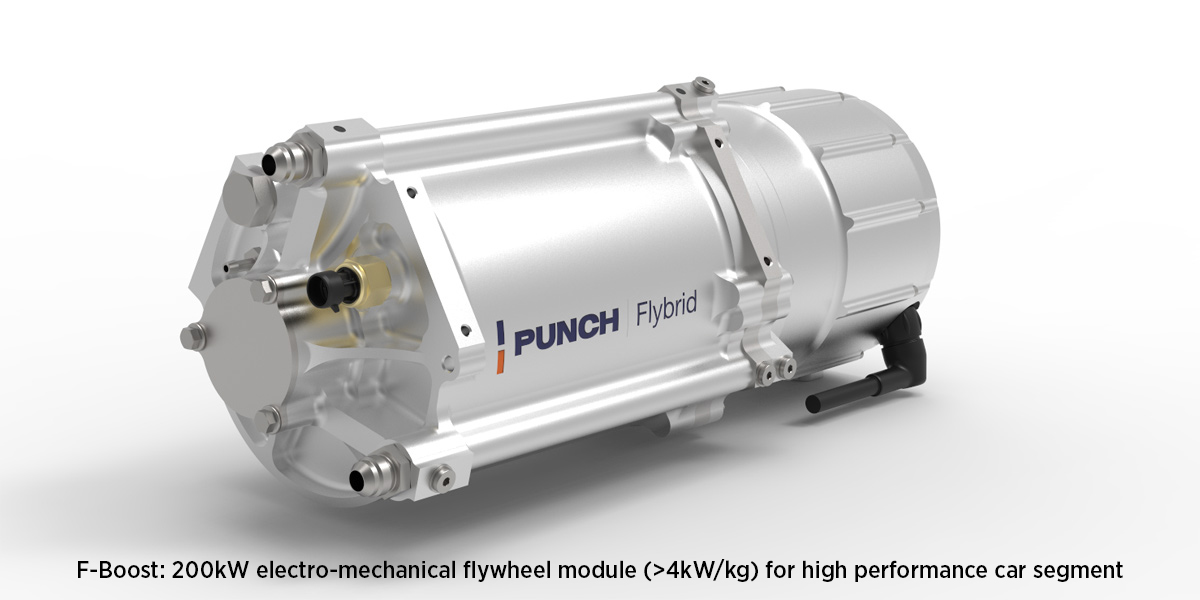
A new generation of modular electro-mechanical flywheel energy storage systems are being developed for integration into different vehicle types and powertrain architectures. The ultra-high-power density of the flywheel provides an effective hybrid solution for conventional ICE powered vehicles and is equally suited to hybridise the battery energy storage system on board already electrified vehicles such as BEVs and PHEVs.
The integral flywheel, electric motor and inverter exceeds ‘state-of-the-art’ performance levels for power density of energy storage systems, by exploiting new compact, high-performance electrical machines. While the concept of an electro-mechanical flywheel system is not new, previous concepts have relied on expensive be-spoke rotor designs. The PUNCH Flybrid system combines the flywheel rotor with conventional motor technology but running at very high-speeds. The direct drive design results in an ultra-compact, efficient and thermally robust energy storage system that can be readily scaled to different energy and power levels according to the intended application. The high-performance energy storage solution can be readily integrated into any electrified vehicle with exceptional cost vs. benefit ratios supporting current automotive industry trends. By connection to a hybrid transmission or the DC-bus of a BEV, the F-Boost flywheel system can be seamlessly integrated into many varied powertrain types.
For the high-performance segment, a 200kW, 1MJ version of the F-boost system has been created. With a total mass of 50kg and a package volume of under 12l, the flywheel is very competitive both in terms of its gravimetric and volumetric power density, with the latter being crucial for the tight packaging constraints typically encountered on modern high-performance cars.
