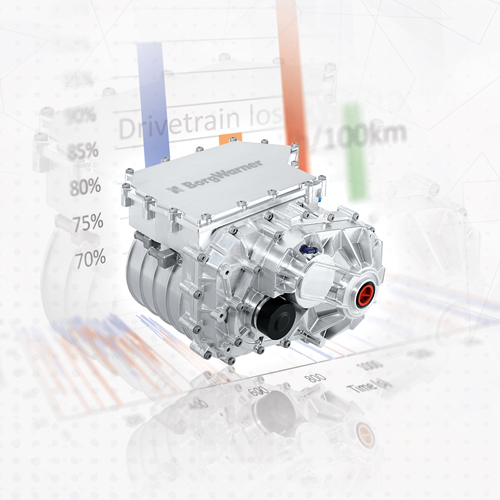
Matthew Vanderlip, iDM Solutions Architect & Manager, System Strategy & Platform Engineerings, BorgWarner
Efficient system integration for the EV market
With an ever-growing trend towards electric propulsion there is also an increasing demand for flexible electrification components that meet the requirements of different vehicle architectures. By permanently enhancing the portfolio through development of innovative technologies and acquisitions that contribute to the company’s expertise, BorgWarner has positioned itself to accelerate its growth in electrification products and drivetrain solutions.
The latest generation of BorgWarner’s integrated Drive Module (iDM), for example, is easy to fit, tested and correlated, and it supports automakers in their design of efficient hybrid and electric vehicles. Based on common architecture, it combines power electronics, electric motor, and mechanical components within one single eAxle unit enabling the fast development of primary and secondary propulsion applications and helping manufacturers to comply with strict sustainability demands and emissions rules.
Developing and improving the solution
With its capability to design, test and manufacture complete electrification systems for passenger cars as well as commercial vehicles, BorgWarner can perform motor, power electronics, drivetrain, and software design in-house to develop fully optimized and highly integrated system solutions for a wide range of applications.
BorgWarner’s first iDM system platform, the iDM200 developed in 2018, utilizes the 200mm outer diameter hairpin motor HVH200 with an interior permanent magnet (IPM) rotor, which was designed to target performance requirements ranging from 80 to 150kW. The next step was the development of a new iDM system for larger, more powerful vehicle applications. The iDM220 platform is intended for operations in the 150 to 250kW power range when utilized in 400V systems, or up to 500kW in 800V form. For this, a new HVH220 (220mm outside diameter) machine was designed. The new HVH220 concept right-sizes the conductors to bring the current density back to an ideal range to match the iDM220’s innovative oil cooling strategy. This enabled an average power consumption reduction of 250W over the WLTC (World harmonized Light-duty vehicles Test Procedure) drive cycle, representing a 22% improvement.
Cooling system a question of performance requirements
Another important aspect of the iDM system development is its cooling design as it can be leveraged to reduce overall costs by allowing the use of smaller, power-dense motors and electronics. System cooling is critical to extracting the most performance out of the iDM while keeping cost under control. Therefore, BorgWarner has developed both water-cooled and oil-cooled solutions.
Lowest system costs – while still complying with performance and package requirements – are achieved by combining the inverter and motor cooling circuit. Typically, the motor is part of the water ethylene-glycol (WEG) circuit after the power electronics and cooled via a water jacket which encircles the stator. This cooling approach is limited by the surface area of the stator’s outer diameter, relying on conduction from the heat source through the stator laminations to the WEG mixture.
When a higher performance is requested, direct oil cooling becomes a more interesting solution for thermal management. Utilizing the gearbox oil to cool the motor can improve heat transfer and therefore the total heat rejection of the system, thus increasing its performance. However, an electric pump is needed to achieve the flow rates required for effective oil cooling, which adds to the system cost and complexity. Also, the oil is now being used as a sink for more heat therefore an oil cooler is often added to keep oil temperatures within operating range. But the cost of these components can be balanced against savings on the electric machine. Furthermore, oil cooling solutions include novel design features to minimize system losses through the elimination of high-speed seals and gear-set churning. This approach also utilizes direct rotor oil cooling to extract heat from the core of the electric motor thus enabling higher torque and power density. These benefits lead to vehicle-level improvements in range or opportunities to reduce battery size resulting in a net benefit.
Flexible platform
By using a building-block approach, each iDM system is designed to be flexible in terms of its motor winding configuration and stack length, power module selection, gear ratio and cooling. This allows solutions to match customer performance and packaging needs without having to start from a blank sheet, resulting in faster execution and reduced cost. In addition to the base functionalities, system add-ons have been developed and can be optionally integrated including park, disconnect and torque-vectoring systems.
Electronics portfolio expansion
With the acquisition of Delphi Technologies in 2020, BorgWarner has strengthened its position in electrification by expanding its product portfolio. Among these new technologies, the Viper family of power devices enable significant advances in BorgWarner’s system development capability. The Viper silicon or silicon carbide versions offer system designers a solution to cover nearly all power levels in both 400V and 800V systems. The devices take advantage of dual-sided cooling to maximize silicon utilization. Dual-sided cooling enables up to 50% reduction in semiconductor area for the same performance. Viper modules also eliminate the need for wire bonds, which improves product yield and reliability. The power modules are physically the same size, which enables interchangeability within a given packaging space. This allows system solutions to be developed using common building-blocks that can be tailored to match the required system performance. Among the Viper product family are SiC MOSFETS with both 750V and 1200V ratings. These devices enable over 50% inverter loss reduction compared to their Silicon IGBT counterparts for those applications demanding the highest efficiency.
System integration
By developing the new IPM motor solution with a 220mm outside diameter, combining that with the appropriate Viper power module and integrating it into a gearbox utilizing a low-loss parallel layshaft gear reduction with a high efficiency oil cooling and lubrication strategy system, designers are able to reduce the average WLTP system power consumption by nearly 700W at 60°C. The combination balances system performance as well as costs and allowed to successfully build and deliver the first two system variants of BorgWarner’s new iDM220 drive unit. The first system with a peak power of 170kW and the second system with a peak output of 225kW.
NVH improvements
With performance targets achieved as described above, specific tools were developed and implemented into the design, analysis, and testing processes to optimize features crucial for the NVH behavior. Thus, lightweight design objectives could be met while housing deflection and dynamics were improved at the same time. At the transmission level, unique design solutions securing gear strength and durability simultaneously minimize gear mesh transmission errors for better NVH. Furthermore, the design process resulted in an optimization of electromagnetic torque ripple in the e-machine and reduced radial forces along with enhanced performance in total output torque and efficiency.
Summary
By integrating a state-of-the-art transmission along with electric motor and custom power electronics, BorgWarner’s iDM can support the automotive industry in its development of cleaner and more efficient passenger cars and commercial vehicles. The modular approach to system integration and development means that BorgWarner can offer customers a solution that will fit nearly any vehicle need, providing compact, lightweight, and efficient components. Each application can draw from the sub-system portfolio to be customized while still using tested building blocks to reduce cost, risk, and time-to-market. The iDM is an innovative solution that helps automakers reduce their electric vehicles’ energy consumption and increase pure electric reach per battery charge.