:
The hollow conductors allow the cooling fluid to be in direct contact with the copper conductors’ inner channels’ surface, enabling direct heat dissipation precisely where it is generated. - Hollow pin topology:
Defined and even hollow channels, typically between 1 and 2mm in size, are engineered to maximize cooling surface area and facilitate consistent fluid flow and heat transfer at all sections of the winding. - Decoupling of electric and hydraulic connection:
Optimization of the hydraulic cooling fluid flow path independent from the electrical winding layout. - Low-viscosity cooling fluid:
Hyperdrives employs a low-viscosity dielectric oil as the cooling fluid, combining water-like viscosity with electrically insulating properties. By solving the pressure drop challenge – maintaining a minimal pressure drop of less than 1 bar – Hyperdrives enables the use of standard, cost-effective pumps with minimal energy consumption instead of specialized, high-cost and high energyconsuming alternatives. - High-velocity, turbulent fluid flow:
The cooling fluid moves at high velocities, promoting turbulent heat transfer with a heat transfer coefficient (HTC) exceeding 2,000 W/m²K. This turbulence intensifies cooling by enhancing heat dispersion from the copper surface.
Together, these features enable superior stator cooling by precisely and uniformly dispersing heat across the copper windings. With cooling integrated directly through the hollow conductors, there is no need for a conventional water-cooled jacket, freeing up valuable installation space around the stator. This allows for a more compact motor design or can be leveraged to increase torque output by enabling a larger airgap diameter and optimized stator geometry. Hyperdrives motors can handle ultra-high current densities of up to 75 Arms/mm² copper cross section in steady-state operation, pushing the boundaries of motor performance. The entire cooling circuit, including both the inverter and motor in one circuit, remains compact and low-cost, offering a highly efficient, space-saving, and economically competitive solution for high-demand, high-volume applications.
Comparison with conventional stator cooling
Compared to state-of-the-art water-jacket plus spray-oil cooled hairpin stators, Hyperdrives’ hollow conductor technology enhances heat dissipation by a factor of 10 and boosts continuous current density by a factor of 3 (75 vs. 25 Arms/mm² continuous). This breakthrough enables the system (motor incl. inverter) to achieve peak power densities up to 15 kW/kg and over 12 kW/kg continuous. All while using standard materials without relying on costly Cobalt-Iron laminates, or 3D-printed windings. By achieving these results with conventional materials, the established inner runner motor topology and proven manufacturing techniques, Hyperdrives sets a new benchmark for performance-to-cost in electric motors.
Efficiency gains and customer benefits
Optimal motor sizing for maximum efficiency is unique to each application and should be evaluated on system level rather than focusing solely on the motor. In aviation, for example, weight savings can take precedence over pure peak efficiency. Hyperdrives’ technology enables groundbreaking designs by shifting conventional thermal boundaries, making it possible to achieve maximum efficiency exactly where it matters most. For the majority of automotive, heavy-duty, and aerospace applications, this is part-load. The enhanced motor efficiency characteristics can yield up to a 10% improvement in energy onsumption and range. These efficiency gains translate into significant lifetime cost savings and deliver clear customer benefits.
Mass production and cost reduction
One of Hyperdrives’ key advantages in using hollow I-pins and hairpins is its compatibility with existing automotive hairpin stator manufacturing processes, which enables full automation, fast scaling and cost-effective integration in existing production lines. Hyperdrives’ proprietary methods for joining hollow pins and sealing the cooling manifold fit seamlessly into current production workflows, reducing conversion costs and simplifying adoption in mass production.
Distributed stator windings enhance compatibility with all available rotor topologies, offering increased design flexibility, especially for cost-sensitive applications. Rare-earth magnets can be optional, mitigating potential geopolitical dependencies and tackling the environmental aspect.
Durability and reliability
Hyperdrives has successfully completed extensive testing to validate the durability and reliability of its technology. Test specimens have demonstrated extreme robustness by withstanding rigorous heavy-duty shaker tests, followed by 25,000 full thermal cycles and pressure pulses, effectively simulating ten years of daily use. This testing confirms that Hyperdrives’ cooling system is engineered for long-term performance, ensuring reliability and robustness under real-world conditions in demanding applications.
Market model and commercial application
Hyperdrives’ system not only maximizes performance but also minimizes production complexity and cost. This makes it ideal for large-scale deployment across automotive, heavy-duty, and aerospace sectors, providing a scalable solution that meets the rigorous demands of these industries without compromising on quality or efficiency. Hyperdrives follows two business models: direct sales of complete systems for customers with low-to-medium production volumes and technology licensing for large-scale manufacturers. Leveraging on close partnerships with industry innovators, along with established production processes, both models remain cost-effective and scalable.
Product specifications and outlook
Hyperdrives now offers an integrated silicon carbide (SiC) inverter and ready-to-go motor control with its motors. The development of the Hyperdrives ONE model, aimed at automotive applications, has been successfully completed. Building on this achievement, Hyperdrives has initiated the development of Hyperdrives ULTRA, a model tailored to meet the rigorous demands of aircraft applications.
The Hyperdrives team is excited to connect with potential partners and clients to discuss custom development of drive systems tailored to your specific application using our versatile and scalable technology. Whether the need is for high-speed or high-torque direct drives, our team is ready to collaborate and create a solution that meets your unique requirements. Reach out to us at info@hyperdrives.de to explore how we can support your project with cutting-edge, adaptable drive technology.