Peak system power is available from 10 to 100% SOC in both charge and discharge, meaning the flywheel can maximise brake energy recovery during high performance driving, typically characterised by short high-power braking events. A combined motor-inverter peak efficiency exceeding 97% and low parasitic losses achieved by running the flywheel and motor in a vacuum, mean the flywheel can achieve high roundtrip efficiencies consistently, maximising energy return and performance boost. Additionally, the low losses mean that the flywheel has a relatively low heat rejection requirement and because the flywheel is tolerant to high temperatures, cooling can be achieved with a water-glycol based coolant running at ~70°C.
A patented rotor bearing support system coupled to accurate balancing gives the flywheel exceptional NVH characteristics while multiple safety design features guarantee safe in vehicle operation even in the event of a crash. The flywheel is designed to satisfy the harshest of vehicle usage patterns, and unlike other electrochemical based energy storage systems does not suffer from calendar-based degradation. An on-board flywheel health monitoring system constantly ensures that the flywheel is operating safely and efficiently.
Applications
1. Hybrid Energy Storage for High performance BEV
The push towards electrification across multiple transport sectors has seen the emergence of advanced Li-Ion battery storage. However, the focus has generally been on improving energy density for greater range and autonomy. In applications with dynamic duty cycles, frequent transient high-power events can pose a significant challenge to the battery, leading to oversized units solely to satisfy the peak power requirement and reduce premature degradation of performance. The inclusion of high-power energy storage such as flywheels can reverse this trend leading to an energy storage system with an optimised power-to-energy ratio, minimising mass, volume and extending system life.
PUNCH Flybrid has fitted one of its electro-mechanical systems to a demonstrator vehicle based on a PHEV Ford Transit van. It has been shown that adding a flywheel can improve the van’s EV-range by up to 40% on certain drive cycles through increased regen braking capability, while power assistance from the flywheel during high power transient manoeuvres reduced peak battery C-rates from 9C to 3C. Likewise, for the high-performance car segment the flywheel can be used to load-level the battery system to reduce its likelihood to de-rate due to thermal limits. Additional recovery and deployment of energy during aggressive driving can also be used to momentarily boost vehicle performance such as when exiting a corner or overtaking.
(a) F-Boost rapid prototype model held by PUNCH Flybrid engineer next to PHEV Transit Van vehicle. (b) During a typical fast lap of the Nürburgring, a performance BEV fitted with an F-boost module can recover an additional 40% energy.
2. H2-ICE Hybridisation
PUNCH Torino and PUNCH Flybrid are also exploiting the flywheel in conjunction with a H2-fuelled ICE coupled to a series hybrid transmission for heavy duty vehicles. While the passenger car market is moving rapidly towards increased levels of vehicle electrification as a means of reducing CO2 emissions, the requirement of heavy and expensive batteries makes this inefficient for heavy vehicles with large energy requirements such as HGVs and buses. For these types of vehicles hydrogen offers a more cost-effective decarbonisation route. Recent years have seen renewed interest in H2-fuelled ICEs as alternatives to fuel cells as these can leverage an already existing production infrastructure, servicing network and skilled workforce. When combined with their lower initial purchase cost, this places H2-fuelled ICEs very favourably in terms of Total Cost of Ownership (TCO). Extensive work by PUNCH Torino, who are currently in advanced stages of developing a H2-fuelled ICE, shows that for hybridised machines the engine operation can be more easily constrained to the optimal region making their overall efficiency comparable to fuel cells in real world operation. For these applications, the high-power density of the flywheel system and its ability to be repeatedly charged and discharged over thousands of cycles without suffering from performance degradation is key.
(a) The addition of a flywheel hybrid system in conjunction with a series type transmission enables the H2-ICE to predominantly operate at peak efficiency. (b) Typical vehicle and flywheel speed profile for an-track driving scenario: the flywheel is robust to frequent high-power charge-discharge cycling.
Author:
Tobias Knichel – Managing Director – PUNCH Flybrid Ltd – Tobias.Knichel@punchflybrid.com
As the Managing Director, Tobias Knichel focuses PUNCH Flybrid’s activities on energy recovery systems for mobile and stationary applications to reduce wasted energy.